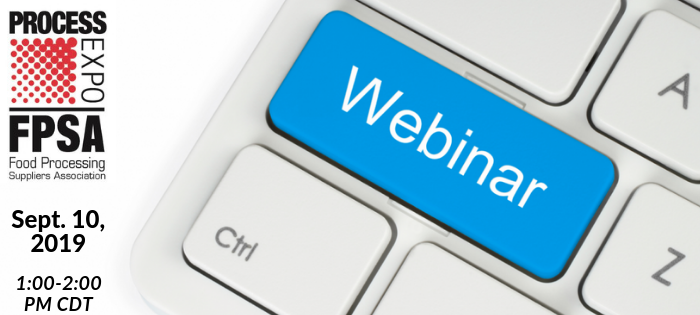
Comments: No Comments
Free Webinar Highlighting PROCESS EXPO Food Safety Training
Are you registered for the PROCESS EXPO’s special food safety training courses? Find out why you should be!
Join Kestrel Principals Bill Bremer & Roberto Bellavia and our team of food safety experts on Tuesday, September 10 for a sneak peek into the special food safety training courses being offered as part of PROCESS EXPO 2019. You’ll get an overview of the courses, what you can expect to learn, and why each of these courses is so important to companies operating in the food industry.
FREE Webinar!
Tuesday, September 10, 2019
1:00-2:00 pm CDT
Food Safety Training Courses
This FDA training is designed to help industry, particularly small- and medium-sized companies, to comply with the new preventive controls rules. The following supplemental food safety training courses will be featured at PROCESS EXPO from Monday, October 7 – Wednesday, October 9 and highlighted in the September 10 webinar.
Preventive Controls for Animal Food
This 2.5-day course is being made available in response to FDA’s final rule requiring covered animal food facilities to establish and implement an animal food safety system that includes an analysis of hazards and implementation of risk-based preventive controls. Completing this course meets FSMA requirements for a PSQI.
Foreign Supplier Verification Program (FSVP) Training
This 2.5-day course will provide participants with the knowledge to implement the requirements of the Foreign Supplier Verification Program (FSVP) for Importers of Food for Humans and Animals regulation of FDA’s FSMA. The FSVP course meets FSMA compliance, and FPSA certificates will be issued upon successful completion of the course.
HACCP Training
HACCP is a systematic preventive approach to food safety from biological, chemical and physical hazards in production processes that can cause the finished product to be unsafe and designs measures to reduce these risks to a safe level. This is a certified 2-day course based on Global Codex and GFSI requirements.
Produced by the Food Processing Suppliers Association (FPSA), PROCESS EXPO is the nation’s largest trade show dedicated to bringing the latest technology and integrated solutions to all segments of the food and beverage processing and packaging industry.
FREE Webinar: Sept. 10, 2019
PROCESS EXPO: Oct. 8-11, 2019
Food Safety Training: Oct. 7-9, 2019
McCormick Place | Chicago, Illinois
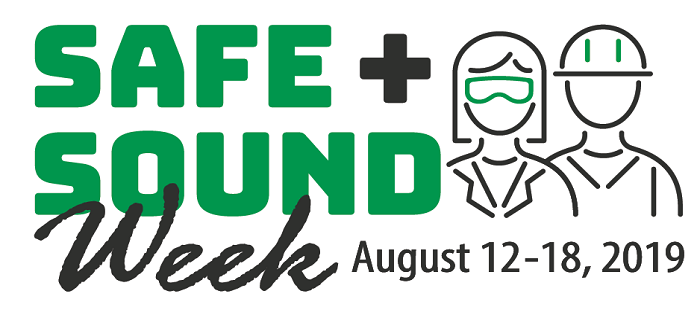
Comments: No Comments
OSHA Kicks Off Safe + Sound Week
The Occupational Safety and Health Administration (OSHA) is joining businesses and organizations nationwide to recognize the importance and successes of workplace safety and health programs during Safe + Sound Week: August 12-18, 2019.
The week-long event encourages employers to implement workplace safety initiatives, and highlight workers’ contributions to improving safety. Businesses that incorporate safety and health programs can help prevent injuries and illnesses, reduce workers’ compensation costs, and improve productivity.
Participating in Safe + Sound Week can help get your program started, energize an existing one, or provide a chance to recognize your safety successes. Learn more about how to help plan and promote safety and health plans.
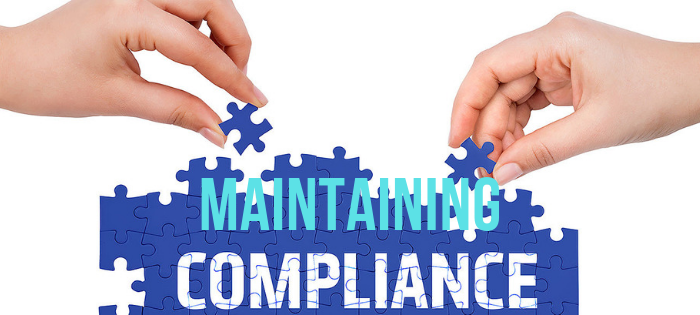
Maintaining a Compliance Assurance Program
A well-designed and well-executed compliance assurance program provides an essential tool for improving and verifying business performance and limiting compliance risks. Ultimately, however, a compliance program’s effectiveness comes down to whether it is merely a “paper program” or whether it is being integrated into the organization and used in practice on a daily basis.
The following can show evidence of a living, breathing program:
- Comprehensiveness of the program
- Dedicated staff and resources
- Employee knowledge and engagement
- Management commitment and employee perception
- Internal operational inspections, “walkabouts” by management
- Independent insider, plus third-party audits
- Program tailoring to greatest risks
- Consistency and timeliness of exception (noncompliance/nonconformance) disclosures
- Tracking of timely and adequate corrective/preventive action completion
- Progress and performance monitoring
Best Practices
To achieve a compliance assurance program on par with world-class organizations, there are a number of best practices that companies should employ:
Know the requirements. This means maintaining an inventory of regulatory compliance requirements for each compliance program, as well as of state/local/contractual binding agreements applying to operations. It is vital that the organization keep abreast of current/upcoming requirements (federal, state, local).
Plan and develop the processes to comply. Identify and assess compliance risks, and then set objectives and targets for performance improvement based on top priorities. From here, it becomes possible to then define program improvement initiatives, assign and document responsibilities for compliance (who must do what and when), develop procedures and tools, and then allocate resources to get it done.
Assure compliance in operations. The organization needs to establish routine checks and inspections within departments to evaluate conformance with sub-process procedures. Process audits should be designed and implemented to cut across operations and sub-processes in order to evaluate conformance with company policies and procedures. Regulatory compliance audits should further be conducted to address program requirements (e.g., environmental, safety, mine safety, security). Audit performance must be measured and reported, and the expectations set for operating managers to take responsibility for compliance.
Take action on issues and problems. Capture, log and categorize noncompliance issues, process nonconformances, and near misses. Implement a corrective/preventive action process based on the importance of issues. Be disciplined in timely completion, close-out, and documentation of all corrective/preventive actions.
Employ management of change (MOC) process. Robust MOC processes help ensure that changes affecting compliance (to the facility, operations, personnel, infrastructure, materials, etc.) are reviewed for their impacts on compliance. Compliance should be assured before the changes are made. Failure to do so is one of the most common root causes of noncompliance.
Ensure management involvement and leadership. Set the tone at the top. The Board of Directors and senior executives must set policy, culture, values, expectations, and goals. It is just as important that these individuals are the ones to communicate across the organization, to demonstrate their commitment and leadership, to define an appropriate incentive/disincentive system, and to provide ongoing organizational feedback.
Maintaining Ongoing Compliance
The compliance assurance program must be a living, breathing program. As risks change, the program must be refreshed, refined, and redeployed. A management system framework can help ensure operational sustainability. A management system drives the auditing process and helps companies say what they will do, do what they say and, importantly, verify it.
Together, there is a real value at the intersection of a compliance assurance program and management systems. Management systems define the internal controls that are in place to reduce risks, prevent losses, and sustain and improve performance over time through the Plan-Do-Check-Act (PDCA) cycle of continual improvement.
Testing and Monitoring
Testing, monitoring, and measuring are crucial elements of this cycle. Without them, it is difficult to understand what is working and what needs improvement. Robust testing and monitoring programs can serve as early warning systems for identifying potential compliance risks before they become enforcement issues.
Compliance should be tested and monitored throughout each level of the organization. A strong testing program will evaluate the results of the compliance risk assessment and assign compliance risks to the business units and processes where they are most likely to occur, creating clear lines of responsibility and accountability. Key risks and the related controls should be tested periodically using statistically valid sampling methodologies, and monitoring activities should be performed on an ongoing basis. Doing so produces trend data that provides the rationale needed for making changes to underlying business processes, as well as emerging risks.
Ongoing compliance excellence relies on top management, operations managers, EHS personnel, and individual employees throughout the organization working together to build and sustain an organizational culture that places compliance on par with business performance. Senior management must focus on the overall culture of the company in terms of taking the necessary steps to reduce risk and make prevention part of daily operations. While it may be impossible to eliminate all risk exposure, a solid risk framework, assessment methodology, and compliance assurance program can help to prioritize risks for active management, sustained compliance, and positive business impacts.
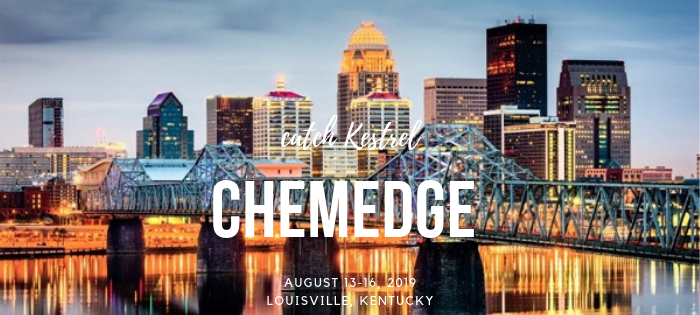
Comments: No Comments
Catch Kestrel at ChemEdge: August 13-19 in Louisville
Are you challenged with…
- Staying on top of EHS&S regulatory compliance?
- Managing your Responsible Distribution verification requirements?
- Handling increased demands from food safety requirements?
- Having the appropriate tools and resources to efficiently manage it all?
Kestrel Management can help.
Kestrel’s Jake Taylor and Liz Hillgren will be available throughout ChemEdge and would enjoy the opportunity to talk further about your company’s challenges—and how we can help. Here’s where you can find us in Louisville:
- August 12, 8:00 am – 5:00 pm – Pre-Con Responsible Distribution Workshop
- August 15, 11:30-12:30 pm – Session: Environmental Auditing for Value-Added Peace of Mind
- August 13 -16 – Exhibition Booth #302
Kestrel Session: Environmental Auditing for Value-Added Piece of Mind
Environmental auditing is a management tool that can be used to evaluate and monitor the internal performance and compliance of your company with environmental regulations and standards. An audit can also be used to determine the overall effectiveness of an existing system within your company. This interactive session will incorporate NACD member feedback on compliance auditing practices to help you maximize best practices for compliance, efficiency, and value within the industry.
Partnering with NACD
Kestrel has been a long-standing NACD Preferred Compliance Provider and Responsible Distribution Adviser, providing leading EHS and food safety compliance expertise and Responsible Distribution assistance. Whether helping members address compliance needs, managing Responsible Distribution verification requirements, or creating adaptable technology solutions tailored to your business needs, Kestrel will help address your challenges.
We look forward to seeing our clients and friends—both old and new—at ChemEdge in Louisville!
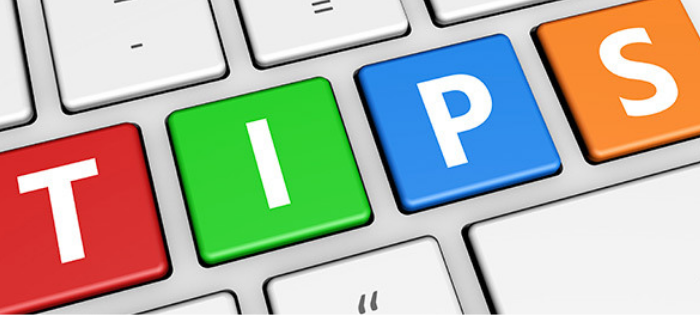
Top 8 Tips for Building a New Compliance IMS
- Inventory your existing systems – Identify how you are currently managing your compliance needs/requirements. What’s working well? What isn’t working? Do the systems work together? Do they all operate independently? This inventory should evaluate the following:
- Current systems and tools
- Status and functionality of existing processes
- Data sources and ability to pull information from various sources
- Organizational complexity
- Compliance status
- Existing management systems
- Determine your business drivers – Are you looking to save time? Create efficiencies? Reduce the number of resources required? Have better access to real-time information? Answer to senior management? Respond to regulatory requirements? These drivers will also drive the decisions you make when it comes to module development, dashboard design, reporting, and more.
- Understand the daily routine of the individuals using the system – Systems and modules should be built according to existing daily routines, when possible, and then implemented and rolled out in a way that encourages adoption. Having a solid understanding of routine tasks and activities will ensure that the system is built in a way that works for the individuals using it.
- Understand your compliance requirements – Do you have permitting requirements? Does your staff need training? How do you maintain your records? Are there regular (e.g., annual, semi-annual) plans and/or reports you need to submit? Do you have routine inspections and monitoring? All of these things can and should be built into a compliance IMS so they can be managed more efficiently.
- Get the right parties involved – There are many people that touch a compliance IMS at various points in the process. The system must be designed with all of these users in mind: the end user entering data in the field, management who is reading reports and metrics, system administrator, etc. A truly user-friendly system will be something that meets the needs of all parties. If employees are frustrated by lack of understanding, if the system isn’t intuitive enough, if it is hard to put data in or get metrics out, the system will hold little value.
- Make your wish list – While you may start your project one module at a time, it is important to define your ultimate desired end state. In a perfect world, how would the system operate? What parts and components would it have? How would things work together? What type of interfaces would users have?
- Set your priorities, budget, and pace – What is the most important item on your list? Do you want to develop modules one at a time or as a fully functional system? It often makes sense to start where you already have processes in place that can be more easily transitioned into a new system to encourage user buy-in. Priorities should be set based on ease of implementation, compliance risk, business improvement, and value to your company.
- Select the right consultant – For a compliance IMS, it is valuable to have a consultant who doesn’t just understand technology but also understands your operational needs, regulatory obligations, and compliance issues. An off-the-shelf software solution isn’t a silver bullet. A consultant who can understand the bigger picture of where you want to go and will collaborate to design the right compliance IMS and efficiency tools will bring the most value to your organization.
- Understanding the bigger picture of where you want to go. We ensure your system is scalable and flexible; upfront planning enhances the outcome more efficiently.
- Collecting and organizing the information in a way that reflects how you conduct business and that aligns with other systems/processes.
- Offering guidance on compliance best practice and what modules and level of customization will bring you the most value.
- Providing as needed compliance support (e.g., review of existing forms and checklists, program improvement, development of training content, compliance audits, audit protocol).
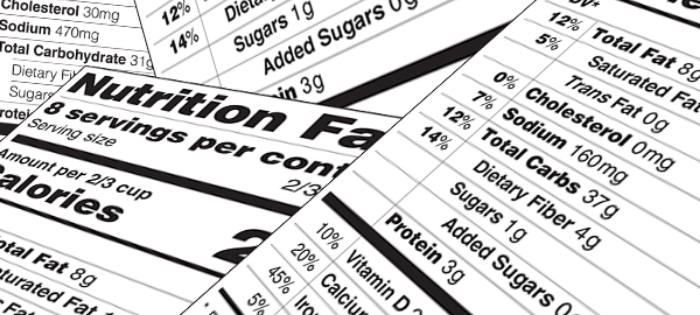
Comments: No Comments
Food Labeling: Compliance Check
The Regulations
Nutrition Labeling and Education Act (NLEA) The Nutrition Labeling and Education Act (NLEA) was signed into law in 1990. The Act requires most foods to contain nutrition labeling. In addition, it requires all nutrient content claims (i.e., high fiber, low fat, etc.) and health claims be consistent with Food and Drug Administration (FDA) regulations. Compliance with the nutrition labeling regulations is based on the date the product was labeled, as opposed to the date the product is offered for entry into interstate commerce. NLEA requires information in the following four areas:- Nutrition Facts Panel
- Ingredient List
- Allergen Statements
- Nutrition Content Claims
- January 1, 2020 for manufacturers with > $10 million in annual sales
- January 1, 2021 for manufacturers with < $10 million in annual food sales
- July 1, 2021 for manufacturers of single-ingredient sugars, such as honey, maple syrup and certain cranberry products
Compliant Labels
Nutrition labeling can be complex and confusing, particularly for first-time food manufacturers. There are very specific requirements that must be addressed to remain compliant not only with FDA requirements, but also with many vendors who require verification of labeling compliance as a condition of doing business (e.g., Amazon, Walmart, Costco). The following label components must be developed and then continually reviewed to identify which labels need further modification and to ensure ongoing compliance:- Nutrition Facts Panel is included on all packaging in a place where it can easily be seen by consumers. The panel includes the following:
- Serving size and servings per container, per FDA guidelines
- Calories per serving
- Nutrient values of the following:
- Total fat (saturated and trans fats)
- Cholesterol
- Sodium
- Total carbohydrates (dietary fibers and sugars)
- Protein
- Vitamin A
- Vitamin C
- Calcium
- Iron
- Ingredient List must include all ingredients and sub-ingredients present in the product in the order of predominance by weight in the product.
- Allergen Statements present a high-risk area, as they alert the consumer to the presence of one of more of the top eight allergens:
- Milk
- Eggs
- Fish
- Crustacean shellfish
- Tree nuts
- Wheat
- Soybeans
- Peanuts
- Nutrition Content Claims include statements such as low fat, high fiber, low sodium, and can help a company positively market food products. However, these claims must be checked, as each has specific requirements established by the FDA.
Why Comply?
At the most basic level, non-compliance can result in products being pulled from store shelves. However, there are other implications to also consider:- Improper labeling may impact a company’s ability to supply product to larger retailers with specific requirements.
- It can destroy the integrity of a company who makes false product claims or provides inaccurate nutritional information.
- It can result in legal action if inaccuracies present high risks (e.g., allergen statements, nutritional claims).
- Keep track of the most current regulatory requirements, as well as uniform compliance dates (and any other established compliance dates).
- Develop product labeling to ensure labels include the required information.
- Regularly review product labeling to identify any modifications to maintain compliance, particularly due to regulatory changes.
- Preserve the integrity of the company by ensuring consumers are provided with accurate information regarding all products.
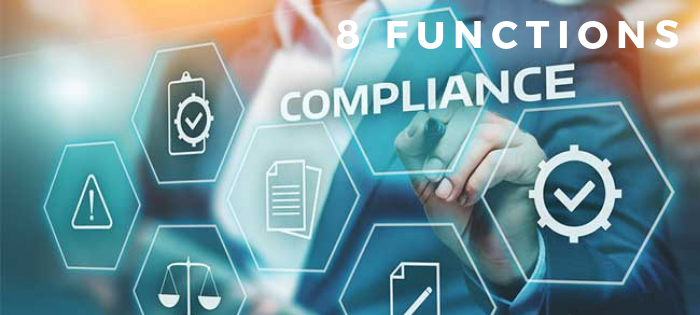
Environment / Food Safety / Quality / Safety / Technology Enabled Business Solutions
Comments: No Comments
Technology & the 8 Functions of Compliance
Virtually every regulatory program—environmental, health & safety, security, food safety—has compliance requirements that call for companies to fulfill a number of common compliance activities. While they do not necessarily need to be addressed all at once or from the start, considering the eight functions of compliance (as outlined below) when designing a compliance Information Management System (IMS) helps define the starting point and build a vision for the “end point” when planning IMS improvements. These compliance functions translate into modules—facility profiles, employee counts, training tracking, corrective action tracking, auditing tasks, compliance calendars, documents and records management, permit tracking, etc.—that are instrumental in establishing or improving a company’s capability to comply.
8 Functions of Compliance
- Inventory means taking stock of what exists. The outcome of a compliance inventory is an operational and EHS profile of the company’s operations and sites. In essence, the inventory is the top filter that determines the applicability of regulatory requirements and guides compliance plans, programs, and activities. For compliance purposes, the inventory is quite extensive, including (but not limited to) the following:
- Activities and operations (i.e., what is done – raw material handling, storage, production processes, fueling, transportation, maintenance, facilities and equipment, etc.)
- Functional/operational roles and responsibilities (i.e., who does what, where, when)
- Emissions
- Wastes
- Hazardous materials
- Discharges (operational and stormwater-related)
- Safety practices
- Food safety practices
- Authorizations, permits & certifications provide a “license to construct, install, or operate.” Most companies are subject to authorizations/permits at the federal, state, and local levels. Common examples include air permits, operating permits, Title V permits, safe work permits, tank certifications, discharge permits, construction authorization. In addition, there may be required fire and building codes and operator certifications. Once the required authorizations, permits, and/or certifications are in place, some regulatory requirements lead companies to the preparation and updating of plans as associated steps.
- Plans are required by a number of regulations. These plans typically outline compliance tasks, responsibilities, reporting requirements, schedule, and best management practices to comply with the related permits. Common compliance-related plans may include SPCC, SWPPP, SWMP, contingency, food safety management, and security plans.
- Training supports the permits and plans that are in place. It is crucial to train employees to follow the requirements so they can effectively execute their responsibilities and protect themselves, company assets and communities. Training should cover operations, safety, security, environment, and food safety aimed at compliance with regulatory requirements and company standards and procedures.
- Practices in place involve doing what is required to follow the terms of the permits, related plans and regulations. These are the day-to-day actions (regulatory, best management practices, planned procedures, SOPs, and work instructions) that are essential for following the required processes.
- Monitoring & inspections provide compliance checks to ensure locations and operations are functioning within the required limits/parameters and the company is achieving operational effectiveness and performance expectations. This step may include some physical monitoring, sampling, and testing (e.g., emissions, wastewater). There are also certain regulatory compliance requirements for the frequency and types of inspections that must be conducted (e.g., forklift, tanks, secondary containment, outfalls). Beyond regulatory requirements, many companies have internal monitoring/inspection requirements for things like housekeeping, sanitation, and process efficiency.
- Records provide documentation of what has been done related to compliance—current inventories, plans, training, inspections, and monitoring required for a given compliance program. Each program typically has recordkeeping, records maintenance, and retention requirements specified by type. Having a good records management system is essential for maintaining the vast number of documents required by regulations, particularly since some, like OSHA, have retention cycles for as long as 30 years.
- Reports are a product of the above compliance functions. Reports from ongoing implementation of compliance activities often are required to be filed with regulatory agencies on a regular basis (e.g., monthly, quarterly, semi-annually, annually), depending on the regulation. Reports also may be required when there is an incident, emergency, recall, or spill.
Reliable Compliance Performance
Documenting procedures on how to execute these eight functions, along with management oversight and continual review and improvement, are what eventually get integrated into an overarching management system (e.g., environmental, health & safety, food safety, security, quality). The compliance IMS helps create process standardization and, subsequently, consistent and reliable compliance performance.
In addition, completing and organizing/documenting these eight functions of compliance provides the following benefits:
- Helps improve the company’s capability to comply on an ongoing basis
- Establishes compliance practices for when an incident occurs
- Creates a strong foundation for internal and 3rd-party compliance audits and for answering outside auditors’ questions (agencies, customers, certifying bodies)
- Helps companies know where to look for continuous improvement
- Reduces surprises and unnecessary spending on reactive compliance-related activities
- Informs management’s need to know
- Enhances confidence of others (e.g. regulators, shareholders/investors, insurers, customers), providing evidence of commitment, capability, reliability and consistency in the company’s compliance program
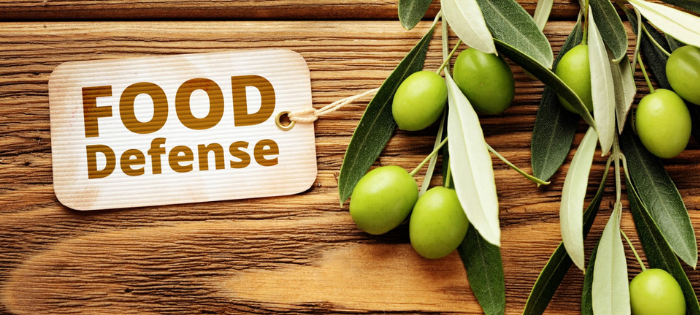
Comments: No Comments
Food Defense Strategies to Prevent Intentional Adulteration
In May 2016, FDA issued its final rule on Mitigation Strategies to Protect Food Against Intentional Adulteration (IA). This rule requires covered facilities to prepare and implement food defense plans. The first compliance date—for businesses with sales of $10 million or more per year and more than 500 full-time equivalent employees—is July 26, 2019. (Note that small businesses have until 2020 and very small businesses have until 2021.)
Just as important, FDA has announced it will begin routine inspections to verify compliance with the IA rule in March 2020. Given those dates, compliance with this rule should be a top priority for the approximately 3,400 impacted firms that operate 9,800 food facilities.
Requirements: Food Defense Plan
Let’s start by defining food defense and why it is so important. According to FDA, “Food defense is the effort to protect food from acts of intentional adulteration.” Intentional adulteration is any act where there is an intent to cause wide-scale public health harm, including acts of terrorism. As such, the rule is designed to primarily cover larger facilities with products that reach many people.
At its most basic level, the IA rule requires every covered facility to prepare and implement a food defense plan. The food defense plan incorporates four major elements:
- The vulnerability assessment identifies those areas in the process that pose the greatest IA risks. Each step in the facility’s process should be evaluated for the following:
- Potential severity and scale of the impact on the public
- Physical access to the product
- Ability to successfully alter/contaminate the product
- Facilities must develop and implement mitigation/preventive strategies at each step in the process to address vulnerabilities and minimize the risks of IA.
- A system must be put in place to ensure implementation of mitigation strategies and to effectively manage the following:
- Monitoring mitigation strategies, including frequency
- Corrective action response
- Verification activities
- Appropriate recordkeeping must be maintained for food defense monitoring, corrective actions, and verification, and key personnel must receive appropriate training.
Mock Exercise
Kestrel’s previous article on the Four A’s of Food Defense outlines a proactive approach to food defense that will help meet a key requirement by ensuring the organization is working to avoid the risks associated with food adulteration and contamination.
In addition, when conducting an assessment of food defense, IA, and generally accepted industry vulnerability, threats, and controls, Kestrel suggests completing a mock exercise scenario. This allows companies to:
- Assess their food defense and IA programs under FSMA;
- Test to confirm their program’s integrity, as documented and implemented; and
- Conduct vulnerability scenarios to verify, validate, and make improvements.
The following areas should be addressed in the assessment, strategies, and plan information:
- Facility
- Materials
- Packaging
- Processing
- Key activities
- Storage
- Transportation and distribution
- Management and personnel
A key aspect is also review of and improvements to training programs for all employees based on responsibility, recordkeeping process, management objectives, and program monitoring.
This activity provides the information needed to develop and implement an effective and compliant food defense and IA program under FSMA. Additionally, it can provide verification of the site’s programs, corrective actions to be implemented, and the necessary records of compliance.
Piece of the Puzzle
Food defense is a big piece of the FSMA puzzle. According to Kestrel Food Safety Principal Bill Bremer, “We have included food defense in virtually all of our program development activities this year for GFSI (all schemes) and now FSMA.” Kestrel has worked with over 400 food sites in passing audits and inspections that have included general or focused food defense and IA management programs in food categories including baking, candy/confection, meat, flavor/ingredients, grain, flour, packaging/contact materials, beverages, beans, chemicals, dietary supplements, commissary/catering, and more.
Doing so directly aligns with FDA’s requirements for companies to assess risk and implement preventive controls on a broad basis. Thinking about risk-based strategies—whether in the supply chain or internal systems or whether you are a grower or an importer—is key for any food company planning for the future. Preventive strategies are the essence of FSMA and HACCP. Proactively creating or updating a food defense and safety plan is the first step to ensure compliance.
Join Kestrel at the PROCESS EXPO, as we discuss this topic and others during our special food safety training courses this October in Chicago.
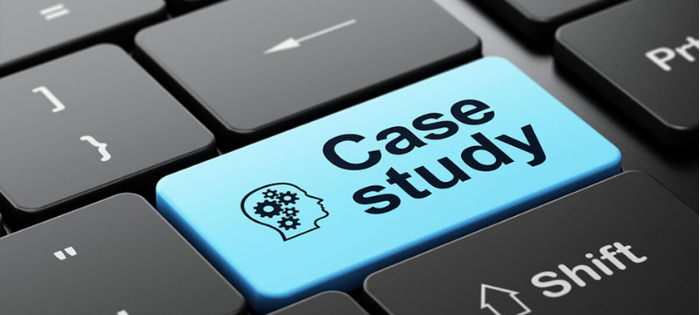
Case Study: Integrated Compliance IMS
This is the next article in Kestrel’s series about Technology-Enabled Business Solutions.
What do you do when your company has multiple grandfathered-in systems that don’t talk to each other? How about when not all locations have access to the same systems…and you have over 150 locations and are still growing? What about when employees are spending excess time collecting and combining information manually instead of electronically? What if you can’t correlate data and generate reports because of multiple systems?
Cut Your Losses, Prioritize Your Needs
These things happen—probably more frequently than one might think. For one of Kestrel’s clients, a large chemical distribution company, all these things were happening simultaneously, and the cost to upgrade existing systems to respond to these needs was getting out of hand. How do you manage that? Do you just cut your losses and find a new compliance IMS solution? Do you address one issue at a time, or does that introduce the risk that everything won’t work together? Again.
Transitioning from one system to another—whether in part or completely—isn’t simple. It takes planning and forethought to create a scalable solution that can be adapted to the company’s overall needs. Proactively managing any sort of technology transition—including prioritizing needs and scheduling how quickly modules are developed and rolled out—is key.
From the beginning, Kestrel’s EHS and IT consultants worked to fully understand the company’s operations, existing systems and workflows, and desired outcomes of the overall system before recommending an approach. Without these upfront conversations, this company could’ve ended back in the same situation with a different system. Instead, they are on their way to developing a robust and scalable compliance IMS that can be adapted to the company’s overall needs and will eventually replace their off-the-shelf software.
Starting with the Data
Our client’s initial request was for dashboard reporting that would:
- Provide a visual of the Excel reports the company was pulling from multiple independent systems, and
- Create efficiencies in the data collection and reporting approach.
During initial conversations about the company’s compliance, information management, and overall business needs, it became clear to Kestrel that the existing facility database forms the foundation for the overall system. All content stems from this database. To create the efficiencies and dashboards the company wanted, building the facility database needed to happen first.
Facility information was originally tracked on individual Excel spreadsheets that were later combined to create a quarterly report. This very manual practice presented risks of user error in data entry, data manipulation, analysis, and reporting. Kestrel developed a facility database in SharePoint to serve as a centralized list, with detailed information on each location. Multiple other databases were then created that filter content into each facility page to create a simplified view of all items associated with each facility. Those other databases currently include:
- Employee counts
- Facility audits
- Sustainability reports
- List of storage tanks, with other assets to be added in the future
- Facility images
- Managed requirements
Let’s look at the employee database as one example of data that flows into the facility database. The employee database is used to track the number of employees in each location and each department. Information is filtered into the facility database, updating the employee count section. This employee database is also used to track access/permissions to the company site, look up individuals within other forms, and assign training based on job title.
The facility database now acts as the centralized core to the entire system. Information available here can be used to drive other actions and lists within the site, such as compliance tasks, corrective and preventive actions (CAPAs), inspections, near-misses, incidents, permitting requirements, etc.
Bringing in Forms
Where does all the data in those databases come from? That is where mobile forms and checklists enter the picture. Integrating various Office 365 technologies, Kestrel is creating several mobile forms, such as the near-miss app, to allow employees in the field to capture data electronically. The forms are accessible at multiple levels and can be assigned down to an individual location. Importantly, there is no need to log in to submit data, ensuring ease of access and use for all employees.
As employees complete the forms, data is collected and uploaded into the company’s related database(s) in real-time. All forms and databases are integrated. Not only does this eliminate the problems associated with manual data entry and manipulation, it provides real-time access to valuable data.
Compliance Dashboard
Kestrel has also created a login-driven compliance dashboard that houses key metrics, compliance tasks, and an at-a-glance compliance calendar. The dashboard can be customized for various applications based on the company’s needs as they continue to use the system—employees, management, departments, divisions, facilities, etc.
Currently, various compliance tasks (and associated reminders) are assigned to individuals throughout the 150+ locations. The dashboard filters assigned tasks to the individual logged in, so each employee can view his/her compliance-related tasks. At the same time, management can view outstanding issues that fall under their area(s) of responsibility, and the calendar provides a quick overview of compliance deadlines throughout the year.
The dashboard provides additional visibility for compliance tasks and alerts management to issues that need attention/resolution across the organization. It can also incorporate data analytics to help identify patterns and trends, inform business decisions, and guide resources.
Building for the Future
Now that the company has a solid foundation, work can commence to bring the independent systems into a single platform. Kestrel’s EHS team continues to identify additional compliance management needs, including checklists and mobile forms, internal audits, permit tracking, training tracking, safety meetings, mobile inspection/audit functionality, document control, incident reporting, and more. As these needs are identified, they can be built into the larger compliance IMS to create one integrated system going forward.
As Kestrel’s lead SharePoint Specialist Jaime Doty stated in a recent Q&A, “If you know where you want to end in an ideal world, it becomes a lot easier to find the starting point. It also makes creating a scalable system much more likely, because you are designing the system with the end in mind.”
This has ensured development of a system that:
- Is built from the perspective of the people who will be using them—in the field, in the plant, in the office, in the board room
- Integrates various databases and forms into a single, familiar platform
- Allows information to be shared and tracked in multiple ways
- Gives the ability to manage sites/facilities/plants/departments for compliance purposes
- Simplifies the data entry process by providing user-friendly functionality
- Provides for continual adaptation to meet future data management and reporting needs
That is exactly the forward-thinking perspective Kestrel takes on all projects—thinking beyond individual efficiency tools, considering the desired state, and determining how technology can make that happen. By coordinating technology and compliance expertise, Kestrel offers unique capabilities and perspective. Our EHS and food safety professionals understand the regulatory obligations, business needs, and needs of the users. This drives design and development of the right compliance IMS and efficiency tools—one that works within the company’s implementation timeline and budget—to reduce compliance risk, create operational efficiencies, and generate business improvement and value.
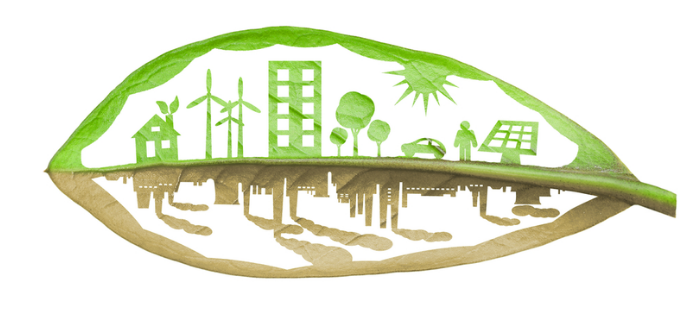
Comments: No Comments
Why Pursue an EHS Management System?
The discipline required to design and implement a compliant environmental, health & safety (EHS) management system can help organizations improve in many areas over and above the tasks, as defined.
- Identify and categorize the organization’s EHS risks. Once this information is known, management will be able to prioritize and then pick and choose how to reduce risks and liabilities to acceptable levels. These risks will be better controlled through strict management accounting. Employees will become more attuned to thinking outside the box to help management improve the overall operation.
- Develop work instructions and/or procedure to guide an employee’s actions and ensure that each EHS task is completed in a disciplined manner approved by management. This will reduce the risk to an organization of an employee accidentally making an environmental, health and/or safety mistake that causes the employee or others to be injured or worse; creates public awareness of the problem; or causes governmental inspections, fines, and loss of business.
- Provide management assurance that the company does, in fact, know and understand the legal and EHS requirements that the business must meet on a daily basis. These legal requirements will drive improvement in having up-to-date procedures and work instructions for employees to follow every day.
- Develop meaningful EHS goals and objectives. These objectives drive improvement in environmental and personal health & safety performance. They may also reduce internal costs by reducing trips to the hospital, payments for workers compensation, and employees on disability. Each business will have different goals that should change each year to ensure continuous improvement over time.
- Develop a strong training program. Well-written procedures and work instructions help define the actions required of employees to meet EPA and OSHA requirements and company directives. A well-trained workforce is a motivated and happy work force. Turnover is reduced, accidents and incidents are reduced, and production efficiencies increase. Employees are very aware when an organization takes time to assure each job requested is completed in the safest and most environmentally sound manner possible.
- Develop appropriate monitoring and measurement of key characteristics and requirements. These key performance indicators are based on regulations and laws intended to guide the organization’s actions in a direction of continuous improvement and compliance.
- Allow employees to audit and verify that the EHS management systems are functioning as designed and implemented. By continuously auditing each OSHA program and environmental function, the organization will discover issues of concern and non-conformances prior to an employee being injured or worse, having an environmental spill or incident, or incurring a governmental agency finding. This allows the company to choose a timeframe that will best help improve the situation without undue influence by outsiders.
- Design a fully functioning corrective/preventive action program to monitor issues of concern and/or non-conformance and the actions used to rectify each situation identified. As employees watch management fix problems, they will learn that management is concerned about continuous improvement and the employees will go back to making improvement suggestions. These suggestions will further drive improvement in areas outside the original EHS management systems.
- Look at the business model and the EHS management systems in a holistic fashion. By using this self-reflection and identifying improvement opportunities, management can direct responsibilities for improvement actions across many departments within the company. Each of these improvement opportunities will again help the bottom line and reduce the possibility of an EHS liability now or in the future.
- Know that you have done everything possible to maintain the business in a manner to meet all OSHA and EPA rules and regulations, as well as association requirements. The organization will have done everything possible to assure that the environment and the health & safety of employees are protected every day the doors are open for business. To a business owner, that knowledge is priceless.