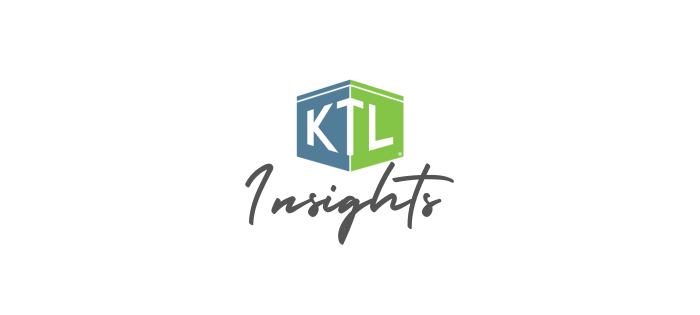
Comments: No Comments
EPA Proposes to Delay RMP Rule Effective Date to 2019
EPA Proposes to Delay RMP Rule Effective Date to 2019
On Friday, March 31, 2017, U.S. Environmental Protection Agency (EPA) Administrator Scott Pruitt announced a proposed rule to further delay the effective date of the Obama Administration’s Risk Management Program (RMP) final rule until February 19, 2019. This will give the agency time to reconsider the final RMP rule published on January 13, 2017.
Industry organizations have raised serious concerns about the final rule. The proposal to further delay the effective date of the amendments will allow the Agency time to evaluate these objections and consider other issues that may benefit from the additional public input.
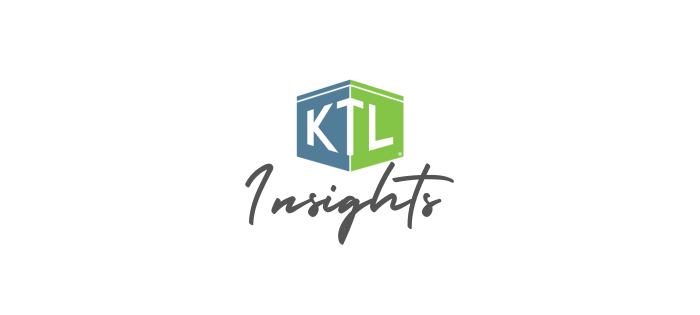
Comments: No Comments
OSHA Releases Three New PSM Publications
OSHA has released three new guidance documents to help employers comply with the agency’s Process Safety Management (PSM) standard. PSM is critically important to facilities that store highly hazardous chemicals. Implementing the required safety programs helps prevent fires, explosions, large chemical spills, toxic gas releases, runaway chemical reactions, and other major incidents. The new documents focus on PSM compliance for Small Businesses, Storage Facilities and Explosives and Pyrotechnics Manufacturing.
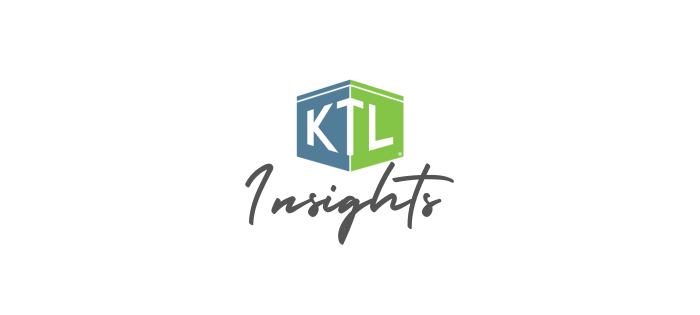
Comments: No Comments
EPA Puts Risk Management Program Rule on Hold
EPA Puts Risk Management Program Rule on Hold
This January, the much anticipated final RMP amendments were published in the Federal Register. According to the EPA, these amendments are intended to:
- Prevent catastrophic accidents by improving accident prevention program requirements
- Enhance emergency preparedness to ensure coordination between facilities and local communities
- Improve information access to help the public understand the risks at RMP facilities
- Improve third-party audits at RMP facilities
As Kestrel indicated in a recent article when the final RMP amendments were published, RMP faces an uncertain future under the Trump Administration. It is not clear at this point whether the final RMP rule will actually be implemented as published—or at all.
We are seeing the first wave of that uncertainty demonstrated. EPA received a petition dated February 28, 2017, from the RMP Coalition requesting a reconsideration and request for a stay for the RMP rule amendments. After a proceeding for reconsideration on March 13, 2017, EPA’s Administrator signed a final rule that provides a three-month (90-day) administrative stay of the effective date of the RMP rule amendments, delaying the effective date of the final rule to June 19, 2017. This stay is intended to allow the EPA to revisit these important issues and consider alternative approaches.
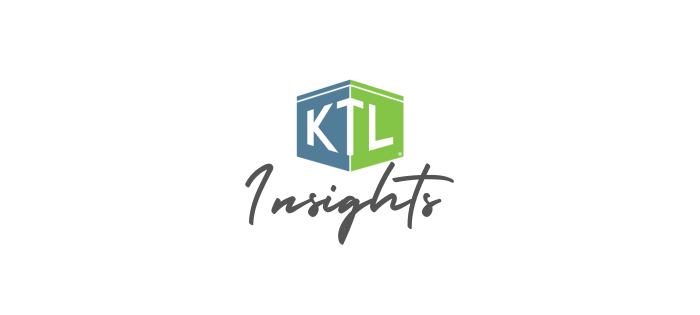
Comments: No Comments
Improving Process Safety Leadership and Culture
Over the past 30 years, there have been numerous events both nationally and internationally that have led organizations to bring a more concerted focus to process safety. Such a focus has many such organizations building process safety elements into their management systems. The goal is to not only comply with regulations, such as OSHA 1910.119, but to also ensure sustainable programs that prevent process safety incidents from ever happening.
A large part of this effort involves integrating process safety leadership into existing programs. Improving an organization’s process safety leadership and culture can have significant and lasting impacts on a company’s process safety performance. Three steps that organizations can undertake to advance this effort include the following:
- Amending metrics to include more leading indicators that are designed to prevent process safety incidents
- Cultivating communications geared toward process safety
- Ensuring incentive schemes include measures related to process safety
Traditional Management Systems
Traditional management systems include personal safety, environmental management, and industrial hygiene as the core elements. Management systems, metrics, and communications have historically been focused on personal safety and environmental management. These areas have clear industry compliance drivers and easy-to-understand metrics for organizational leaders. The prevention of personal injury or actions to protect the environment are relatable concepts for most.
The addition of process safety to the management system structure has been a smooth transition for many organizations, as the majority of the elements that cover process safety are already part of a typical management system. However, process safety—and the incidents that can occur if not managed well—can be complex in nature to explain. The challenging part of integrating process safety into an organization becomes getting leaders both comfortable and equipped to address it.
Leading Metrics
Due to the generally low frequency of process safety incidents, the development and measurement of process safety indicators is often not a priority for organizations. Many companies rely heavily on lagging personal safety and environmental metrics (Days Away from Work Rate, Total Recordable Incident Rate, Spill Rate). Injuries are easy for leaders to understand and explain. Leaders demonstrate empathy towards their staff and contractors, again making it easier for them to relate to personal safety. Minor spills are also easily understood and easier to discuss.
While these lagging metrics are still important and can be used and communicated, organizations need to include different metrics to bring more focus on leading indicators that are designed to prevent process safety incidents. Some examples of leading metrics that can be developed, implemented, and tracked include the following:
- Identifying systems/equipment that are critical to prevent or mitigate a process safety event, and tracking their effectiveness and operability
- Tracking the completion of Management of Change (MOC)
- Tracking the effective closeout of Process Hazard Analysis (PHA) and PSM audit actions
- Assessing organizational capability around process safety and tracking identified gap closure plans
- Tracking the number of Pressure Relief Valve (PRV) activations
- Tracking anomalies from complete permit-to-work reviews
Communication
Once an organization has developed a set of leading process metrics applicable to the business, the metrics should be made visible to all staff and included in communications on business performance. Leaders also need to focus more of their strategic communications and site visits on process safety. This can include talking about leading process safety metrics and undertaking the following activities when at a facility:
- Ask members of the facility staff about the major identified hazards from the PHA
- Determine if staff are involved in reviewing and updating operating procedures
- Ask staff about the last emergency drill and actions taken
- Ask operations staff about the number of alarms they deal with on a typical shift to determine if alarm management/rationalization is required or if low criticality alarms are not burdening staff
- Hold discussion groups focused on process safety during leadership onsite visits
Incentive Schemes
Another outcome of tracking lagging metrics involves translating them into part of the organization’s incentive bonus criteria for leaders. Organizations should work to transition leadership bonus/incentive schemes away from just traditional personal safety and environmental lagging metrics, namely injury and spill rates. Again, it would not be necessary to immediately drop existing lagging metrics. Start with adding the new metrics and gradually change the percentage weightings so leading process safety indicators become the dominant factor. This will serve to reinforce the importance of process safety and incident prevention in overall business performance.
To truly have an organization that demonstrates process safety leadership and has a strong process safety culture, there need to be some changes and effective actions taken. The steps outlined in this article—amending metrics, cultivating communications toward process safety, and integrating process safety into incentive schemes—can help organizations take a few of the initial necessary steps to build process safety culture and leadership and, ultimately, prevent process safety incidents from occurring.
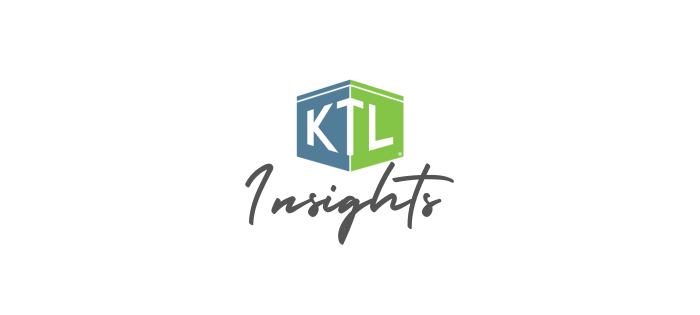
Comments: No Comments
GFSI in 2017: The Year of FSMA Compliance
This year is being described as “the year of FSMA compliance,” as many compliance dates for the various FSMA rules fall in 2017. As one might expect, the FSMA law and rules include many aspects of the established Global Food Safety Initiative (GFSI) standard; however, there are also differences in how they are applied to create better food safety enforcement.
At the most basic level, GFSI is an industry conformance standard for certification, while FSMA is a compliance regulation that must be met. However, both work together to ensure companies are effectively managing food safety.
GFSI Conformance
The GFSI is facilitated by the industry network of The Consumer Goods Forum. It provides a very solid foundation and supporting objective of “safe food for consumers everywhere”.
GFSI was originally established based on a growing pattern of food safety outbreaks throughout the international marketplace. This led to the proactive development of GFSI standards as an alternative to the more limited and less effective customer audits in place at the time. An important part of this outcome was that CEOs in the food industry—not a regulatory body—determined the need to address food safety through the GFSI food safety standard.
With its beginning as a benchmarking organization, GFSI has since evolved throughout the food supply chain as a strong means for achieving global food safety. It is now established, growing, and improving across the primary supply chains within the global food market.
As such, much work to address food safety has been accomplished by GFSI over the past sixteen years. In fact, the industry-driven aspect of GFSI along the food supply chain has led many companies to achieve levels of food safety comparable to those required to achieve FSMA compliance. Based on its collaboration of food safety experts, GFSI provides for a significant evolution of food safety programs and supports those requiring FSMA compliance.
FSMA Compliance
During a similar timeframe, the United States identified food safety as a major concern for the public. In the 1990s, a growing number of food outbreaks from biological contamination continued to spread, prompting the addition of controls within both the USDA and FDA. These brought the mandated requirement for Hazards and Critical Control Points (HACCP) and supporting Good Manufacturing Practices (GMPs) to specific industry sectors. However, these efforts were measured to have limited effect, as the outbreaks continued.
By the early 2000s, the public concern for food safety continued, and the FDA was determined to make changes. Along with Congress, the FDA commissioned research into the underlying issues that were resulting in the growing number and severity of food outbreaks. This research was being conducted and analyzed just as GFSI was determining its final group of benchmarked standards. At the same time, GFSI was positioned to be advanced into the U.S. market by food industry leaders, including Cargill, McDonalds, Walmart, Kroger, Coca Cola and Wegmans.
The outcomes from the FDA studies determined that the GMPs (in existence for the past 40 years) were not effectively implemented across the U.S. food industry. Further, the studies indicated that the ability to prevent food safety issues through specific controls would provide a means for reducing the number of foodborne illness.
This effort led to the development of FSMA, which passed in January 2011. Additional FSMA rules have since been published, starting in September 2016. The FSMA rules represent a rewrite of the existing FDA food safety regulations. However, with the FSMA law taking several years to roll out, the existing FDA laws remain in effect until they are replaced. These actions expand the FDA’s jurisdiction now and until full compliance of FSMA.
Bringing GFSI and FSMA Together
The presence of GFSI in the U.S., as well as the GFSI certification of many suppliers to U.S. food importers, provides for a synergy between the GFSI standard and the FSMA law being enforced throughout the U.S. and its foreign suppliers. GFSI’s global focus provides the structure to adapt and meet many of the FSMA requirements, with the ability to expand to all FSMA requirements.
As one would expect, the FSMA law and rules include several aspects of the GFSI standard; however, there are many differences in how each is applied to encourage better food safety enforcement. For instance, GFSI has the advantage of providing the time to develop programs, and thousands of companies are certified to the various programs under the standard. Conversely, FDA is implementing FSMA compliance over several years, with 2017 being a big year for compliance (based on the rules’ published dates, company size and industry segment).
In this new order of food safety in the U.S., those companies that have achieved GFSI certification should have an advantage over those who do not, provided they can align their GFSI programs with the FSMA law requirements. However, there is also a benefit to starting with FSMA and moving to a GFSI certification.
Existing GFSI certifications provide an established framework, with many of the program requirements similar to those required by FSMA. For example, personnel are required by both to establish HACCP and Food Safety Plans, as well prerequisite procedures (PRPs) and current-Good Manufacturing Practices (cGMPs). The challenges are ensuring the complete development of these food safety procedures to guarantee they meet both GFSI and FSMA requirements.
As another example, personnel requirements are similar but different under FSMA and GFSI, which calls for training, updating and qualifying resources. Ultimately, advanced HACCP training under GFSI provides the means for establishing a Qualified Individual under FSMA, but it requires expanding the training to include FSMA Preventive Controls and procedures. The resulting plan is the Food Safety Plan, which can be based on HACCP but with the proper additions to meet FSMA requirements.
Global Food Safety Conference
The upcoming Global Food Safety Conference (February 27 – March 3 in Houston, Texas) provides an opportunity for those seeking compliance to FSMA or certification to a scheme within the GFSI Standard to get a deeper understanding of food safety. With 2017 being the year of FSMA compliance, it is very appropriate that the Global Food Safety Conference be held in the U.S. this year. The conference will provide U.S. companies attending, as well as foreign suppliers of products to the U.S. market, an educational opportunity and forum to reach out to experts from industry, government, and academia to better understand these two key areas for food safety program development. Some of the topics to be addressed at the conference include the following:
- Food safety management commitment and corporate governance
- Required training of food safety roles, including management, staff and operations
- Specific requirements of the documented food safety program or written programs under FSMA
- FDA requirements of the past and existing requirements prior to FSMA and the relationship of these as comparable to GFSI
- Implications for FDA enforcement under FSMA of these previous requirements and program requirements that may need to be formalized under FSMA
- The proof of evidence with supporting records required by FSMA that may be addressed in part by existing or GFSI-level food safety programs
- How to adapt a FSMA-level food safety plan and preventive controls cGMPs from existing programs, including GFSI, or develop these to function with existing programs
- Levels and numbers of qualified individuals, qualified auditors and competent sanitation for oversight and management of FSMA food safety plans
- Management reanalysis and update of the written FSMA programs to ensure compliance and readiness for inspection by FDA FSMA investigators
- Process used to ensure compliance with FSMA Preventive Controls and the other FSMA rules being issued in 2017 and 2018, including Foreign Suppler Verification, Sanitary Transportation and Intentional Adulteration
Kestrel has been a long-time advocate of GFSI, performing site certification program development support for hundreds of companies. We have served as a GFSI Stakeholder, Technical Working Group participant, and panelist at previous GFSI Global Food Safety Conferences. We look forward to seeing you at the 2017 GFSI Global Food Safety Conference and to helping you navigate GFSI conformance and FSMA compliance requirements.
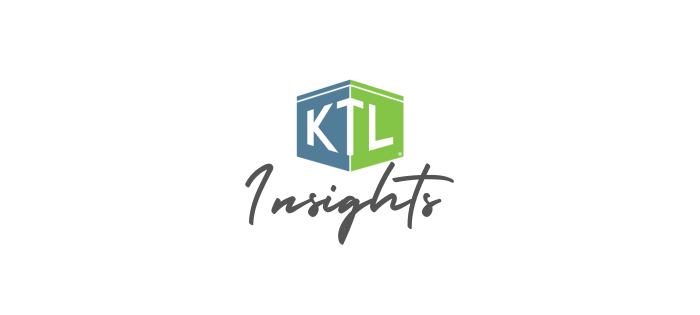
Comments: No Comments
Risk Management Plan (RMP) Final Amendments
Chemicals are an important part of many aspects of our lives; however, improper handling and management of chemicals can result in catastrophic releases that have severe and lasting impacts—loss of life, injury, property damage, community disruption. USEPA’s Risk Management Plan (RMP) data shows that in the last 10 years, there have been more than 1,517 reportable incidents of accidental chemical releases. Those incidents were responsible for 58 deaths, 17,099 injuries, the evacuation or shelter-in-place of almost 500,000 people, and over $2 billion in property damage.
Charting the Changes to RMP
The USEPA’s RMP Rule (Section 112(r) of the Clean Air Act Amendments) is aimed at reducing the frequency and severity of accidental chemical releases. Changes to the RMP Rule have been in progress since former President Obama issued Executive Order (EO) 1365, Improving Chemical Safety and Security, in August 2013. The focus of the EO is to reduce risks associated with hazardous chemicals to owners and operators, workers, and communities by enhancing the safety and security of chemical facilities. Modernizing policies and regulations—including the RMP Rule—falls under this umbrella.
A July 2014 Request for Information (RFI) sought initial comment on potential revisions to RMP under the EO. This was followed by a Small Business Advocacy Review (SBAR) Panel discussion in November 2015. On March 14, 2016, the USEPA published Proposed Rule: Accidental Release Prevention Requirements: Risk Management Programs Under the Clean Air Act, Section 112(r)(7), outlining proposed amendments to the RMP Rule.
Since the initial action to revise the RMP Rule commenced two and a half years ago, the USEPA has received over 60,000 public comments and has had extensive engagement with nearly 1,800 people.
Final Amendments
The much anticipated final RMP amendments were published in the Federal Register on January 13, 2017. According to the USEPA, these amendments are intended to:
- Prevent catastrophic accidents by improving accident prevention program requirements
- Enhance emergency preparedness to ensure coordination between facilities and local communities
- Improve information access to help the public understand the risks at RMP facilities
- Improve third-party audits at RMP facilities
The final changes in the RMP Rule are outlined in the table below.
Compliance
The effective date for the final RMP amendments is March 14, 2017. Compliance dates are set according to this date, as follows:
The Future of RMP
The final RMP amendments have the potential to significantly affect the 12,500 facilities in the U.S. that are subject to the RMP program. However, like many environmental rules, RMP faces an uncertain future under the Trump Administration. It is not clear at this point whether the final RMP Rule will actually be implemented as published—or at all.
Among the possible outcomes, environmental law firm Beveridge & Diamond PC cites the following possibilities:
- Congress may rescind the Rule using the Congressional Review Act.
- The USEPA might stay the Rule and then unilaterally seek to repeal it through amendment.
- The Rule might be challenged through a petition for reconsideration to the USEPA or a petition for review by the federal courts.
Kestrel will continue to track the RMP Rule and potential upcoming actions or compliance dates that may affect impacted facilities.
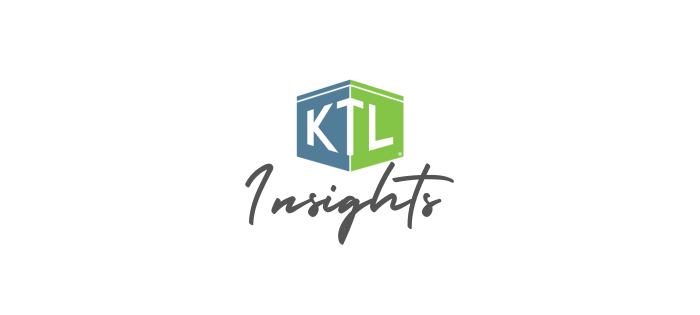
Kestrel Grows Senior Food Safety Resources
Kestrel is pleased to be growing our resources to the food industry with the addition of Senior Consultant Roberto Bellavia.
Roberto comes to Kestrel following a successful career with US Foods, where he provided leadership for quality and food safety programs; managed and developed HACCP, GMP, SSOP, and SOP programs; and planned and implemented GFSI certification for FSSC 22000 at 13 national locations.
At Kestrel, Roberto will be serving as project manager for food safety-related projects and supporting clients in developing and implementing GFSI schemes and supplier approval programs. He will focus on meat, dairy, RTE, bakery, and other related food industry segments.
Roberto holds a number of food qualifications that will enhance Kestrel’s ability to serve the food industry, including GFSI, HACCP, GMP, SSOP, SOP, FSPCA, Lead Auditor certifications. He has nearly 20 years of food quality experience and a Master’s Degree in Animal Production Science from the University of Camerino in Italy.
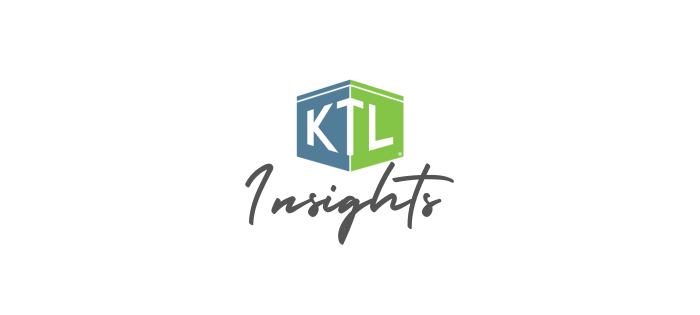
Comments: No Comments
FSMA Preventive Controls: Are You Prepared?
Compliance with the Food Safety Modernization Act (FSMA) has presented a new and difficult challenge for the industry, the public, and the FDA since it passed on January 4, 2011. When it comes to the Preventive Controls Rule, the prime question for companies, regardless of size, is whether they have aligned their preventive controls development with existing HACCP programs to meet current FSMA requirements.
Overview of Requirements
Under the Preventive Controls Rule, registered food facilities must evaluate and implement preventive control provisions to meet the requirements and the compliance deadline. The most urgent concerns for companies subject to the Preventive Controls Rule include developing a Preventive Controls Program, identifying a Preventive Controls Qualified Individual (PCQI), and implementing a Food Safety Plan.
The following areas are all included under the FSMA Preventive Controls Rule:
- Hazard Analysis. Companies must identify and evaluate known and reasonably foreseeable hazards.
- Preventive Controls. Preventive controls must be implemented to significantly minimize or prevent the occurrence of hazards.
- Monitoring. Preventive controls must be monitored for effectiveness.
- Corrective Actions. Procedures for addressing failures of preventive controls and prevention of affected food from entering commerce are required.
- Verification. Facilities are required to verify that preventive controls, monitoring, and corrective actions are adequate.
- Recordkeeping. Records must be kept for two years.
- Written Plan and Documentation. A written plan must document and describe procedures used to comply with requirements.
- Qualified Individual. A Qualified Individual who has been adequately trained must be present at the facility to manage the preventive controls for the site and the products processed and distributed at/from the site.
Failure to implement preventive controls (a/k/a Hazard Analysis and Risk-based Preventive Controls (HARPC)) for qualified sites may result in fines and possible jail sentences.
Key Questions
The following questions can help organizations assess their compliance with the Preventive Controls Rule and better determine their current state of planning for FSMA compliance:
-
- In determining the appropriate preventive controls under FSMA for your food operation, have you evaluated your compliance requirements and categories?
- Have you assessed hazards outside or not part of your existing HACCP flows for determining preventive controls?
- Are the preventive controls you have identified supported by science-based justification?
- Is the science-based information supported by means such as statistical methods, published reports, peer review, industry/second-party verification, or other documentation?
- Have you determined the program requirements for preventive controls for implementation in your Food Safety Management System (FSMS), as required by the FSMA Food Safety Plan requirement?
- Have the cGMP-based policy, procedure, work instruction, test/validation, forms, and records criteria been established for preventive controls at your food operation(s)?
- Have you determined the functional organizational responsibilities of preventive controls, your preventive control Food Safety Plan, and Qualified Individual?
- Does organizational responsibility include oversight by process owners of preventive controls and comprehensive FSMA management?
- Will completion of your program, as documented with cGMPs and a validated Food Safety Plan, meet FSMA and customer deadlines?
- Will internal auditing of program elements meet established timing and allow for preventive control and Plan verification and management review?
Companies must have their training, planning and development underway to comply or face possible violations, fines, and penalties under FDA enforcement. These questions will help identify the areas in need of attention to ensure that companies have aligned their preventive controls development with existing HACCP programs to meet requirements and any pending deadlines.
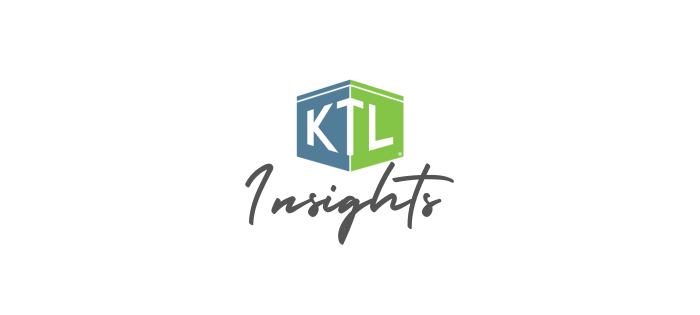
Comments: No Comments
Final Rule: Walking-Working Surfaces
OSHA has issued a final rule updating its general industry Walking-Working Surfaces standard to protect workers from slip, trip, and fall hazards. The rule also increases consistency in safety and health standards for people working in both general and construction industries.
The final rule’s most significant update is allowing employers to select the fall protection system that works best for them, choosing from a range of accepted options including personal fall protection systems.
OSHA estimates the final rule will prevent more than 5,800 injuries a year. The rule takes effect Jan. 17, 2017.
Read the full press release.
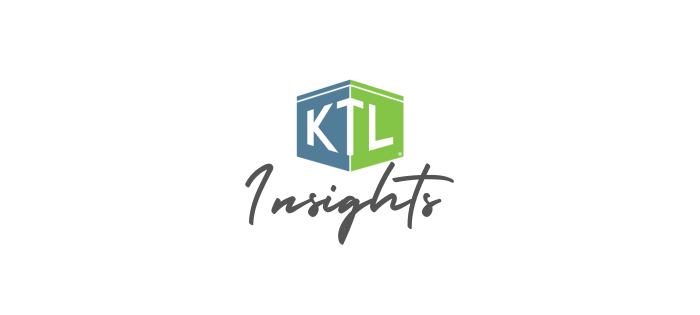
Comments: No Comments
FSMA Preventive Controls Guidance: Small Business
The U.S. Food and Drug Administration (FDA) has issued two Food Safety Modernization Act (FSMA) small entity compliance guidance documents to assist small and very small businesses with the implementation of the Preventive Controls for Human Food and Preventive Controls for Animal Food rules.
The guidance outlines who must comply with the rule, who is exempt from parts of the rules or subject to modified requirements, and outlines key information for qualified facilities (i.e., small businesses).
The guidance documents are two of dozens of guidance documents the FDA intends to release as it continues with the implementation of FSMA. The Agency released guidance for both the human and animal food rules in August 2016.