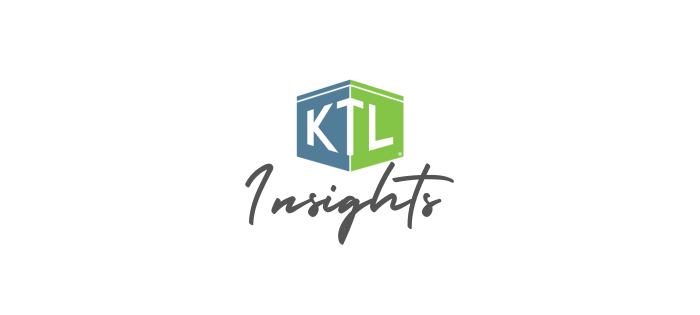
Comments: No Comments
OSHA Safe + Sound Week: August 15-21, 2022
According to the Occupational Safety and Health Administration (OSHA), “Safe workplaces are sound workplaces.” An organization’s safety culture is ultimately reflected in the way that safety is managed in the workplace, and having a strong safety and health program can help create:
- Fewer accidents, losses, and disruptions by preventing workplace injuries and illnesses
- Engaged employees and improved morale
- Increased productivity and enhanced overall business operations
- Lower workers’ compensation and insurance claims
- Improved compliance with OSHA regulations
- Improved reputation to attract new customers and employees and retain existing ones
- Better brand and shareholder value that tie to social responsibility
These benefits are precisely why the OSHA created Safe + Sound as a year-round campaign: to encourage every workplace to develop, implement, and maintain a safety and health program.
Safe + Sound Week
One week out of the year—August 15-21, 2022—OSHA promotes a nationwide “Safe + Sound Week” to recognize the successes of workplace health and safety programs, offer information and ideas on how to keep America’s workers safe, and encourage America’s workplaces to commit to workplace safety and health.
OSHA recommends that every workplace have a safety and health program that includes the following three major areas:
- Management leadership. Management must provide the leadership, vision, and resources needed to implement an effective safety and health program. This means that business owners, managers, and supervisors commit to:
- Making worker safety and health a core organizational value.
- Eliminating hazards, protecting workers, and continuously improving workplace safety and health.
- Providing sufficient resources to implement and maintain a strong safety culture.
- Visibly demonstrating and communicating their ongoing commitment to safety and health.
- Worker participation. Engaging workers at all levels in establishing, implementing, evaluating, and improving safety and health in the workplace creates buy-in. Workers are a valuable partner in making the workplace safer, and maximizing participation (without risk of retaliation) allows everyone to feel invested in the program.
- Systematic approach to finding and fixing hazards. Finding and fixing hazards in the workplace is an ongoing process to better identify and control sources of potential injuries or illnesses. This can involve establishing procedures to collect and review information about known or potential hazards, investigating the root cause of those hazards, and prioritizing hazard controls. This continual process ensures that workers go home to their families safe and sound every night.
KTL’s Series on Investing in Safety
Throughout OSHA’s Safe + Sound Week (August 15-19), KTL will be featuring a series of articles and posts on our blog and social media (i.e., Facebook, LinkedIn, Twitter) reinforcing these concepts from OSHA and discussing why businesses should invest in safety. Topics will include the following:
- Where is your company on its safety journey?
- Top employee safety concerns and why they need to be heard
- Worker compensation audits, what to expect, and how you can save money
- Behavior-based safety – what is it?
- Benefits of a third-party safety audit
Watch for these articles! And for more information on Safe + Sound and what your organization can do to participate and promote a strong safety culture, visit https://www.osha.gov/safeandsound.
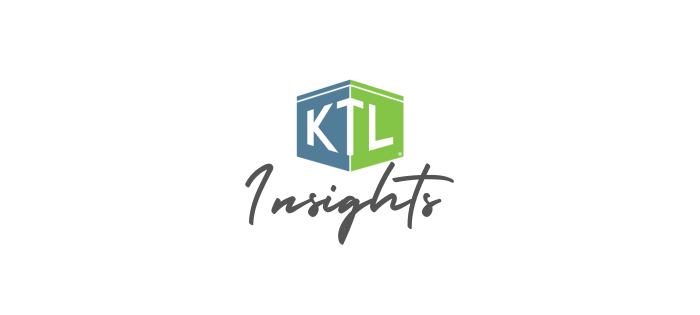
Comments: No Comments
June: National Safety Month
Strong safety performance is a cornerstone of any business. Implementing and enforcing health and safety policies and safe work practices is essential to ensure that the organization does not endanger the health or safety of workers, communities, or customers. More often than not, strong safety performance also makes the difference in being qualified to provide services to customers or being able to sustain/expand the business.
June is National Safety Month. Observed annually by the National Safety Council (NSC), the nation’s leading nonprofit safety advocate, National Safety Month focuses on “saving lives and preventing injuries, from the workplace to anyplace.”
Where to Start
This year, NSC has chosen the following weekly topics to highlight during National Safety Month:
- Week 1 – Musculoskeletal Disorders (MSDs): MSDs are a leading cause of workplace injury and cost billions each year in workers’ compensation and lost productivity.
- Week 2 – Workplace Impairment: More than 90% of employers agree that fatigue, mental distress, and stress can cause workplace impairment, in addition to drug misuse.
- Week 3 – Injury Prevention: In 2020 alone, more than four million workplace injuries required medical attention in the U.S., resulting in more than $643 billion in costs.
- Week 4 – Slips, Trips, and Falls: Falls are the second-leading cause of unintentional injury-related death and the most frequently cited standard on the Occupational Health and Safety Administration’s (OSHA) top 10 list for the eleventh year in a row (see below).
OSHA’s Top 10: FY 2021
Beyond the topics NSC has chosen to highlight for this year’s National Safety Month, OSHA’s list of the top 10 most frequently cited standards is an excellent place for any organization to focus their attention. OSHA publishes this list each year to help employers take the appropriate steps to find and fix recognized hazards before they experience a workplace injury and/or before OSHA shows up for an inspection.
OSHA’s top 10 for FY 2021 includes the following:
- Fall Protection, construction (29 CFR 1926.501)
- Respiratory Protection, general industry (29 CFR 1910.134)
- Ladders, construction (29 CFR 1926.1053)
- Hazard Communication, general industry (29 CFR 1910.1200)
- Scaffolding, construction (29 CFR 1926.451)
- Fall Protection Training, construction (29 CFR 1926.503)
- Control of Hazardous Energy (lockout/tagout), general industry (29 CFR 1910.147)
- Eye and Face Protection, construction (29 CFR 1926.102)
- Powered Industrial Trucks, general industry (29 CFR 1910.178)
- Machinery and Machine Guarding, general industry (29 CFR 1910.212)
Many workplace injuries, illnesses, and deaths that occur in workplaces are related to these top 10 cited standards—and many could be prevented with adequate resources and attention. That is why it remains critical for organizations to continue developing and promoting strong safety and health programs, as well as educating and training workers in safety awareness.
For more information on National Safety Month, visit https://www.nsc.org/workplace/national-safety-month.
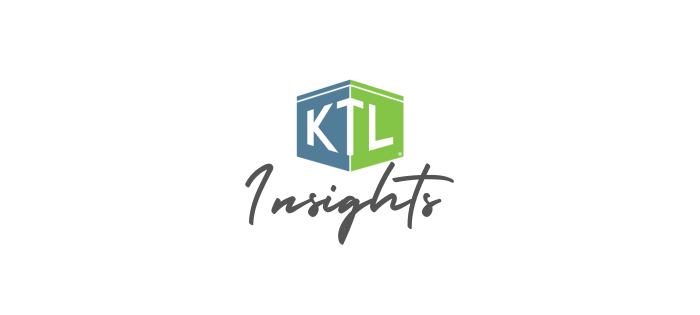
Benefits of an Integrated Management System
According to the International Organization for Standardization (ISO), are currently more than 80 Management System Standards (MSS)—80 different standards designed to help companies improve their performance across a diverse range of areas and sectors.
Most companies these days have some sort of management system, whether formal (e.g., ISO, Global Food Safety Initiative (GFSI)-benchmarked standard, industry-specific) or informal. And, because most companies have various aspects and functions to their operations, many actually may have more than one system to organize processes and business objectives.
While management systems by ISO’s definition are designed to “help organizations improve their performance by specifying repeatable steps that organizations consciously implement to achieve their goals and objectives,” having multiple systems to manage often overlapping requirements (i.e., regulatory, certification, supply chain, internal) can create redundancies, inefficiencies, extra work, and overall confusion.
Integrated Management Systems: The Basics
A management system is the organizing framework that enables companies to achieve and sustain their operational and business objectives through a process of continuous improvement (i.e., Plan-Do-Check-Act). It is designed to identify and manage risks through an organized set of policies, procedures, practices, and resources that guide the enterprise and its activities to maximize business value.
A management system should be a means to better align operational quality, safety, environment, food safety, security, energy, etc. with the business. An integrated management system does just this. It aligns an organization’s various systems and processes into one complete framework, enabling the organization to work as a single unit to implement specific best practices organization-wide, fulfill the requirements of multiple standards, and meet a unified set of business objectives.
Integration Business Benefits
Ultimately, the various MSS have many common points—and all work towards the goal of making the organization more effective and efficient. Developing an integrated management system allows organizations to align the standards, find common management system components (e.g., terminology, policies, objectives, processes, resources), and add measurable and recognizable business value, including the following:
Greater consistency. An integrated approach creates greater consistency across business facets when it comes to terminology, processes, procedures, expectations, etc., and, in turn, greatly improved focus on a common set of business objectives. With an integrated system, organizations can ensure that processes, methods, and practices are in place, documented, and consistently applied across the entire organization. A common documented framework such as this helps alleviate duplication of efforts, allows for a more complete view of the functional needs of the entire organization, and reduces variability in performance.
Optimized processes and resources. Integrated systems allow companies to optimize processes and resources and, subsequently, reduce the time it takes to do certain activities. Integrated management systems help organizations to maintain requirements and associated documents concurrently—particularly through use of an information system—streamlining the process and allowing the organization to focus on improvements rather than maintaining multiple systems. A common system enables better use of resources and better collaboration and communication across the company.
More strategic approach. Organizations can take a more strategic approach with an integrated management system because it focuses on managing all aspects of the business, not just one area. It provides clear methods and processes to identify and prioritize risks, set and monitor goals, communicate risks to employees and management, and allocate appropriate resources to mitigate them. It also establishes a common language among managers, executives, and employees, which enables better goal setting, priority ranking, and allocation of resources. As a bonus, integrated systems also make it much easier to implement an organization-wide information system capable of tracking and reporting on common activities and key performance metrics.
Forward-thinking. More and more organizations are expecting more from the companies they work with—and that includes management systems. The push for best practices over just regulatory compliance is a growing trend. Reliable and effective regulatory compliance is commonly an outcome of consistent implementation of a management system. Beyond that, an integrated management system allows organizations to more effectively manage those risks (i.e., compliance, financial, legal liability, brand reputation) that can significantly impact the entire supply chain.
Help from the Standards
Standards organizations such has ISO are making it as easy as possible to implement an integrated management system—whether formal or informal—because, plain and simple, it just makes business sense. For example, ISO has adopted a Harmonized Structure (formerly known as High-Level Structure) to make sure every ISO MSS is structured in the same way with ten universal sections. The ISO MSS also use Annex SL, which dictates how the MSS should be written and, again, is consistent across the various MSS. These efforts simplify use, streamline protocol, and encourage standardization across the ISO MSS.
Beyond that, ISO has published a Guide to Integrating Management System Standards (revised in 2018) to help organizations implement integrated management system design—ISO or not. According to Michael McLean, Convenor or the ISO working group that developed the handbook, “Many organizations benefit from multiple management systems to help them ensure their systems and processes are in line with their objectives and help them maintain their business model through ever-changing environments. This handbook provides a practical guide for organizations to effectively align their management systems with their strategies, plans, and operations.”
Taking the Next Steps
If you are operating with multiple management systems—or even if you have no management system at all—there are some basic steps to creating an integrated management system:
- Invest the time to understand the current scope of operations, functional departments, compliance requirements, governance structure, etc. across the entire organization as a whole, not just siloed departments.
- Conduct a gap assessment to evaluate the current (“as-is”) condition of any formal or informal management system(s) against the desired (“to-be”) condition (e.g., ISO, GFSI, industry-specific).
- Create a development and implementation plan outlining tasks and resources required to close any identified gaps and achieve those objectives.
- Determine key components of the integrated management system required to achieve business objectives.
- Identify common elements to be standardized and incorporated into an integrated system (e.g., policies, procedures, processes, metrics, training).
- Determine what information technology can support and streamline an integrated management system.
- Provide relevant training to all interested parties to truly operationalize the management system across the organization.
Whether formal or informal, integrated management systems provide organizations—both big and small, in any industry—a pillar for sustainable growth. By developing and implementing an aligned management system, organizations can achieve more consistent, reliable, and efficient performance across many areas, while adding measurable and recognizable business value.
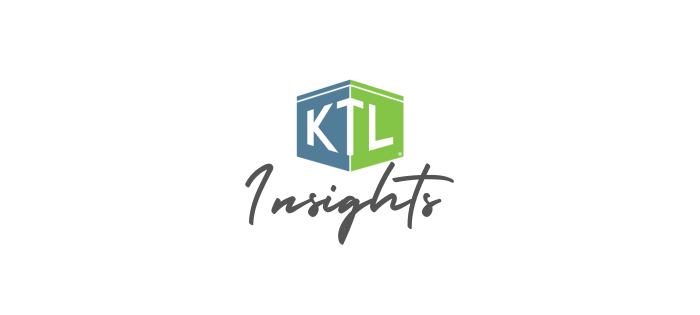
Comments: No Comments
Controlling Combustible Dust: Focus on Food
There is a wide range of agricultural and food products that create fire and explosion risks and hazards, including flour, grain, sugar, spices, cereal, flavoring additives, and many more. Dusts produced in any industry present challenges, but when manufacturing and processing food products, dusts can create the following major threats:
- Airborne dust can cause serious harm to human (employee) health by causing physical ailments ranging from dermatitis to occupational asthma to lung cancer.
- Dust can create the potential for cross contamination and encourage the spread of pathogens and allergens within the food processing plant.
- Dust may become combustible and serve as the source for explosions that harm workers, damage machinery, and destroy buildings/corporate reputation.
About Combustible Dust
The food industry is responsible for the largest percentage of combustible dust incidents in the U.S.—ranging anywhere from 24-43% depending on the timeframe and the source. One of the most notable combustible dust incidents in history involved a secondary explosion at the Imperial Sugar refinery in 2008, which killed 14 people and injured 40.
According to the Occupational Safety and Health Administration’s (OSHA) definition, combustible dust is “a solid material composed of distinct particles or pieces, regardless of size, shape, or chemical composition, which presents a fire or deflagration hazard when suspended in air or some other oxidizing medium over a range of concentrations.”
A dust explosion occurs when all five elements of the Dust Explosion Pentagon are present:

- Ignition source
- Oxygen
- Confined area
- Suspended cloud
- Explosive dust
Combustible Dust Standards
The devastating 2008 sugar refinery explosion prompted the development of OSHA’s Combustible Dust National Emphasis Program (NEP), and yet, some 14 years later, there is still no combustible dust regulation. That doesn’t mean, however, that there are no standards for managing and controlling combustible dust. In fact, there are several agencies involved in ensuring the food industry is appropriately managing the various hazards associated with combustible dust, including:
- National Fire Protection Association (NFPA)
- OSHA
- U.S. Food and Drug Administration (FDA)
NFPA Codes
NFPA sets standards regarding combustible dust. In fact, there are at least ten NFPA standards related to combustible dust (NFPA 61, 68, 69, 77, 484, 499, 652, 655, 664, 654). While these standards and codes are not law, per se, they are enforced by OSHA and referenced extensively. Most insurance agencies and local fire codes state that NFPA standards shall be followed as code.
NFPA’s most recent Standard on the Fundamentals of Combustible Dust (NFPA 652) covers the fundamental requirements for managing combustible dust fires and explosions and is an excellent starting point. NFPA 652 requires owners/operators to:
- Determine the dust’s combustibility and explosibility hazards based on laboratory testing or historical facility data.
- Conduct a Dust Hazard Analysis (DHA) to identify and evaluate potential dust fire and explosion hazards based on Kst (i.e., explosibility) values. Note: The DHA is a relatively new requirement—similar to OSHA’s Process Hazard Analysis as part of the Process Safety Management (PSM) program—used to assess risk and determine the required level of fire and explosion protection from combustible dust.
- Manage all the identified fire, flash fire, and explosion hazards identified in the DHA.
- Establish a written safety management system, including operating procedures and practices, training, incident investigation, and employee participation, to prevent and protect against the hazards.
NFPA 61 – Standard for the Prevention of Fires and Dust Explosions in Agricultural and Food Processing Facilities specifically covers facilities engaged in dry agricultural bulk materials or manufacturing and handling starch.
OSHA National Emphasis Program (NEP)
While OSHA has no formal standard for managing combustible dust, the agency published the Combustible Dust NEP in 2009, which outlines policies and procedures for inspecting workplaces that create or handle combustible dusts. The NEP heavily references the standards published by NFPA. It also references several other OSHA standards, including:
- 1910.22 Housekeeping
- 1910.307 Hazardous Locations
- 1910.1200 Hazard Communication
- 1910.269 Electric Power Generation, Transmission, and Distribution
- 1910.272 Grain Handling Facilities
- General Duty Clause, Section 5(a)(1) of the OSH Act
The General Duty Clause may be the most important of these, as it essentially gives OSHA the right to issue a citation any time employers fail to keep their employees safe from recognized hazards, including those hazards associated with combustible dust. Companies must control dust emissions to protect workers from exposure. If OSHA determines that even a very low Kst (i.e., low explosibility) dust is present in a facility with no explosion protection in place, the agency will issue citations and fines for lack of compliance.
Incidentally, OSHA published the Occupational Exposure to Flavoring Substances – Safety & Health Information Bulletin (SHIB) in 2010, cautioning that volatile organic compounds (VOCs) and respirable dust may be produced when handling many powdered flavoring formulations or spices. Inhalation of these substances may result in exposure directly to the small airways of the lungs.
FDA: Food Safety Modernization Act (FSMA)
In addition to meeting NFPA standards and OSHA guidelines, food companies must meet the requirements of FDA’s Food Safety Modernization Act (FSMA). FSMA requires food processing facilities to implement measures to ensure contamination hazards will be minimized or prevented. This includes developing a Hazard Analysis and Critical Control Points (HACCP) Plan with preventive controls for processes, food allergens, foreign objects, sanitation, and supply chain, as well as complying with Good Manufacturing Practices (GMPs).
Best Practices
Combustible dust itself is not avoidable, but the related consequences are. When it comes down to it, poor housekeeping is the biggest root cause of combustible dust issues. Many risks and hazards can be avoided by effectively cleaning the facility and equipment to remove contaminants before they become widely dispersed. Diligent housekeeping, combined with installing a dust collection system that is properly designed for the operation, can significantly reduce airborne dust and help mitigate a primary or more deadly secondary explosion.
If you work in the food industry, combustible dust is a concern. Make sure you understand the applicability of all the standards and codes, particularly the requirements under the various NFPA standards. The following may be required to keep your facility in compliance and your employees safe:
- Laboratory screening to determine if your powders are combustible or explosible.
- DHA to identify and evaluate potential dust fire, flash fire, and explosion hazards.
- Full analytical testing to determine explosion strength (Kst), minimum ignition energy, maximum safe storage temperature, and more.
- A written management system that documents operating procedures and practices for the ongoing management of dust fire, flash fire, and explosion hazards.
- Initial and ongoing training for operating, engineering, and management staff to build competency and understanding.
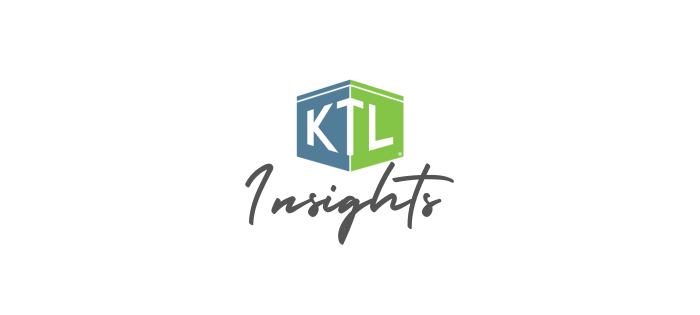
EHS: Top Trends to Watch in 2022
As we’ve seen businesses manage their way through the pandemic over the past two years and a new Administration take hold in office, a number of environmental, health, and safety (EHS) trends are rising to the surface. Some of these may sound familiar, as certain challenges and opportunities in EHS remain ongoing. Some are just gaining traction as we move into the new year.
Here are the top EHS trends KTL’s EHS professionals are keeping watch on in 2022—and some advice on what you can do to prepare…
OSHA Enforcement: Happy 50th Birthday OSHA!
The Build Back Better Act (BBBA) introduced the first amendment to the Occupational Safety and Health (OSH) Act in nearly 20 years. This would include increased funding to make significant improvements in workplace safety protection for American workers, as well as significant increases in the Occupational Safety and Health Administration’s (OSHA) maximum penalties. While the future of the BBBA is uncertain, it provides a good picture of where OSHA is headed by enacting high enough penalties to significantly impact businesses that violate the law and injure or kill workers. While OSHA doesn’t have the resources to audit or fine everyone, the agency will likely make an example of a few major violators to deter others from non-compliance.
To prepare: Make sure you have the processes, programs, and systems in place—and documented—to ensure you are always protecting employees’ safety and health and meeting OSH Act requirements.
EPA Inspections and Enforcement: Focus on Ammonia Refrigeration
With the new Administration, 2021 brought a significant uptick in Environmental Protection Agency (EPA) multi-media inspections, enforcement actions, and large penalties for violations, particularly related to anhydrous ammonia storage, risk management, and chemical accident prevention planning. Many of these violations have been uncovered as part of a National Compliance Initiative (NCI), which is working to enforce the regulatory aspects of the Clean Air Act’s (CAA) Chemical Accident Prevention Program, including Risk Management Plan (RMP) regulations (40 CFR Part 68), General Duty Clause (GDC) (CAA Section 112(r)), Emergency Planning and Community Right-to-Know Act (EPCRA) (CAA Section 312), Process Safety Management (PSM) regulations (29 CFR 1910.119).
To prepare: If your facility uses anhydrous ammonia and you have not conducted a hazard analysis, you are at significant risk of incurring enforcement actions of fines. It is important you invest the time and resources required to:
- Understand the hazards posed by chemicals at the facility.
- Assess the impacts of a potential release.
- Design and maintain a safe facility to prevent accidental releases.
- Coordinate with local emergency responders.
- Minimize the consequences of accidental releases that do occur.
PFAS/PFOA Contamination
Because of per- and polyfluoroalkyl substances’ (PFAS) persistence in the environment and widespread use in firefighting foams and products that resist grease, water, and oil, PFAS contamination is an extremely complicated issue—and concern is mounting over its impacts and how to regulate these chemicals going forward. On October 18, 2021, EPA Administrator Michael Regan announced EPA’s comprehensive Strategic Roadmap to tackle PFAS contamination through increasing investments in research, leveraging authorities to act now to restrict PFAS chemicals from being released, and accelerating cleanup of PFAS contamination. More and more facilities are going to be directly impacted by mitigation efforts and future regulatory action.
To prepare: Proper usage strategies, a comprehensive environmental management system (EMS), and a forward-thinking Emergency Response Plan will remain vital tools for companies potentially dealing with PFAS to effectively manage the associated risks.
Resource Constraints and Compliance Efficiency Tools
There are a few trends we see time and again, which generally can be tied back to many EHS “departments” (which often consist of just one person) lacking the resources—financial and personnel—to manage the sheer number of EHS requirements they are required to comply with. Frequently, companies may not understand or have the resources to manage everything that needs to be in place to satisfy compliance requirements. This is an area where EHS compliance efficiency and tracking tools are becoming essential to allow companies to do more with fewer resources.
To prepare: A compliance management system (CMS) brings information technology (IT) and management systems together to coordinate, organize, control, analyze, and visualize information in such a way that helps organizations remain in compliance and operate efficiently. A CMS can help provide operational flexibility, generate business improvement, and prepare organizations to address these and other EHS compliance challenges that will continue to surface.
Hazardous Waste Incineration Backlog
The changing hazardous waste market continues to create a fair amount of uncertainty regarding whether hazardous waste management capacity can actually meet demand. Many Large Quantity Generators (LQGs) and Small Quantity Generators (SQGs) are still experiencing a hazardous waste incineration slowdown, and most of the permitted transport, storage, and disposal facilities (TSDFs) are backlogged. EPA predicts that this backlog may not fully resolve until the end of the first quarter of 2022. EPA has offered multiple existing regulatory options for various regulated entities that generate and manage hazardous waste as temporary solutions to address the backlog.
To prepare: If you are in the situation where you are coming up against your time limits, contact your EPA Regional Administrator and ask for guidance on how to manage the situation. Keep very careful and accurate records of all hazardous waste information to demonstrate appropriate management.
Environmental Justice and Citizen Science
On January 27, 2021, President Biden issued Executive Order (EO) 14008 – Tackling the Climate Crisis at Home and Abroad, amending EO 12898, which directed federal agencies to develop environmental justice (EJ) strategies to help federal agencies address disproportionately high and adverse human health or environmental effects of their programs on minority and low-income populations. EO 14008 further directs Federal agency actions to support making EJ part of its mission by identifying and addressing the effects of all programs, policies, and activities on minority and low-income populations. As part of EPA’s EJ efforts, the Agency is charting a new pathway for the use of citizen science. Citizen science engages the public in identifying research questions, collecting and analyzing data, interpreting results, and developing technologies and applications to resolve environmental problems. Citizen science provides a resource in times of restricted budgets and to address dispersed or hyperlocal environmental issues.
To prepare: Equipment loan programs are available for anyone who would like to participate. KTL is aware of clients receiving money from the state to make equipment updates. In addition there are a number of EJ grants, funding, and other technical assistance available.
Sustainability
As developing nations continue to industrialize and increase their material consumption, resource demands and pressures on our supply chains will only increase. The Biden Administration has committed to a net zero economy by 2050, and the number of net zero commitments from local governments and businesses continues to grow and push further down the supply chain. There are more incentives for businesses to find clean/renewable energy solutions and to manage waste more sustainably. As one example, Sustainable Material Management (SMM) considers the entire of a product and/or process to help create a circular economy.
To prepare: Consider the following sustainability activities as part of your company’s business strategy:
- Conduct a lifecycle analysis (LCA) to identify and quantify the inputs and outputs in a process and use data to assess the potential environmental impacts across the lifecycle.
- Check with your local utility to have an energy audit completed of your facilities.
- Get input from employees on what initiatives are important to them by enacting a sustainability committee or adding sustainability to your EHS agenda.
Set Your Goals for 2022
With these trends toward more regulations, more enforcement, and more focus on sustainability, EHS management needs to play a more integral role in company strategy. Companies must take the time to be informed, be prepared, and be proactive. Establish company-wide EHS priorities and goals and commit the appropriate resources to ensure the required programs and systems are in place for 2022 and beyond.
If you would like help evaluating your current EHS risk level and assessing your priorities for 2022, please contact KTL.
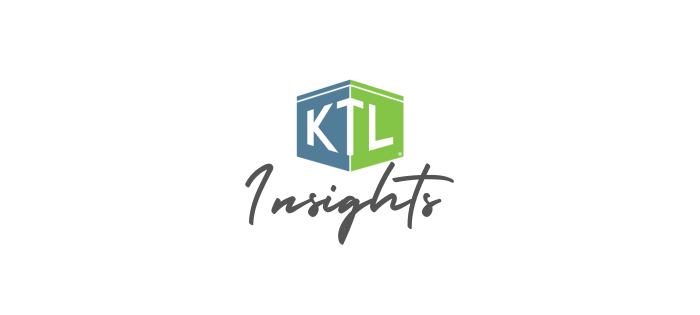
DOT General Awareness Training: June 16 & 22, 2021
Department of Transportation (DOT) code (49CFR172.702) requires that any employee involved in the transportation (shipping or receiving) of hazardous materials must be trained and tested in general awareness, safety, site-specific job functions, and transportation security.
8-hour DOT General Awareness Training (ONLINE)
June 16 (part A) & June 22 (part B), 2021
8:30 am – 12:30 pm CT
REGISTER NOW!
KTL’s 8-hour DOT General Awareness Training (held as two 4-hour sessions online on June 16 and June 22) is applicable for all companies that ship hazardous materials, ship hazardous waste, or prepare shipments of hazardous materials/waste for transport. It teaches all topics required for DOT general awareness training and general security training and will meet the requirements for triennial training certification.
Topics covered include:
- Code training requirements
- Shipping papers
- Hazardous materials table
- Incident reporting
- Hazard classes
- Common violations and confusing specifics
- Marking, labeling, and placarding
Cost: $198/participant. This online DOT training is held as two 4-hour sessions: June 16 (Part A) and June 22 (Part B) from 9 am – 1 pm. To receive CERTIFICATION, participants MUST complete Part A and Part B and pass both post-tests with 80%.
Training Details
- Training sessions will be held via Zoom. Link will be provided prior to class.
- Training is scheduled to begin at 8:30 am and end at 12:30 pm CT (or until material is complete).
- Participants will receive a training manual, pre-/post-competency test, exercises, and a certificate of completion, provided they receive an 80% or above on the test.
- Registration closes 72 hours prior to the scheduled training. KTL has the authority to cancel training with 72-hours notice if class size is not large enough.
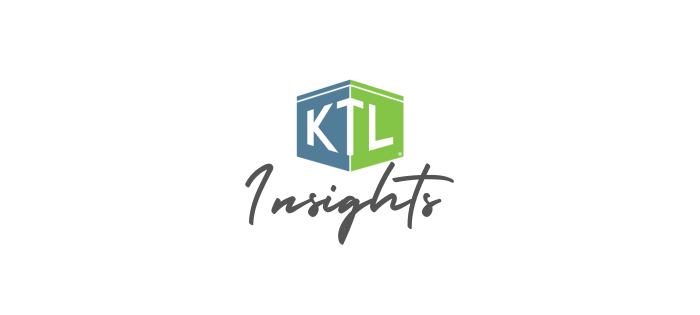
EHS Compliance: Top Issues
Companies committed to environmental, health, and safety (EHS) compliance face a complicated array of federal, state, and local regulations that may vary by industry sector, facility size, setting, and location. Technical EHS compliance has undergone significant changes over the last several of years—and more is likely to come in the foreseeable future. The evolving EHS landscape presents some significant challenges that companies must address to remain in compliance.
Pandemic
The COVID-19 pandemic has certainly impacted EHS, as it has other operations. There are probably few organizations that have not implemented operational changes on some level to respond to the pandemic—whether that has involved more remote working situations for staff, increased or decreased production, or updated travel and health and safety guidelines.
Changes such as these have had a cascading impact on the way organizations and EHS operations work. With more staff working from various and often remote locations, Cloud-based access EHS and facility documents, records, and shared applications has become essential. Employees need access to everything regardless of location. Along the same line, virtual monitoring methods have also become a necessity. With new guidelines for travel and who may be allowed in a facility, in-person monitoring, assessing, and auditing to meet EHS compliance requirements may not be possible for some facilities.
After over a year of adjusting to a new way of operating through the pandemic, resuming “normal” operations can present additional challenges. Workplace culture has undoubtedly changed. Defining what the culture is as individuals may (or may not) return to the work environmental will requirement management of change and, likely, training. It is important for organizations to address workplace changes and expectations and to evaluate new ways of doing business.
Staffing
EHS department understaffing has long been reported as an issue. In a 2016 study done by Triumvirate, 72% of companies reported EHS understaffing. Many organizations do not have dedicated EHS resources, and many EHS departments often consist of one individual who fulfills multiple roles. Internal resource growth as operations resume is questionable, as EHS expertise can be expensive. This presents an even bigger issue with many experienced workers—often those with the facility EHS background—electing not to return to the workplace full time. This is an area where EHS compliance efficiency and tracking tools are becoming essential to allow companies to do more with fewer resources.
Regulatory Uncertainty
Not surprisingly, EHS regulations—climate change, air, waste, water—are undergoing seismic shifts with the new Administration taking office. Some of these notable changes include the following:
- Environmental Protection Agency’s (EPA’s) new Waters of the U.S. (WOTUS) Rule
- Major Lautenberg Law Amendments to the Toxic Substances Control Act (TSCA)
- Chemical Safety Board’s (CSB’s) new Chemical Release Reporting Rule
- Latest Clean Air Act (CAA) requirements for facilities
On top of this, the differences between state and federal regulations are growing in many states. Organizations need to understand what requirements are applicable and what must be done to maintain compliance at all levels.
Enforcement
From 2017-2020, the U.S. experienced the lowest number of Occupational Safety and Health Administration (OSHA) inspections in over 10 years—including fewer complex investigations. In this same period, the Agency also has had the fewest OSHA inspectors conducting inspections in 40 years.
Not surprisingly, COVID has stalled many enforcement activities and court cases. However, despite COVID, EPA issued approximately $3 million in fines in Q3 of 2020:
- > $1.5 million Resource Conservation and Recovery Act (RCRA)
- > $1 million in Clean Air Act (CAA)
- > $0.5 million in Clean Water Act (CWA)
With the new Administration and resumed business activities, the frequency of comprehensive multimedia environmental inspections appears to be increasing. EHS regulatory enforcement is regaining momentum and likely will continue over the next few years.
Facing the Challenges
Achieving and maintaining EHS compliance requires great management and expertise to ensure all aspects of a company’s technical compliance have been identified and are being actively managed. A management system can provide the organizing framework to enable organizations to achieve and sustain their operational and business objectives through a process of continuous improvement. Information technology (IT) can further help to carry out daily tasks, connect staff, manage operations—and play a vital role in managing compliance requirements.
A compliance information management system brings IT and management systems together to coordinate, organize, control, analyze, and visualize information in such a way that helps organizations remain in compliance and operate efficiently. A system like this will help provide operational flexibility, generate business improvement, and prepare organizations to address these and other EHS compliance challenges that will continue to surface.
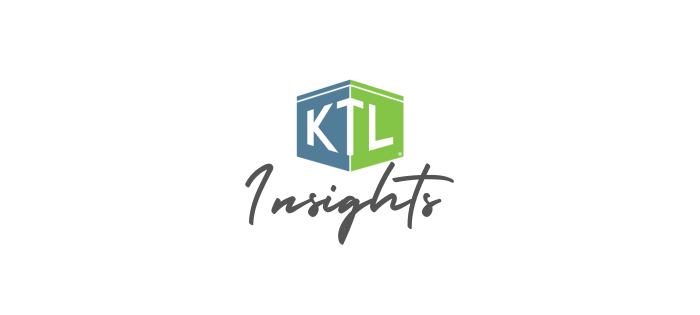
Webinar: Challenges of EHS Compliance in the U.S.
Current Challenges of Technical Compliance in the U.S.:
Focus on Occupational Health & Safety and Environment
May 17, 2021 | 4 pm – 5 pm CT
Technical compliance regarding EHS has seen tremendous changes over the last couple of years and is likely to change even more in the foreseeable future. EHS regulatory enforcement will undoubtedly regain momentum in the next few years. Achieving and maintaining EHS compliance requires great management and expertise to ensure all aspects of a company’s technical compliance have been identified and are being actively managed.
KTL’s Sarah Burton will be joining Martin Mantz Compliance Solutions, our German alliance partner, to discuss the challenges of technical EHS compliance and to provide an up-to-date understanding of technical compliance in the U.S. today.
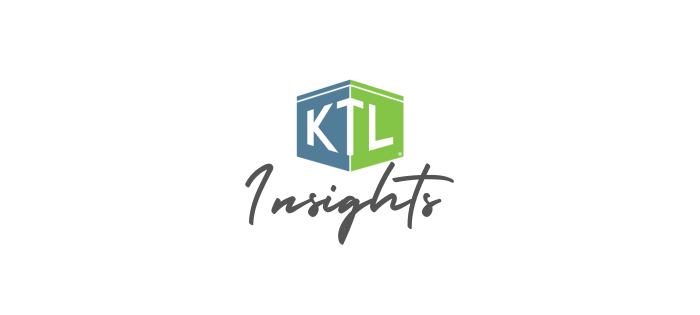
Demonstrating Compliance in a Socially Distanced World
Don’t miss this free American Bar Association event on April 22, 2021 — Demonstrating Compliance in a Socially Distanced World: Virtual Auditing.
In the time of COVID-19, virtual auditing has become increasingly necessary and valuable to organizations as they seek to achieve environmental compliance while facing worldwide travel restrictions and remote work policies that have disrupted routine in-person audits. With this shift, comes the need for both regulated entities and regulators to develop new approaches and procedures to ensure the effectiveness of audits conducted remotely. Practitioners, including auditors and legal counsel, must consider new dynamics related to security, data protection, and audit integrity-on top of the usual audit considerations. This session will highlight some of these new challenges and provide real-world solutions to aid attendees form new practice skills to apply in the (virtual) field.
Panelists–including KTL’s Sarah Burton–will explore the new world of remote auditing, focusing on real-world solutions to the challenges that virtual auditing presents.
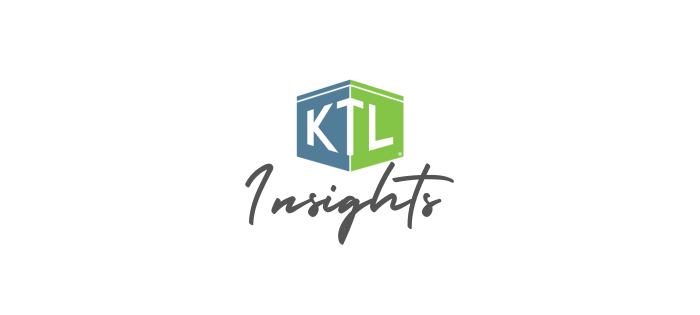
Comments: No Comments
Regulatory Alert: Proposed Update to OSHA Hazard Communication Standard
On February 16, 2021, the Occupational Safety and Health Administration (OSHA) issued a proposed rule to update the agency’s Hazard Communication Standard (HCS) to align with updates to the United Nations (UN) Globally Harmonized System of Classification and Labeling Chemicals (GHS), as well as those of Canada and other U.S. agencies.
According to OSHA, the agency “expects the proposed updates to the HCS will increase worker protections and reduce the incidence of chemical-related occupational illnesses and injuries by further improving the information on labels and safety data sheets (SDS) for hazardous chemicals.”
HCS and GHS
The HCS was initially adopted by OSHA in 1983 to create a standardized approach for communicating about workplace hazards associated with hazardous chemical exposures. The standard requires chemical manufacturers and importers to classify the hazards of chemicals produced and/or imported to the U.S. and to communicate to employees about these chemicals through a hazard communication program, including labels and other forms of warning, SDS, and training.
Like HCS, the GHS is an international standard that was created as a “universally harmonized approach” to classifying chemicals and communicating hazard information. Warning pictograms that can be understood in any language are a key component of the GHS, in addition to universal standards for hazard testing criteria and SDS. The UN updates the GHS every two years, with the most recent updates in 2019 with Revision 8.
OSHA’s proposed HCS updates are the agency’s first since 2012 and are intended to address issues that have emerged since 2012, align with GHS Revision 7 and some provisions from GHS Revision 8, and enhance cooperation with international trading partners. Correspondingly, as part of OSHA’s proposed rule, the agency is evaluating whether it should establish a schedule for updating the HCS to coincide with GHS updates or maintain the status quo of updating when there are substantial changes to GHS requirements.
Major Proposed Changes
The following proposed modifications to the HCS are intended to improve hazard communication so employees are more aware of the hazards associated with potential chemical exposure, while creating additional clarity and flexibility in requirements:
- Flexibility for bulk shipments of hazardous chemicals, including allowing labels to be included on immediate containers or with shipping papers, bills of landing (BOLs), or other electronic means that are immediately available to workers in printed form on the receiving end of the shipment.
- Options for labeling small containers when it is not feasible to use traditional pull-out labels, fold-back labels, or tags containing full information. This includes using just the product identifier, pictogram, signal word, chemical manufacturer’s name/phone number, and statement that full information is provided on the immediate outer package for containers less than or equal to 100 ml capacity. For those with a capacity of 3 ml or less, only the product identifier needs to be displayed.
- New requirements for updating labels on individual containers that have been released for shipment but are waiting future distribution. These shipments would not need to be relabeled; however, the chemical manufacturer/importer would need to provide the updated label for each individual container with each shipment.
- Updates to precautionary statements in every hazard class and category. OSHA is also proposing certain statements related to medical response be prioritized.
- Withholding of a chemical’s concentration range as a trade secret. In addition, OSHA is proposing to allow the use of prescriptive concentration ranges rather than actual concentration/concentration ranges (consistent with those required by Canada) when these are deemed trade secrets.
- New required information on SDS, including U.S. address/phone in Section 1, hazards associated with change in chemical’s physical form, identification of hazards that result from a chemical reaction, more information on physical and chemical properties (e.g., particle size), and more information on interactive effects.
Next Steps
OSHA is currently seeking public comment on the HCS proposed updates through April 19, 2021.
While many of OSHA’s proposed changes will provide additional flexibility to chemical manufacturers and importers, as well as alignment with GHS and international trading partners, the regulatory burden is not insignificant to those impacted. The fundamental structure of the HCS is not changing; however, the revisions will require companies to update SDS, labels, and training. All of this will take appropriate and resources to meet deadlines once any proposed updates are finalized.