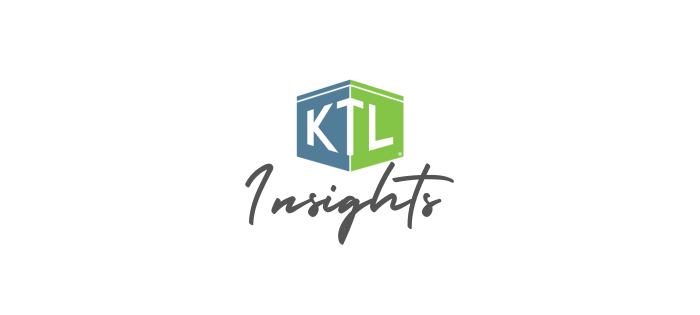
Audit Program Best Practices: Part 1
Audits provide an essential tool for improving and verifying compliance performance. Audits may be used to capture regulatory compliance status, management system conformance, adequacy of internal controls, potential risks, and best practices. An audit is typically part of a broader compliance assurance program and can cover some or all of the company’s legal obligations, policies, programs, and objectives.
Companies come in a variety of sizes with a range of different needs, so auditing standards remain fairly flexible. There are, however, a number of audit program elements and best practices that can help ensure a comprehensive audit program:
- Goals. Establishing goals enables recognition of broader issues and can lead to long-term preventive programs. This process allows the organization to get at the causes and focus on important systemic issues. It pushes and guides toward continuous improvement. Goal-setting further addresses the responsibilities and obligations of the Board of Directors for audit and oversight and elicits support from stakeholders.
- Scope. The scope of the audit should be limited initially (e.g., compliance and risk) to what is manageable and to what can be done very well, thereby producing performance improvement and a wider understanding and acceptance of objectives. As the program is developed and matures (e.g., Management Systems, company policy, operational integration), it can be expanded and, eventually, shift over time toward systems in place, prevention, efficiency, and best practices.
- Committed resources. Sufficient resources must be provided for staffing and training and then applied, as needed, to encourage a robust auditing program. Resources also should be applied to EHSMS design and continuous improvement. It is important to track the costs/benefits to compare the impacts and results of program improvements.
- Operational focus. All facilities need to be covered at the appropriate level, with emphasis based on potential EHS and business risks. The operational units/practices with the greatest risk should receive the greatest attention (e.g., the 80/20 Rule). Vendors/contractors and related operations that pose risks must be included as part of the program. For smaller, less complex and/or lower risk facilities, lower intensity focus can be justified. For example, relying more heavily on self-assessment and reporting of compliance and less on independent audits may provide better return on investment of assessment resources.
- Audit team. A significant portion of the audit program should be conducted by knowledgeable auditors (independent insiders, third parties, or a combination thereof) with clear independence from the operations being audited and from the direct chain of command. For organizational learning and to leverage compliance standards across facilities, it is good practice to vary at least one audit team member for each audit. Companies often enlist personnel from different facilities and with different expertise to audit other facilities. Periodic third-party audits further bring outside perspective and reduce tendencies toward “home-blindness”.
- Audit frequency. There are several levels of audit frequency, depending on the type of audit:
- Frequent: Operational (e.g., inspections, housekeeping, maintenance) – done as part of routine EHSMS day-to-day operational responsibilities
- Periodic: Compliance, systems, actions/projects – conducted annually/semi-annually
- As needed: For issue follow-up
- Infrequent: Comprehensive, independent – conducted every three to four years
- Differentiation methods. Differentiating identifies and distinguishes issues of greatest importance in terms of risk reduction and business performance improvement. The process for differentiating should be as clear and simple as possible; a system of priority rating and ranking is widely understood and agreed. The rating system can address severity levels, as well as probability levels, in addition to complexity/difficulty and length of time required for corrective actions.
- Legal protection. Attorney privilege for audit processes and reports is advisable where risk/liability are deemed significant, especially for third-party independent audits. To the extent possible, make the audit process and reports become management tools that guide continuous improvement. Organizations should follow due diligence elements of the USEPA audit policy.
- Procedures. Describe and document the audit process for consistent, efficient, effective, and reliable application. The best way to do this is to involve both auditors and those being audited in the procedure design. Audit procedures should be tailored to the specific facility/operation being audited. Documented procedures should be used to train both auditors and those accountable for operations being audited. Procedures can be launched using a pilot facility approach to allow for initial testing and fine-tuning. Keep procedures current and continually improve them based on practical application. Audits include document and record review (corporate and facility), interviews, and observations.
- Protocols & tools. Develop specific and targeted protocols that are tailored to operational characteristics and based on applicable regulations and requirements for the facility. Use “widely accepted or standard practice” as go-by tools to aid in developing protocols (e.g., ASTM site assessment standards; ISO 14010 audit guidance; audit protocols based on EPA, OSHA, MSHA, Canadian regulatory requirements; GEMI self-assessment tools; proprietary audit protocol/tools). As protocols are updated, the ability to evaluate continuous improvement trends must be maintained (i.e., trend analysis).
- Information management & analysis. Procedures should be well-defined, clear, and consistent to enable the organization to analyze trends, identify systemic causes, and pinpoint recurring problem areas. Analysis should prompt communication of issues and differentiation among findings based on significance. Audit reports should be issued in a predictable and timely manner. It is desirable to orient the audit program toward organizational learning and continual improvement, rather than a “gotcha” philosophy. “Open book” approaches help learning by letting facility managers know in advance what the audit protocols are and how the audits will be conducted.
- Verification & corrective action. Corrective actions require corporate review, top management-level attention and management accountability for timely completion. A robust root cause analysis helps to ensure not just correction/containment of the existing issue, but also preventive action to assure controls are in place to prevent the event from recurring. For example, if a drum is labeled incorrectly, the corrective action is to relabel that drum. A robust plan should also look for other drums than might be labeled incorrectly and to add and communicate an effective preventive action (e.g., training or posting signs showing a correctly labeled drum).
Read the part 2 audit program best practices.
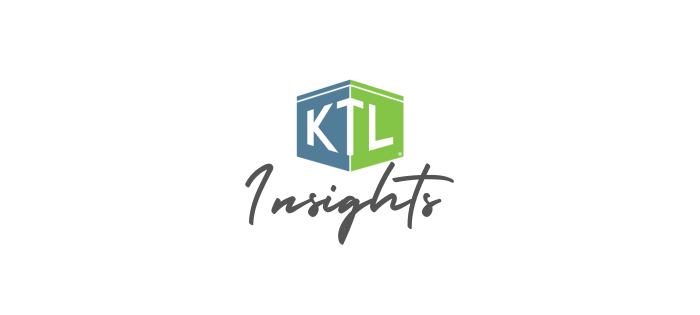
10 Reasons to Implement a Management System
A management system is the framework that enables companies to achieve their operational and business objectives through a process of continuous improvement. In its simplest form, a management system implements the Plan, Do, Check, Act/Adjust cycle. Several choices are available for management systems (ISO is commonly applied), whether they are certified by third-party registrars and auditors, self-certified, or used as internal guidance and for potential certification readiness.
Business Benefits of a Well-Documented Management System
The connection between management systems and compliance is vital in avoiding recurring compliance issues and in reducing variation in compliance performance. In fact, reliable and effective regulatory compliance is commonly an outcome of consistent and reliable implementation of a management system.
Beyond that, there are a number of business reasons for implementing a well-documented management system (environmental, safety, quality, food safety, other) and associated support methods and tools:
- Establishes a common documented framework to achieve more consistent implementation of compliance policies and processes—addressing the eight core functions of compliance:
- Inventories
- Permits and authorizations
- Plans
- Training
- Practices in place
- Monitoring and inspection
- Records
- Reporting
- Provides clear methods and processes to identify and prioritize risks, set and monitor goals, communicate those risks to employees and management, and allocate the resources to mitigate them.
- Shifts from a command-and-control, centrally driven function to one that depends heavily on teamwork and implementation of a common system, taking into consideration the necessary local differences and building better know-how at the facility level.
- Establishes a common language for periodic calls and meetings among managers, facility managers, and executives, which yields better goal-setting, priority ranking, and allocation of resources to the areas with greatest risk or the greatest opportunity to add business value.
- Empowers facilities to take responsibility for processes and compliance performance without waiting to be told “what” and “how”.
- Enables better collaboration and communication across a distributed company with many locations.
- Enables the selection and implementation of a robust information system capable of tracking and reporting on common activities and performance metrics across the company.
- Employs a design and implementation process that builds company know-how, captures/retains institutional knowledge, and enables ongoing improvement without having to continually reinvent the wheel.
- Creates consistent processes and procedures that support personnel changes (e.g., transfers, promotions, retirements) and training of new personnel without causing disruption or gaps.
- Allows for more consistent oversight and governance, yielding higher predictability and reliability.
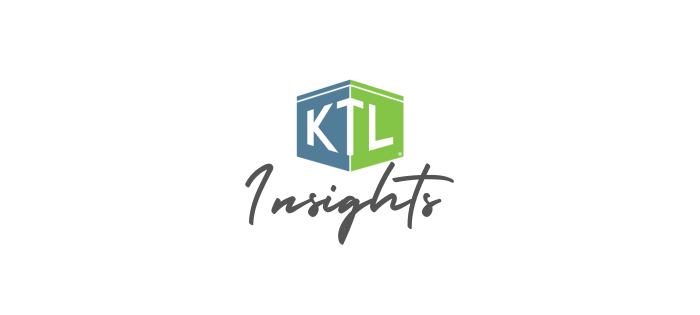
Environment / Quality / Safety
Comments: No Comments
Six Best Practices for Compliance Assurance
A well-designed and well-executed compliance assurance program provides an essential tool for improving and verifying business performance and limiting compliance risks. Ultimately, however, a compliance program’s effectiveness comes down to whether it is merely a “paper program” or whether it is being integrated into the organization and used in practice daily.
The following can show evidence of a living, breathing program:
- Comprehensiveness of the program
- Dedicated staff and resources
- Employee knowledge and engagement
- Management commitment and employee perception
- Internal operational inspections, “walk-abouts” by management
- Independent insider, plus third-party audits
- Program tailoring to greatest risks
- Consistency and timeliness of exception (noncompliance/nonconformance) disclosures
- Tracking of timely and adequate corrective/preventive action completion
- Progress and performance monitoring
Best Practices
To achieve a compliance assurance program on par with world-class organizations, there are a number of best practices that companies should employ:
- Know the requirements. This means maintaining an inventory of regulatory compliance requirements for each compliance program, as well as of state/local/contractual binding agreements applying to operations. It is vital that the organization keep abreast of current/upcoming requirements (federal, state, local).
- Plan and develop the processes to comply. Identify and assess compliance risks, and then set objectives and targets for performance improvement based on top priorities. From here, it becomes possible to then define program improvement initiatives, assign and document responsibilities for compliance (who must do what and when), develop procedures and tools, and then allocate resources to get it done.
- Assure compliance in operations. The organization needs to establish routine checks and inspections within departments to evaluate conformance with sub-process procedures. Process audits should be designed and implemented to cut across operations and sub-processes in order to evaluate conformance with company policies and procedures. Regulatory compliance audits should further be conducted to address program requirements (e.g., environmental, safety, mine safety, security). Audit performance must be measured and reported, and then expectations set for operating managers to take responsibility for compliance.
- Take action on issues and problems. Capture, log, and categorize noncompliance issues, process non-conformances, and near misses. Implement a corrective/preventive action process based on importance of issues. Be disciplined in timely completion, close-out, and documentation of all corrective/preventive actions.
- Employ management of change (MOC) process. Robust MOC processes help ensure that changes affecting compliance (to facility, operations, personnel, infrastructure, materials, etc.) are reviewed for their impacts on compliance. Compliance should be assured before the changes are made. Failure to do so is one of the most common root causes of noncompliance.
- Ensure management involvement and leadership. Set the tone at the top. The Board of Directors and senior executives must set policy, culture, values, expectations, and goals. It is just as important that these individuals are the ones to communicate across the organization, to demonstrate their commitment and leadership, to define an appropriate incentive/disincentive system, and to provide ongoing organizational feedback.
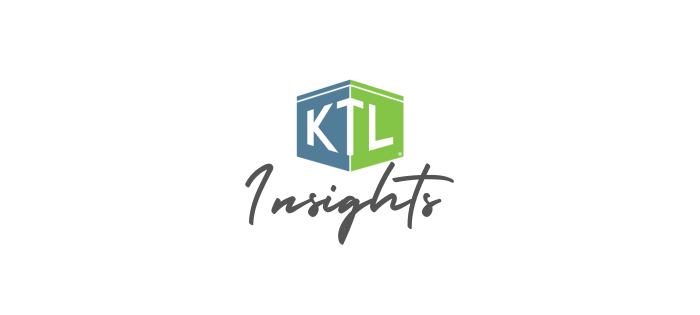
Comments: No Comments
Predictive Analytics in Incident Prevention
Companies are generating ever increasing amounts of data associated with business operations, leading to renewed interest in predictive analytics, a field that analyzes large data sets to identify patterns, predict outcomes, and guide decision-making. Companies are also facing a complex and ever expanding array of operational risks to proactively identify and mitigate. While many companies have begun using predictive analytics to identify marketing/sales opportunities, similar strategies are less common in risk management, including safety.
Classification algorithms, one general class of predictive analytics, could be particularly beneficial to the refining and petrochemical industries by predicting the time frame and location of safety incidents based on safety related inspection and maintenance data, essentially leading indicators. There are two main challenges associated with this method: (1) ensuring that leading indicators being measured are actually predictive of incidents, and (2) measuring the leading indicators frequently enough to have predictive value.
Kestrel’s article in the Q3 2018 edition of Petroleum Technology Quarterly (PTQ) features a case study to illustrate this process. Using regularly updated inspection data, the author developed a model to predict where broken rails are likely to occur in the railroad industry. The model was created using a logistic regression modified by Firth’s penalized likelihood method, and predicts broken rail probabilities for each mile of track. Probabilities are updated as additional data are collected.
In addition to predicted broken rail probabilities, the model identifies the variables with the most predictive validity (those that significantly contribute to broken rails). Using the model results, the railroad was able to identify exactly where to focus maintenance, inspection, and capital improvement resources and what factors to address during these activities. Validation tests of the model revealed 70% of the actual broken rail incidents occurred on the 20% of segments at highest risk for broken rails.
The same methodology could be used in the refining and petrochemical industries to manage risks by predicting and preventing incidents, provided that organizations:
- Identify leading indicators with predictive validity
- Regularly measure leading indicators (inspection, maintenance, and equipment data)
- Create a predictive model based on measured indicators
- Update the model as data are gathered
- Use the outputs to prioritize maintenance, inspections, and capital improvement projects and review operational processes/practices.
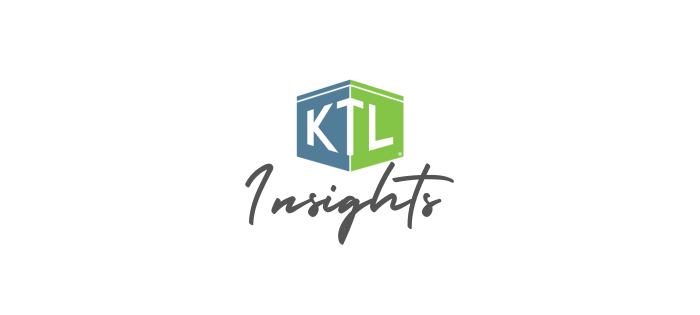
Comments: No Comments
Applying Predictive Analytics in Safety
In recent years, companies have been generating vast and ever-increasing amounts of data associated with business operations. This trend has led to renewed interest in predictive analytics, a field which focuses on analyzing large data sets to identify patterns and predict outcomes to help guide decision-making. While many leading companies use predictive analytics to identify marketing and sales opportunities, similar data analysis strategies are less common in occupational and process safety. Although the use of predictive analytics is less common in the field of safety, the potential benefits of analyzing safety data are considerable.
Just as companies are currently using customer data to predict customer behavior, safety and incident data can be used to predict when and where incidents are likely to occur. Appropriate data analysis strategies can also identify the key factors that contribute to incident risk, thereby allowing companies to proactively address those factors to avoid future incidents.
Predictive Analytics: In Theory
Let’s take a step back and look at what predictive analytics is and what it does. Predictive analytics is a broad field encompassing aspects of various disciplines, including machine learning, artificial intelligence, statistics, and data mining. Predictive analytics uncovers patterns and trends in large data sets for the purpose of predicting outcomes before they occur. One branch of predictive analytics, classification algorithms, could be particularly beneficial to industry, especially when it comes to avoiding incidents.
Classification algorithms can be categorized as supervised machine learning. With supervised learning, the user has a set of data that includes predictive variable measurements that can be tied to known outcomes. The algorithms identify the relationships between various factors and those outcomes to create predictive rules (i.e., a model). Once created, the model can be given a dataset with predictive variable measurements and unknown outcomes, and will then predict the outcome based on the model rules.
Predictive Analytics: In Practice
Like many in the transportation industry, this railroad had experienced a number of derailments caused by broken rails. Broken rail derailments can have particularly severe consequences, since they typically occur on mainline tracks, at full speed, and with no warning of the impending broken rail. Kestrel was asked to create a predictive model of track-caused derailments on a mile-by-mile basis to identify areas of high broken rail risk so the railroad could target those areas for maintenance, increased inspections, and capital improvement projects.
Penalized Likelihood Logistic Regression
As described above, classification models learn predictive rules in an original data set that includes known outcomes, then apply the learned rules to a new data set to predict outcomes and probabilities. In this case study, Kestrel used a logistic regression modified by Firth’s penalized likelihood method to:
- Fit the model
- Identify eleven significant predictive variables (based largely on past incidents)
- Calculate broken rail probabilities for each mile of mainline track based on track characteristics
Final Model
The final model calculates a predicted probability of a broken rail occurring on each mile of track over a two-year period. The results suggest that the final model effectively predicted broken rail risk, with 33% of broken rails occurring on the riskiest 5% of track miles and 70% occurring in the riskiest 20%. Further, the model shows that the greatest risk reduction for the investment may be obtained by focusing on the 2.5% of track miles with the highest probability of a broken rail. This ability to predict where broken rails are likely to occur will allow the company to more effectively manage broken rail derailment risk through targeted track inspections, maintenance, and capital improvement programs.
Implications for Other Industries
The same general approach described in the above case study can also be applied to other industries—using KPIs to determine predictive variables and incidents as the outcome. The process is as follows:
- Measurements for defined variables would be taken regularly at each facility or unit. Precision increases as the measurements become more frequent and the observed area (facility/unit) becomes smaller.
- Once a sufficient number of measurements has been taken, they would then be combined with incident data to provide both the predictive variable measurements and the outcome data needed for training a model. This dataset would be fed into a logistic regression or other classification algorithms to create a model.
- Once the model has been created, it can be applied to new measurements to predict the probability of an incident occurring at that location during the applicable timeframe.
Once predicted incident probabilities have been found, management would be able to focus improvement resources on those locations that have the highest probabilities of experiencing an incident. The classification algorithms also identify which factors have predictive validity, so management will know how improving those factors will affect the predicted probability of incidents occurring. In other words, they will know which factors have the strongest relationship with incidents and can focus on improving those first.
Data-Driven Decisions
Industrial companies are generating and recording unprecedented amounts of data associated with operations. Those that strive to be best-in-class need to use that data intelligently to guide future business decision-making.
The versatility of predictive analytics, including the method described in this case study, can be applied to help companies analyze a wide variety of problems. In this way, companies can:
- Explore and investigate past performance
- Gain the insights needed to turn vast amounts of data into relevant and actionable information
- Create statistically valid models to facilitate data-driven decisions
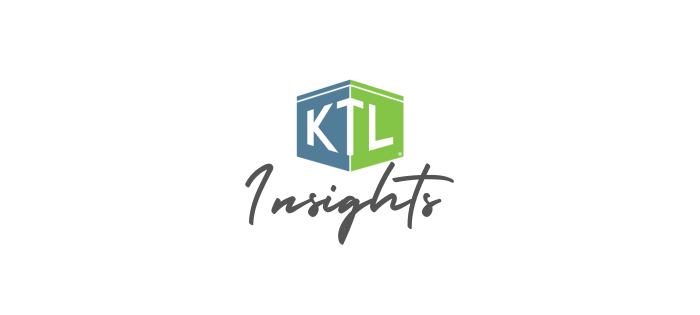
Comments: No Comments
Q&A: The New ISO 45001 Standard
What is ISO 45001?
ISO 45001 is a new international standard created by the International Organization for Standardization (ISO) that specifies requirements for an occupational, health & safety management system (OHSMS). It provides a framework for managing the prevention of death, work-related injury, and work illnesses. The ultimate goal of the standard is to help organizations proactively improve OHS performance and create a safe and healthy workplace.
Note that ISO 45001 provides guidance. It does not state specific criteria for OHS performance, nor is it prescriptive about the OHSMS design. It is a management tool for voluntary use by organizations to minimize OHS risks.
Why is ISO 45001 necessary?
There are several reasons why the creation of an international standard to manage OHS performance is necessary:
- First and foremost, organizations are responsible for minimizing the risk of harm to all individuals that may be impacted by their activities. The standard aims to protect human lives by encouraging organizations to create a safer, healthier workplace.
- According to the International Labour Organization (ILO), there were 2.34 million deaths worldwide in 2013 as a result of worker activities. The greatest majority (2 million) are associated with health issues, as opposed to injuries. The economic burden associated with this number of occupational injuries and illnesses is significant. Organizations must manage all their risks—including OHS—to survive. Poor OHS management can result in loss of key employees, business interruption, claims, higher insurance premiums, regulatory action, reputational damage, loss of investors, and loss of business.
- Finally, increased globalization creates new OHS challenges. ISO 45001 is an international standard that promotes global conformity.
What are the key aspects of ISO 45001?
Many of the elements of ISO 45001 are the same or similar to those found in OSHAS 18001. However, there are additions and changes in ISO 45001 that differentiate the new standard.
ISO 45001 establishes new roles for the organization’s people. First, it emphasizes worker participation in the OHSMS. This includes ensuring that workers are competent and have the appropriate skills to safely perform their tasks. Second, the role of top management is different than in OHSAS 18001. Of note, a designated Management Representative is no longer required; however, those individuals in management roles are expected to take ownership and demonstrate a commitment to OHS through leadership. Top management must demonstrate direct involvement and engagement with the OHSMS by:
- Ensuring the organization’s OHS policy and objectives are compatible with the overall strategic direction of the organization
- Integrating OHSMS processes and requirements into business processes
- Developing and promoting an OHS culture that supports the OHSMS
- Being accountable for the OHSMS’s effectiveness
In addition to people, ISO 45001 follows a risk-based approach that advocates prevention. This requires identifying activities that could harm those working on behalf of the organization. A large part of this involves understanding the “context” of the organization, another new element of ISO 45001. Organizations must be able to identify all external and internal factors that have the potential to impact OHS management objectives and results.
To address risks and opportunities, there are new clauses related to hazard identification, as well. As with other sections of the standard, hazard identification becomes a process rather than a procedure and, importantly, considers all individuals near the workplace who may be impacted by the organization’s activities. ISO 45001 further outlines a more defined hierarchy for organizations to determine appropriate controls.
How does ISO 45001 fit in with other ISO standards and management system approaches?
ISO 45001 follows the same high-level management system approach being applied to other ISO management system standards (e.g., ISO 14001 and ISO 9001)—Annex SL. Because of this, the ISO 45001 requirements should be consistent with the other standards to allow for relatively easy alignment and integration into the organization’s overall management processes.
In addition, ISO 45001 takes into account other OHS standards, including OHSAS 18001, ILO-OSH Guidelines, various national standards, and the ILO’s international labor standards and conventions.
What is Annex SL?
As mentioned above, Annex SL is the structure for all new and revised ISO standards. It defines the framework for a generic management system—and is then customized for each discipline. This standard structure allows for easier integration between management systems and improved efficiencies. The major clauses for all ISO management system standards are identical under Annex SL and fall into the Play-Do-Check-Act (PDCA) cycle. Organizations who have already implemented ISO 9001:2015 or ISO 14001:2015 will be familiar with the Annex SL structure.
The table below outlines the main clauses in Annex SL, as well as the OHSMS-specific clauses. Highlighted areas indicate those sections that are significant changes/additions to the existing OHSAS 18001 standard.
What does this mean for OHSAS 18001?
As outlined in the table above, ISO 45001 does not conflict with OHSAS 18001. In fact, it expands and enhances the existing standard to improve integration of the OHSMS into the overall business. ISO 45001 is intended to replace OHSAS 18001. Much like other management system standards, current users of OHSAS 18001 will need to update their systems according to the requirements of the new standard within a three-year transition period.
Who should use ISO 45001?
The short answer is everyone. ISO 45001 is designed to be a flexible management system that can be implemented by any organization, no matter the size, type, or industry. As long as the organization has people who may be affected by its activities, an OHSMS has value in ensuring worker health and safety and fulfilling legal requirements.
Why should I do this? Why are management systems like ISO 45001 beneficial?
A management system is an organizing framework that enables companies to achieve and sustain their operational and business objectives through a process of continuous improvement. A management system is designed to identify and manage risks through an organized set of policies, procedures, practices, and resources that guide the enterprise and its activities to maximize business value.
What do I do next?
- Get informed! Start reading up on ISO 45001 to get familiar with how the new standard is structured.
- Identify gaps in your existing OHSMS that will need to be addressed to meet any new requirements. If you don’t have an existing OHSMS, review the requirements and determine what pieces you may already have in place.
- Develop an implementation plan. There is a three-year transition period. Plan according to this timeline.
- Provide training. It is vital to ensure that workers and management are engaged in the OHSMS and that they are competent in any new skills/responsibilities that may be required.
- Put your plan into action. Update/develop your OHSMS to meet the ISO 45001 requirements and provide verification of its effectiveness to ensure certification.
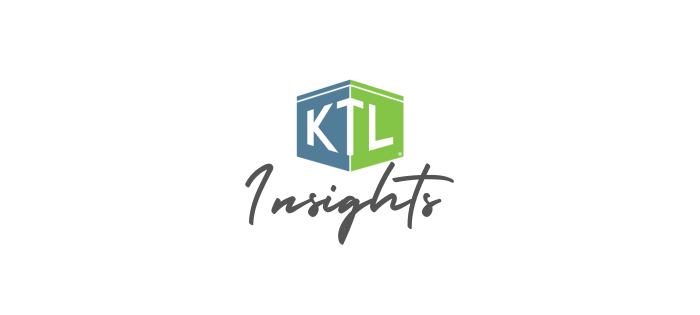
Environment / Food Safety / Quality / Safety / Technology Enabled Business Solutions
Comments: No Comments
Technology Tip: Software and Audits Top 10
All types of business and operational processes demand a variety of audits and inspections to evaluate compliance with standards—ranging from government regulations to industry codes, to system standards (i.e., ISO), to internal corporate requirements.
Audits provide an essential tool for improving and verifying compliance performance. Audits may be used to capture regulatory compliance status, management system conformance, adequacy of internal controls, potential risks, and best practices.
By combining effective auditing program design, standardized procedures, trained/knowledgeable auditors, and computerized systems and tools, companies are better able to capture and analyze audit data, and then use that information to improve business performance. Having auditing software of some sort can greatly streamline productivity and enhance quality, especially in industries with many compliance obligations.
The following tips can help ensure that companies are getting the most out of their auditing process:
- Have a computerized system. Any system is better than nothing; functional is more important than perfect. The key is to commit to a choice and move forward with it. Companies are beginning to recognize the pitfalls of “smart people” audits (i.e., an audit conducted by an expert + notebook with no protocols or systems). While expertise is valuable, this approach makes it difficult to compare facilities and results, is not replicable, and provides no assurance that everything has been reviewed. A defined system and protocol helps to avoid these pitfalls.
- Invest time before the audit. The most important time in the audit process is before the audit begins. Do not wait until the day before to prepare. There is value in knowing the scope of the audit, understanding expectations, and developing question sets/protocol. This is also the time to ensure that the system collects the data desired to produce the final report.
- Capture data. Data is tangible. You can count, sort, compare and organize data so it can be used on the back end. Data allows the company to produce reports, analytics, and standard metrics/key performance indicators.
- Don’t forget about information. Information is important, too. The information provides descriptions, directions, photos, etc. to support the data and paint a complete picture.
- Be timely. Reports must be timely to correct findings and demonstrate a sense of urgency. Reports serve as a permanent record and begin the process of remediation. The sooner they are produced, the sooner corrective actions begin.
- Note immediate fixes. During the audit, there may be small things uncovered that can be fixed immediately. These items need to be recorded even if they are fixed during the audit. Unrecorded items “never happened”. Correspondingly, it is important to build a culture where individuals are not punished for findings, as this can result in underreporting.
- Understand the audience. Who will be reading the final report? What do they need to know? What is their level of understanding? Not all data presentation is useful. In fact, poorly presented data can be confusing and cause inaction. It is important to identify key data, reports desired, and the ways in which outputs can be automated to generate meaningful information.
- Compare to previous audits. The only way to get an accurate comparison is if audits have a common scope and a common checklist/protocol. Using a computerized system can ensure that these factors remain consistent. Comparisons reinforce and support a company’s efforts to maintain and improve compliance over time.
- Manage regulatory updates. It is important to maintain a connection to past audits and the associated compliance requirements at the time of the audit. Regulations might change and that needs to be tracked. Checklists, however, may remain the same. Companies should have a process for tracking regulatory updates and making sure that the system is updated appropriately.
- Maintain data frequency. For data, the frequency is key. Consider what smaller scope, higher frequency audits look like. These can allow the company to gather more data, involve more people, and improve the overall quality and reliability of reports.
A well-designed and well-executed auditing program—with analysis of audit data—provides an essential tool for improving and verifying business performance. Audits capture regulatory compliance status, management system conformance, adequacy of internal controls, potential risks, and best practices. And using a technology tool or system to manage the audit makes that information even more useful.
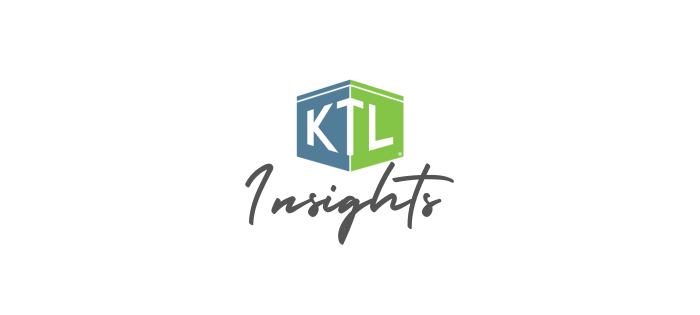
Comments: No Comments
Final Rule: Walking-Working Surfaces
OSHA has issued a final rule updating its general industry Walking-Working Surfaces standard to protect workers from slip, trip, and fall hazards. The rule also increases consistency in safety and health standards for people working in both general and construction industries.
The final rule’s most significant update is allowing employers to select the fall protection system that works best for them, choosing from a range of accepted options including personal fall protection systems.
OSHA estimates the final rule will prevent more than 5,800 injuries a year. The rule takes effect Jan. 17, 2017.
Read the full press release.
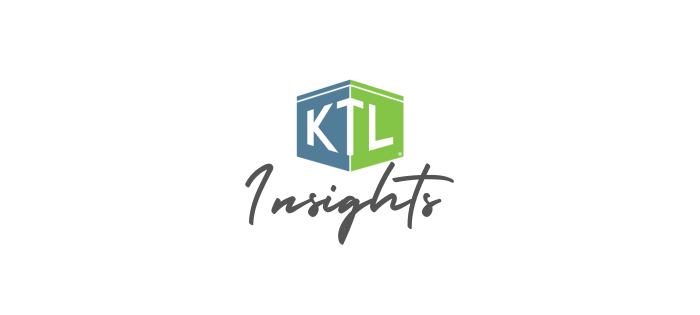
Case Study: Efficient Compliance Management
Regulatory enforcement, customer and supply chain audits, and internal risk management initiatives are all driving requirements for managing regulatory obligations. Many companies—especially those that are not large enough for a dedicated team of full-time EHS&S staff—struggle with how to effectively resource their regulatory compliance needs.
The following case study talks about how The C.I. Thornburg Co., Inc. (C.I. Thornburg) is using a technology tool to efficiently meet National Association of Chemical Distributors (NACD) and a number of other regulatory requirements.
The Challenge of Compliance
C.I. Thornburg joined NACD in January 2015. As a condition of membership, the company started the process of developing and implementing Responsible Distribution in April 2015. Responsible Distribution showcases member companies’ commitment to continuous improvement in every business process of chemical distribution—and it requires rigorous management activities to develop and maintain.
With an EHS&S department of one, managing all of those activities was a challenge for C.I. Thornburg. The company was looking for a way to streamline the process and more effectively manage Responsible Distribution requirements and regulatory compliance obligations.
Code & Compliance Elite™
C.I. Thornburg brought on Kestrel to initially help the company achieve Responsible Distribution verification. Kestrel worked with C.I. Thornburg to customize and implement Code & Compliance Elite (CCE™), an easy-to-use technology tool designed to effectively manage management system and verification requirements. Kestrel tailored the CCE™ application specifically for C.I. Thornburg to provide:
- Document management – storage, access, and version control
- Mobile device access
- Regulatory compliance management and compliance obligation calendaring
- Internal audit capabilities
- Corrective and preventive action (CAPA/CPAR) tracking and management
- Task and action management
CCE™ played a large role toward the end of C.I. Thornburg’s Responsible Distribution implementation, particularly with document control and organization, and in the verification audit. During verification, documents could be quickly referenced because of how they are organized in CCE™, making the process very efficient. According to C.I. Thornburg Director of Regulatory Compliance and EHS&S Richard Parks, “The verifier was blown away by how well we were organized and how the tool linked many documents from different regulatory policies.” The company achieved verification in May 2016.
Broadening to Other Regulatory Requirements
CCE™ is still being used to manage Responsible Distribution requirements, but C.I. Thornburg is now working with Kestrel to expand it to all regulatory branches that govern the business. Regulatory requirements function similarly—for example, Responsible Distribution has 13 codes, Department of Homeland Security (DHS) has 18 performance standards (RBPS), and OSHA PSM has 14 elements. All require internal audits and corrective action tracking—things that can be easily and effectively managed through CCE™ to create a one-stop shop for regulatory compliance. Kestrel is currently developing the DHS and PSM modules in CCE™ for C.I. Thornburg.
Valuable Management Tool
CCE™ is providing C.I. Thornburg with a valuable management tool that automates the regulatory landscape. According to Parks, as a small organization that depends on using efficient tools to manage compliance rather than adding more manpower, CCE™ has provided huge cost savings and tremendous value for the organization, including the following:
- CCE™ has become the ultimate tool inefficiency. Tasks that used to take hours to complete are now easily done in just minutes.
- The internal audit function of CCE™ makes audits seamless and tracking and follow-up easy.
- The CAPA tool ensures that the company is managing corrective actions and completing follow-up activities and tasks.
- The functionality of CCE™ allows for managing multiple regulatory dashboards, providing a one-stop shop for managing regulatory compliance obligations.
- CCE™ creates an organized document structure that enables easy access to information and quick response to auditors.
- During Senior Management Review, senior managers see the benefit of being able to reference the history of corrective actions and audits through CCE™.
“A lot of NACD member companies are small organizations that have limited resources to effectively manage all EHS&S needs,” said Parks. “CCE™ really creates the department and is a huge value to small businesses. With the CCE™ technology and a company’s clearly defined goal, Kestrel can provide an efficient solution to most any need.”
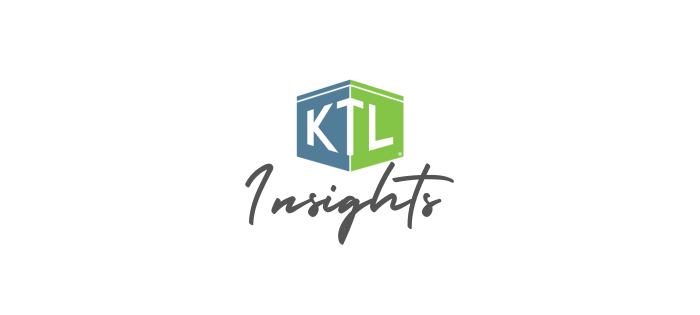
Comments: No Comments
Applying Predictive Analytics to Leading Indicators
Leading indicators can be defined as safety-related variables that proactively measure organizational characteristics with the intention of predicting and, subsequently, avoiding process safety incidents. Leading indicators become especially powerful when combined with advanced statistical methods, including predictive analytics.
Case Study
Kestrel developed a major incident predictive analytical model for the transportation industry that is also applicable to the process industries. Using regularly updated inspection data, the model was created to provide major incident probabilities for each transportation segment over a six-month period.
Additionally, the model identifies the variables that are significantly contributing to major incidents, thereby showing the company which factors to address to prevent future incidents. Model validation revealed that it could successfully predict the location and time frame of 75% of major incidents.
Broader Applicability
Companies in the process industries are generating and recording unprecedented amounts of data associated with operations. Companies that strive to be best-in-class need to use that data intelligently to guide future business decision-making.
The versatility of predictive analytics, including the method described in this case study, can be applied to help companies analyze a wide variety of problems. In this way, companies can:
- Explore and investigate past performance
- Gain the insights needed to turn vast amounts of data into relevant and actionable information
- Create statistically valid models to facilitate data-driven decisions
Join Kestrel at the 2016 International Symposium
Kestrel’s William Brokaw will be presenting the case study discussed above on Tuesday, October 25 at 1:15 p.m. at the Mary Kay O’Connor Process Safety Center 2016 International Symposium: Applying Predictive Analytics to Process Safety Leading Indicators.
MKOPSC 2016 International Symposium
October 25-27, 2016
Hilton Conference Center
College Station, Texas
Kestrel’s experts will also be on hand throughout the Symposium to talk with you. Stop by and see us at our booth. We welcome the opportunity to learn more about your needs and to discuss how we help our chemical and oil & gas clients manage environmental, safety, and quality risks; improve safety performance, and achieve regulatory compliance assurance.