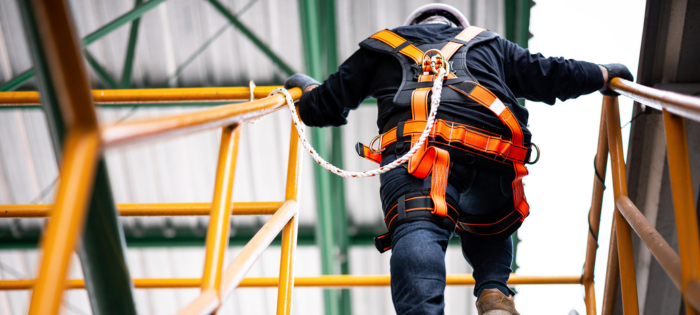
Safety
Comments: No Comments
Safe + Sound Week
In the post-COVID world, working remotely and alone has become much more common. In many industries, particular attention needs to be paid to these lone workers to ensure appropriate practices and procedures are in place to keep them safe.
What Is a Lone Worker?
Lone workers are people who perform their jobs alone—without someone else present and without any supervision. Lone workers cannot be heard or seen by another individual while working. They may work in more remote locations with limited emergency response or perform jobs during nonstandard work hours. Lone workers may also work in the same building or area as others but out of viewing or hearing distance.
Workplace Safety Hazards
A workplace safety hazard is anything that could potentially cause harm or damage to people, property, or equipment. The most common safety hazard for all workers, including lone workers, is slips, trips and falls. Another common safety hazard that lone workers face is from machinery and equipment, which can injure or trap the worker.
To avoid workplace safety hazards, there are certain conditions where lone work is not recommended and/or prohibited, including the following conditions:
- From height
- With electricity or in confined spaces
- During severe weather conditions
- Around avalanche risks
- Near chemical exposure that could incapacitate a worker
- When respirators or air monitoring is required
- Using hazardous equipment (e.g., chainsaws, firearms)
- Where the potential for violence is present
Planning and Preparation
The Occupational Safety and Health Administration (OSHA) does not have a standard for employees working alone; however, there are several standards that apply to specific lone-work situations (e.g., emergency response, interior structural firefighting). OSHA further recommends that employers develop emergency procedures and provide “a wireless electronic notification device and/or cellphone to those employees.”
As best practice, any company with lone workers should develop and implement a lone worker safety program with specific practices and procedures to minimize the risk of injury. This includes the following:
- Identify, assess, and mitigate work hazards. It is important to identify safety hazards in any work environment but particularly for lone workers who must navigate hazardous situations alone. Each hazard’s level of risk must be assessed. Once this assessment is complete, strategies can then be implemented to remove existing dangers to the extent possible, prioritizing the highest risk hazards. Hazard mitigation should consider physical modifications, safety education and training, and communication to help ensure workplace injuries and incidents occur less frequently.
- Create a lone worker policy. This policy should establish the organization’s rules and practices for working alone. Generally, a lone worker safety policy should include:
- Contact information and location of all lone workers
- General safety guidance
- Roles and responsibilities
- Safety procedures and processes, including predetermined safety check-ins and stop-work guidance
- Methods of communication and available backups (e.g., cell phone, GPS devices, and mobile apps)
- Emergency procedures and contacts
- Lone worker training and continuous education
- Monitor lone workers. Lone workers must be monitored, whether through regular manual check-ins or automated monitoring systems. Both allow the employer to confirm the worker’s safety and well-being. If a worker misses a check-in, an automated system can immediately request help and employ tools such as GPS location tracking to provide necessary assistance.
Don’t forget about your lone workers. They play an important role and special provisions need to be taken to ensure they are monitored and protected.