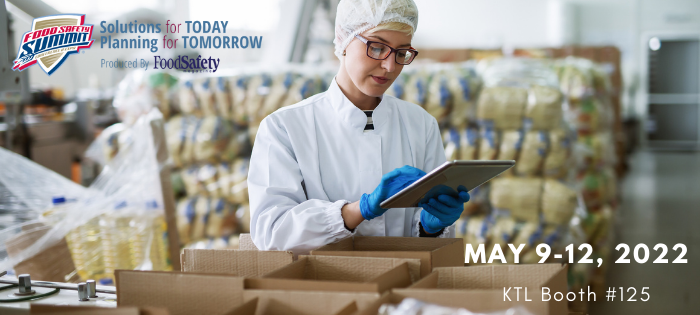
Visit KTL at the 2022 Food Safety Summit
As one of the premier events in the food industry, the Food Safety Summit provides a comprehensive conference and expo for attendees to learn from subject matter experts, exchange ideas, and find solutions to current industry challenges. The Summit is back in person this year, and KTL is excited to be there live!
- When: May 9-12, 2022
- Where: Donald Stephens Convention Center, Rosemont, Illinois
- Who: Retailers, food processors, distributors, food manufacturers, growers, foodservice, testing laboratories, importing/exporting, law firms, and other food safety professionals
- Find KTL: Stop by our booth (#125) in the exhibit hall!
KTL Solutions Stage Presentation
Be sure to also update your agenda to attend KTL’s Solutions Stage presentation on Thursday, May 12 at 1:30 pm. KTL Principal Joe Tell and Partner and Senior Consultant Roberto Bellavia will be highlighting the following case study:
Food Safety Management System Case Study: Using Microsoft 365® to Improve Compliance
Food and beverage companies and their suppliers are subject to a wide range of complex regulatory and certification requirements, often with limited resources to maintain and demonstrate compliance. Finding effective information management tools is critical. Having a simple, centralized FSMS to manage, track, communicate, and report compliance program information can enable staff to complete required tasks, improve compliance performance, and support operational decision-making. The big secret: most companies already have the software they need in-house. KTL will present an industry case study demonstrating a cost-effective approach for building an FSMS using your existing Microsoft 365® platform with SharePoint®.
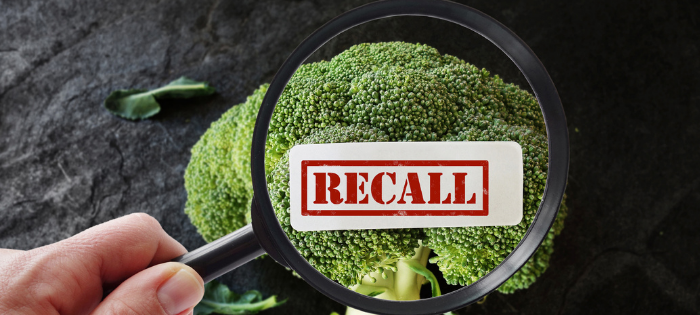
Comments: No Comments
FDA Issues Guidance for Voluntary Recalls
Foodborne illnesses impact millions of Americans every year—ranging from mild cases to hospitalizations to death. Reducing foodborne illness is a focus for the U.S. Food and Drug Administration (FDA), as reflected in several recent actions, including the proposed Food Traceability Rule (published on September 23, 2020) and the 2021 Foodborne Outbreak Response Improvement Plan (FORIP).
FDA recently took another step toward reducing the public’s exposure to the risks of foodborne illness on March 3, 2022, issuing its final guidance for voluntary recalls: Initiation of Voluntary Recalls Under 21 CFR Part 7, Subpart C.
About Voluntary Recalls
A voluntary recall involves actions taken by a company to correct or remove a violative product from the market, either on its own initiative or in response to a recommendation from the FDA. FDA Associate Commissioner of Regulatory Affairs Judith McMeekin, Pharm. D., emphasizes that “voluntary recalls continue to be the fastest, most effective way for a company to correct or remove violative and potentially harmful products from the market to help keep consumers safe.”
FDA’s new guidance outlines the steps companies should take before a recall is mandated, including developing policies and procedures, establishing training, maintaining records, and initiating communications.
BEFORE: Preparation Guidance
FDA’s guidance applies to any products that fall under the agency’s jurisdiction, including any food, drug, or device intended for human or animal use. The guidance breaks down the agency’s recommendations for activities companies (including manufacturers and distributors) should take in advance of a potential recall to be “recall ready.” These include the following:
- Establish a recall communications plan to address communications with employees, FDA, supply chain, direct accounts, and the public, as necessary. Identify key contacts and develop draft templates that can be easily customized and distributed when needed.
- Identify and train appropriate personnel (and alternates) on recall-related responsibilities. The recall team should have a thorough understanding of recall procedures and their respective roles in carrying out a recall plan. Regular training, including mock recalls, help ensure competency.
- Identify any reporting requirements for distributed products, if required by FDA. This might include a report to the Reportable Food Registry, an adverse event report for a dietary supplement, or a report to FDA upon product correction or removal.
- Establish and implement product coding to ensure traceability throughout production and distribution. This will enable more effective lot identification to accurately define and limit the recall scope.
- Maintain distribution records to allow for easier and faster identification of products to be recalled. Distribution records should include contact information for all direct accounts that received the product.
- Establish recall initiation procedures. Prepare, maintain, and document written procedures for initiating a recall to minimize delays and uncertainty when/if a voluntary recall becomes necessary. Procedures should be covered in training and should describe actions to carry out the following:
- Stop distribution, shipment, and/or sales of affected products.
- Outline a recall strategy that considers the scope/depth of the recall and associated risks.
- Notify direct accounts throughout the distribution chain and communicate instructions for appropriate disposition of product.
- Notify the public, when appropriate, if a product presents a health hazard.
DURING: Identifying and Initiating a Potential Recall
Identifying a potential problem is the first step in initiating a potential recall. It is vital that companies ensure timely identification and response to product problems that might lead to a recall. FDA suggests that the following indicators may suggest a potential concern:
- Internal reports of product specification deviation
- Out-of-specification testing results
- Consumer complaints
- Inspectional observations or laboratory results
- Reports of adverse events (e.g., illness, injury, death)
It is then the company’s responsibility to investigate the potential problem to determine 1.) whether a deviation has occurred, and 2.) whether the safety, effectiveness, purity, or potency of distributed products has been affected. A voluntary recall should not be delayed pending results of this investigation. Rather, companies should follow established procedures (see above) to decide whether to initiate a recall, determine the appropriate scope/depth of the recall, and resolve whether to discontinue production or distribution of impacted product(s).
To initiate a voluntary recall, companies should:
- Notify the FDA immediately if the company believes the product to be violative.
- Promptly issue recall communications to affected direct accounts and to the general public, if appropriate.
- Follow the procedures established in the company’s recall plan to implement the recall in accordance with 21 CFR 7.46.
- Provide instructions to the distribution chain regarding disposition of the product.
AFTER: Working with FDA
The FDA is committed to working with companies to help facilitate prompt response (i.e., removal or correction) to violative product that enters the marketplace. The agency has designated recall coordinators organized by product type located throughout the country who can work with company recall teams to develop strategies, review communications, monitor disposition of the product, coordinate with other regulatory bodies, etc.
The FDA may request a company initiate a recall under 21 CFR 7.45 after conducting discussions with the firm if the product presents a risk of illness, injury, or gross consumer deception; the firm has not initiated a voluntary recall; or agency action is required to protect public health.
Reducing Risks
The food industry and supply chains continue to change and evolve at an accelerated pace. That introduces new risks and challenges, including foodborne illness outbreaks. FDA’s most recent guidance is intended to help companies proactively address these risks—reducing response time in a foodborne illness outbreak and, subsequently, the number of people impacted.
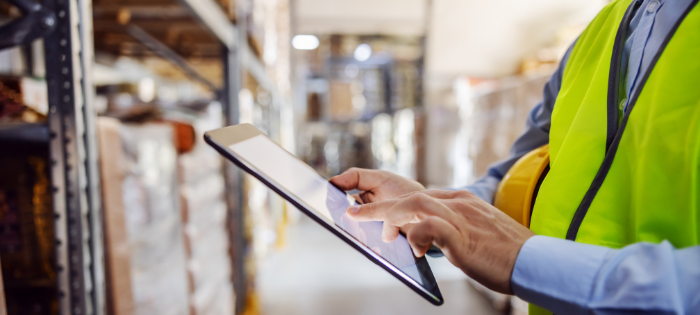
Comments: No Comments
4 Quick Tips as EPA Inspections Continue
For the past several months, KTL has been talking about the significant uptick in U.S. Environmental Protection Agency (EPA) information surveys and multimedia inspections at regulated facilities—on our website, during webinars, at various conferences. Earlier this month, our team was called in to provide on-the-ground support to another manufacturer undergoing a comprehensive, unannounced multimedia inspection.
On the heels of this surprise inspection, one KTL Senior Consultant reiterates, “I can tell you firsthand based on this and other similar inspections over the past few months that inspectors are being very thorough and that the threat of financial penalty is substantial—particularly if your facility is not prepared.”
Take Action Now
KTL has been able to have some candid conversations with the EPA inspectors, and we know they plan to continue these unannounced inspections. EPA will be back in force this spring, and they have targets. It is in your best interest to make sure your facility is ready should an inspector show up on your doorstep.
Based on recent conversations and observations, KTL recommends taking at least the following four actions to prepare your facility:
- Verify your hazardous waste generator status in EPA’s Enforcement and Compliance History Online (ECHO) database and, if you are a small quantity generator (SQG), make sure that you have updated your EPA notification. All SQGs are required to update notification to EPA once every four years beginning September 2021. If you have not done this using the Form 8700-12, you are out of compliance and a likely target for an EPA inspection.
- Check the EPA EnviroFacts database to make sure you have identified emergency contacts for your facility and that the contacts are current. Inspectors are asking to see Emergency Response Plans and are particularly focused on correct contact information, clear conveyance of risk, and understanding of roles and responsibilities (i.e., training).
- Make sure you are appropriately managing your universal waste and hazardous waste. Have you completed a waste characterization for all hazardous waste streams and for solid waste streams that may appear to be hazardous? Are your containers closed, labeled with the nature of the hazard (see 40 CFR 262.16(b)(6)(i)(B), and dated? Are you appropriately managing and labeling any satellite accumulation areas (SAA) and container accumulation areas (CAA)?
- Establish a quick response internal inspection team that can evaluate all areas of risk in your facility to ensure you are in compliance at the time of inspection. Plan to check containers for proper labeling; ensure universal waste containers are closed and labeled properly; and verify that all hazardous waste, universal waste, and used oil management documentation is readily accessible. The inspector will ask to see your documentation.
KTL strongly encourages you to reach out if you have any questions or concerns about a potential EPA inspection. Our team has been through enough of these inspections with various clients recently to have a good handle on what to expect and what should be done to avoid financial penalty.
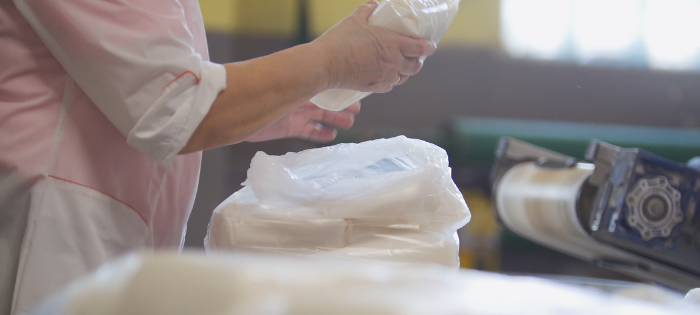
Comments: No Comments
Controlling Combustible Dust: Focus on Food
There is a wide range of agricultural and food products that create fire and explosion risks and hazards, including flour, grain, sugar, spices, cereal, flavoring additives, and many more. Dusts produced in any industry present challenges, but when manufacturing and processing food products, dusts can create the following major threats:
- Airborne dust can cause serious harm to human (employee) health by causing physical ailments ranging from dermatitis to occupational asthma to lung cancer.
- Dust can create the potential for cross contamination and encourage the spread of pathogens and allergens within the food processing plant.
- Dust may become combustible and serve as the source for explosions that harm workers, damage machinery, and destroy buildings/corporate reputation.
About Combustible Dust
The food industry is responsible for the largest percentage of combustible dust incidents in the U.S.—ranging anywhere from 24-43% depending on the timeframe and the source. One of the most notable combustible dust incidents in history involved a secondary explosion at the Imperial Sugar refinery in 2008, which killed 14 people and injured 40.
According to the Occupational Safety and Health Administration’s (OSHA) definition, combustible dust is “a solid material composed of distinct particles or pieces, regardless of size, shape, or chemical composition, which presents a fire or deflagration hazard when suspended in air or some other oxidizing medium over a range of concentrations.”
A dust explosion occurs when all five elements of the Dust Explosion Pentagon are present:

- Ignition source
- Oxygen
- Confined area
- Suspended cloud
- Explosive dust
Combustible Dust Standards
The devastating 2008 sugar refinery explosion prompted the development of OSHA’s Combustible Dust National Emphasis Program (NEP), and yet, some 14 years later, there is still no combustible dust regulation. That doesn’t mean, however, that there are no standards for managing and controlling combustible dust. In fact, there are several agencies involved in ensuring the food industry is appropriately managing the various hazards associated with combustible dust, including:
- National Fire Protection Association (NFPA)
- OSHA
- U.S. Food and Drug Administration (FDA)
NFPA Codes
NFPA sets standards regarding combustible dust. In fact, there are at least ten NFPA standards related to combustible dust (NFPA 61, 68, 69, 77, 484, 499, 652, 655, 664, 654). While these standards and codes are not law, per se, they are enforced by OSHA and referenced extensively. Most insurance agencies and local fire codes state that NFPA standards shall be followed as code.
NFPA’s most recent Standard on the Fundamentals of Combustible Dust (NFPA 652) covers the fundamental requirements for managing combustible dust fires and explosions and is an excellent starting point. NFPA 652 requires owners/operators to:
- Determine the dust’s combustibility and explosibility hazards based on laboratory testing or historical facility data.
- Conduct a Dust Hazard Analysis (DHA) to identify and evaluate potential dust fire and explosion hazards based on Kst (i.e., explosibility) values. Note: The DHA is a relatively new requirement—similar to OSHA’s Process Hazard Analysis as part of the Process Safety Management (PSM) program—used to assess risk and determine the required level of fire and explosion protection from combustible dust.
- Manage all the identified fire, flash fire, and explosion hazards identified in the DHA.
- Establish a written safety management system, including operating procedures and practices, training, incident investigation, and employee participation, to prevent and protect against the hazards.
NFPA 61 – Standard for the Prevention of Fires and Dust Explosions in Agricultural and Food Processing Facilities specifically covers facilities engaged in dry agricultural bulk materials or manufacturing and handling starch.
OSHA National Emphasis Program (NEP)
While OSHA has no formal standard for managing combustible dust, the agency published the Combustible Dust NEP in 2009, which outlines policies and procedures for inspecting workplaces that create or handle combustible dusts. The NEP heavily references the standards published by NFPA. It also references several other OSHA standards, including:
- 1910.22 Housekeeping
- 1910.307 Hazardous Locations
- 1910.1200 Hazard Communication
- 1910.269 Electric Power Generation, Transmission, and Distribution
- 1910.272 Grain Handling Facilities
- General Duty Clause, Section 5(a)(1) of the OSH Act
The General Duty Clause may be the most important of these, as it essentially gives OSHA the right to issue a citation any time employers fail to keep their employees safe from recognized hazards, including those hazards associated with combustible dust. Companies must control dust emissions to protect workers from exposure. If OSHA determines that even a very low Kst (i.e., low explosibility) dust is present in a facility with no explosion protection in place, the agency will issue citations and fines for lack of compliance.
Incidentally, OSHA published the Occupational Exposure to Flavoring Substances – Safety & Health Information Bulletin (SHIB) in 2010, cautioning that volatile organic compounds (VOCs) and respirable dust may be produced when handling many powdered flavoring formulations or spices. Inhalation of these substances may result in exposure directly to the small airways of the lungs.
FDA: Food Safety Modernization Act (FSMA)
In addition to meeting NFPA standards and OSHA guidelines, food companies must meet the requirements of FDA’s Food Safety Modernization Act (FSMA). FSMA requires food processing facilities to implement measures to ensure contamination hazards will be minimized or prevented. This includes developing a Hazard Analysis and Critical Control Points (HACCP) Plan with preventive controls for processes, food allergens, foreign objects, sanitation, and supply chain, as well as complying with Good Manufacturing Practices (GMPs).
Best Practices
Combustible dust itself is not avoidable, but the related consequences are. When it comes down to it, poor housekeeping is the biggest root cause of combustible dust issues. Many risks and hazards can be avoided by effectively cleaning the facility and equipment to remove contaminants before they become widely dispersed. Diligent housekeeping, combined with installing a dust collection system that is properly designed for the operation, can significantly reduce airborne dust and help mitigate a primary or more deadly secondary explosion.
If you work in the food industry, combustible dust is a concern. Make sure you understand the applicability of all the standards and codes, particularly the requirements under the various NFPA standards. The following may be required to keep your facility in compliance and your employees safe:
- Laboratory screening to determine if your powders are combustible or explosible.
- DHA to identify and evaluate potential dust fire, flash fire, and explosion hazards.
- Full analytical testing to determine explosion strength (Kst), minimum ignition energy, maximum safe storage temperature, and more.
- A written management system that documents operating procedures and practices for the ongoing management of dust fire, flash fire, and explosion hazards.
- Initial and ongoing training for operating, engineering, and management staff to build competency and understanding.
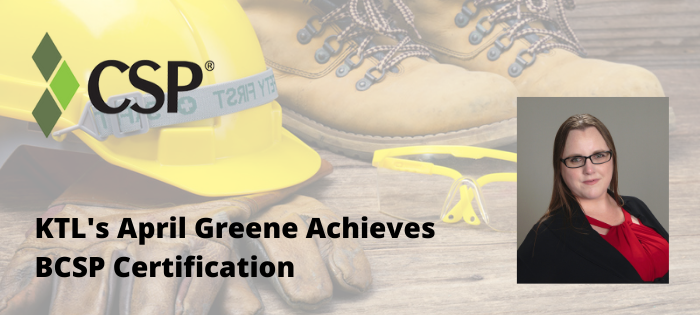
Comments: No Comments
KTL Consultant April Greene Achieves BCSP Certification
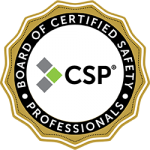
Consultant April Greene has become KTL’s newest Certified Safety Professional (CSP). April has completed all experience and eligibility requirements—including recently passing the rigorous CSP exam—for a Board of Certified Safety Professionals® (BCSP®) certification. The CSP is one of the industry’s most recognized environmental, health, and safety (EHS) certifications.
April is an experienced EHS professional with a 10-year history of working in the EHS services industry and laboratory settings. She has worked with many of KTL’s clients to create and manage EHS programs, plans, policies, and procedures to ensure regulatory compliance and workplace safety. In addition to her BCSP certification, April is a certified ISO 45001 (safety) and 14001 (environment) Lead Auditor and Wisconsin Department of Natural Resources (WDNR) Green Tier Auditor.
Safety issues have become more complex, and today’s safety professional must continually be better qualified. “Safety, health, and environmental practice relies on the knowledge and skills of its practitioners,” explains BCSP’s CEO, Christy Uden, CAE, IOM.
BCSP credential holders are among the most highly trained, educated, and experienced individuals in the safety field. Having achieved a BCSP certification demonstrates April’s proven knowledge of EHS fundamentals, her commitment to worker safety, and the professionalism of her safety practice.
Next up for April: First a new tattoo to commemorate her CSP (think GHS pictograms), and then she’s off to the BCSP Global Learning Summit in May.
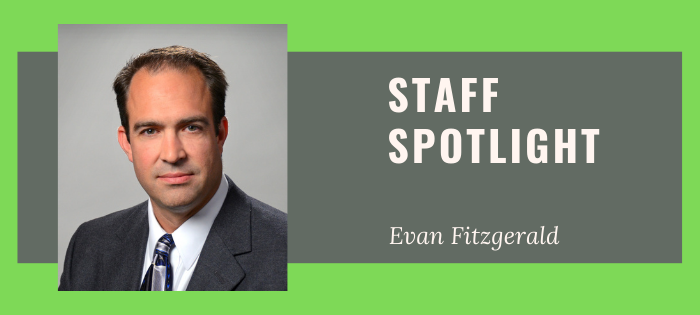
Comments: No Comments
Staff Spotlight on Evan Fitzgerald
Get to know our KTL team! This month, we are catching up with KTL Principal Evan Fitzgerald. Evan leads KTL’s efforts to help clients develop, automate, and improve management and compliance information systems and optimize them to reduce costs and improve performance. He has developed numerous cloud-based applications that KTL uses to deliver compliance efficiency tools to our clients. He is based out of KTL’s Madison, WI headquarters.
Tell us a little bit about your background—what are your areas of expertise?
I earned a degree in mechanical engineering in 1996 and went to work for RMT, an environmental consulting firm, with the plan of being on their process engineering team. I ended up doing mostly construction management, which was not the direction where I saw growth in environmental compliance. When an opportunity with Kestrel Management (now KTL) opened in 1998, I jumped at the chance to make the switch to a firm that viewed environmental compliance from a management and process perspective. That made me employee #1 with the five original owners.
Since then, I’ve done a little bit of everything at KTL—but always with an eye towards technology. That included running our Aerie Technologies business when we created a joint venture to take the dynaQ™ assessment software into the marketplace. It was during that time I first met KTL Principal Joe Tell (formerly of Tellevate LLC) at a trade show focusing on software in environmental management. It was years in the making, but on November 1, 2019, Kestrel Management and Tellevate LLC merged to form KTL.
I now primarily focus on managing the SharePoint/IT side of KTL and have also taken on more business management responsibility as we have transitioned our management team. I have never been as excited and hopeful for the direction of KTL given the staff and clients we have put together.
What types of clients do you work with? What are the biggest issues you see them facing right now?
I work with all types of KTL clients. The biggest issue facing them (from my view of things) is the same thing that’s been facing them for decades—a need to improve processes via the use of technology with little direction and support provided by their internal resources.
People often ask me who our biggest competitor is in the IT sector, and I always say our biggest competitors remain Microsoft Excel and Word. Our clients do not have the time to put to use the tools often already at their disposal, and switching to one of the large platforms is expensive and time-consuming. KTL fills that gap by developing the right level of tool built to our clients’ current operations.
What would you say is a highlight of your job?
The diversity of work and clients that we help at KTL. It’s pretty rare when any two days are the same…and I don’t think after 23 years here that I’ve ever had two weeks the same.
What do you like to do in your free time?
My wife and I have three children that have kept us pretty busy for the past 21 years between theater, sports, and school functions. Our youngest is still in the house and has taken up competitive volleyball, giving us our first taste of the weekend sports tournament grind.
I have been an avid strategy card game and board game player for about 25 years. My big summer trip was attending a massive gaming convention in Indianapolis called GenCon. That’s taken a dip due to COVID. Hopefully, that can get back on track soon. I also participate in an archery and trap shooting league throughout the year.
Read Evan’s full bio.
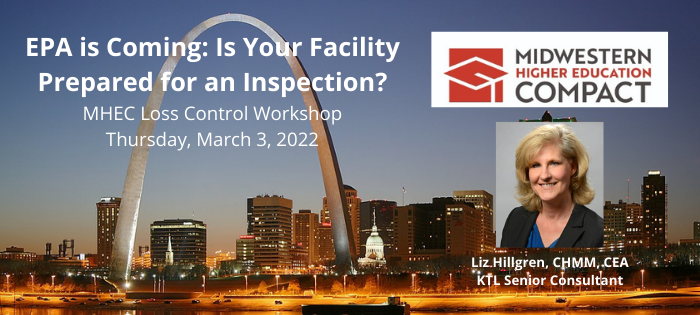
KTL Presentation on EPA Inspections Featured at Loss Control Workshop
KTL is excited to be joining the Midwest Higher Education Compact (MHEC) as a featured presenter at the 24th Annual Loss Control Workshop live and in-person in St. Louis, Missouri. This workshop is open to all interested institutional representatives participating in MHEC’s Master Property Program.
KTL’s presention is part of the workshop’s technical agenda:
EPA Is Coming: Is Your Facility Prepared for an Inspection?
Thursday, March 3, 2022
3:30-4:30 pm CT
In recent months, regulated facilities have experienced an uptick in U.S. EPA information surveys and multimedia inspections. KTL’s Liz Hillgren, CHMM, CEA, will present guidance on steps you can take to prepare for inspections and minmize your risk of compliance findings and enforcment actions.

Comments: No Comments
Food Safety: Top Trends to Watch in 2022
The food system and supply chains continue to change and evolve at an accelerated pace. That introduces new risks and challenges—and heightens some familiar ones. As we move into 2022, the Food and Drug Administration (FDA) continues to strengthen its focus on the four core elements of its New Era of Smarter Food Safety to address several ongoing challenges in food safety. In addition to those identified in FDA’s New Era, KTL’s food safety experts have identified some of the key trends they are tracking in 2022—along with some guidance on how to prepare for the future.
Food Traceability
Food traceability is the ability to track any food through all stages of the supply chain—production, processing, distribution—to ensure food safety and operational efficiency. There is a real need for standardization, stronger linkages throughout the supply chain, improved communication and recordkeeping, and faster response. Notably, one of the core elements of FDA’s New Era is Tech-Enabled Traceability, which involves the use technology to create food traceability advancements. Under this, FDA has taken several actions to reduce foodborne illness:
- The proposed Food Traceability Rule was published on September 23, 2020, as required under the Food Safety Modernization Act (FSMA) Section 204(d), to enhance traceability recordkeeping for certain identified foods beyond a limited “one-up, one-back” traceback approach. The final rule must be submitted by November 7, 2022.
- FDA’s 2021 Foodborne Outbreak Response Improvement Plan sets the stage to “enhance the speed, effectiveness, coordination, and communication of foodborne outbreak investigations” through tech-enabled product traceback, root cause investigations, stronger analysis and dissemination of outbreak data, and operational improvements.
To prepare: Familiarize yourself with FDA’s proposed rule. Review the Food Traceability List (FTL) and start building systems and processes now that address requirements for traceability lot codes, critical tracking events (CTEs), key data elements (KDEs), and recordkeeping.
Food Safety Culture
An organization’s food safety culture is ultimately reflected in the way food safety is managed in the workplace. A strong food safety culture creates an atmosphere where everyone in the organization is aware of and helps to prevent any process and/or operational issues and deviations that may impact the safety and/or quality of their products. Food safety culture is another core element of the FDA’s New Era. It is also a key component of the GFSI Benchmarking Requirements Version 2020 and, subsequently, is being integrated as a requirement into many of the benchmarked food safety certification standards. Best-in-class food safety cultures have robust systems in place to ensure consistent commitment, communication, procedures, training, performance measurement, and trust.
To prepare: The incorporation of food safety should translate to all aspects of the business. Assess current food safety program elements, identify improvements that are internally desirable and required, and implement those updates that will create a strong food safety culture.
Sustainable Food Management
Wasted food makes up the largest percentage—over 20%—of any one material sent to landfills and incinerators each year in the U.S. With more customers and businesses focusing on making sustainable changes, food businesses need to work hard to ensure less food is being wasted. According to the Environmental Protection Agency (EPA), sustainable management of food is “a systematic approach that seeks to reduce wasted food and its associated impacts over the entire lifecycle, starting with the use of natural resources, manufacturing, sales, and consumption, and ending with decisions on recovery of final disposal.” The EPA, U.S. Department of Agriculture (USDA), and FDA joined forces to address the magnitude of wasted food impacts across the U.S. through the U.S. Food Loss and Waste 2030 Champion program. Efforts to promote sustainable food management have also extended to the state level.
To prepare: A thorough food and packaging assessment can help identify appropriate strategies to avoid waste, cut down on disposal costs, reduce over-purchasing and labor costs, reduce water and energy use associated with food production, and reduce GHG emissions. Based on the outcomes of the food waste assessment, there are some common strategies for reducing wasted food and packaging.
Health & Safety and Environmental Focus
During the pandemic, businesses had to find new ways of working to ensure health and safety. Employee protection will remain a top priority, particularly with potential increases in Occupational Safety and Health Administration (OSHA) funding to make improvements in workplace safety protection for American workers, as well as significant increases in OSHA’s maximum penalties. In addition, 2021 brought a significant uptick in EPA multi-media inspections, enforcement actions, and large penalties for violations, particularly related to anhydrous ammonia storage, risk management, and chemical accident prevention planning. Anhydrous ammonia is widely used as refrigerant in food facilities, including meat, poultry, and fish processing facilities; dairy and ice cream plants; wineries and breweries; fruit juice, vegetable juice, and soft drink processing facilities; cold storage warehouses; other food processing facilities; and seafood processing facilities aboard ships.
To prepare: Make sure you have the processes, programs, and systems in place—and documented—to ensure you are always protecting employees’ safety and health and meeting OSH Act requirements. If your facility uses anhydrous ammonia, you must understand the hazards posed by chemicals at the facility and design and maintain a safe facility to prevent accidental releases.
Compliance Efficiency Tools
Managing the complexities of a management system is challenging. That is because every regulatory agency (e.g., FDA, USDA, OSHA, EPA) and voluntary certification (e.g., GFSI-benchmarked standards, gluten-free, organic, ISO) calls for companies to fulfill compliance requirements—many of which overlap. Supply chain and internal requirements can create further complications and confusion. And more frequently than not, companies may not understand or have the resources to manage everything that needs to be in place to satisfy requirements. This is an area where compliance efficiency and tracking tools are becoming essential to allow companies to do more with fewer resources.
To prepare: An integrated compliance management system (CMS) is intended to bring various tools together to create one system that effectively manages compliance requirements, enables staff to carry out daily tasks and manage operations, and supports operational decision making by tracking and trending data that is collected daily by the team charged with implementation.
Food Fraud
In May 2016, FDA issued its final rule on Mitigation Strategies to Protect Food Against Intentional Adulteration (IA). While this is not a new rule, supplier approval/verification programs, vulnerability assessments, and written food defense plans will remain a key focus as a surge in food demand and lack of supply has created an environment ripe for food fraud. It is likely that FDA IA inspections could also ramp up, especially when more onsite inspections resume.
To prepare: Develop a food defense plan. This should include conducting a vulnerability assessment and developing the required programs to remove the risks of IA and food fraud.
Others to Watch…
- Food Irradiation. Food irradiation is a food safety technique used to kill pathogens, including bacteria, viruses, and parasites, and extend shelf life. Irradiation provides excellent safe food processing. FDA continues to research and approve irradiation for a variety of foods. Despite consumer resistance, expect this trend to continue.
- Food Investments. We are seeing more and more private equity firms investing in food companies and, subsequently, in their food safety infrastructure. Food safety is a critical factor in these acquisitions. Expect a thorough assessment of the condition of operations (i.e., personnel, equipment, processes, plant); level of food safety compliance/certification status; and any other potential risks that would impact the transaction.
- Cannabis. The regulatory framework for managing cannabis production is still murky. However, this is a rapidly growing market, and we anticipate progress—whether at the state level or federal level—in the development and implementation of regulations and controls (e.g., Good Manufacturing Practices (GMPs), labeling requirements, etc.).
- Labeling. COVID significantly increased the number of new food preparation and delivery/takeout services and ready-to-eat (RTE) food products. These new business models heighten the importance of appropriate labeling, particularly regarding allergens and instructions for safe food production.
Set Your Goals for 2022
As FDA continues to push its New Era of Food Safety forward and new challenges surface, it is important to understand the current landscape, set priorities, and commit the appropriate resources to ensure long-term sustainability. Consider undertaking the following activities:
- Implement a CMS to help coordinate, organize, control, analyze, and visualize the information necessary to remain in compliance and operate efficiently.
- Conduct third-party assessments to provide an outside perspective of food safety systems and compliance/certification to identify gaps in programs that need development/updates.
- Explore technological advancements that allow for further digitization and promote more timely and accurate collection and management of important data.
- Conduct root cause analysis, as needed, to identify underlying issues and ensure similar problems do not occur in the future.
- Build a strong food safety culture that focuses on changing from a reactionary to a preventive mindset that promotes safety and quality.
If you would like help evaluating your current food safety risk level and assessing your priorities for 2022, please contact KTL.
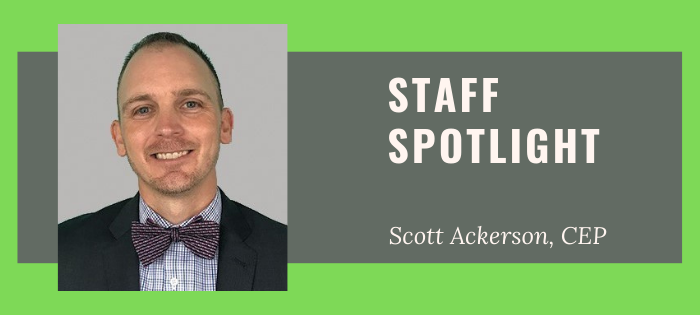
Comments: No Comments
Staff Spotlight on Scott Ackerson, CEP
Get to know our KTL team! This month, we are catching up with KTL Senior Consultant Scott Ackerson. Scott is a Certified Environmental Professional (CEP) with technical expertise in international environmental compliance and environmental system design and nearly 20 years of professional experience in managerial and strategic leadership supporting governments, private industry, and NGOs. He is based out of Arlington, Virginia.
Tell us a little bit about your background—what are your areas of expertise?
During my career, I’ve worked with Peace Corps in Morocco and United States Agency for International Development (USAID), Centers for Disease Control and Prevention (CDC), and Global Fund as an Implementing Partner. In addition, I’ve lived and worked in over 17 countries working with various Ministries of Health to provide technical assistance in areas such as developing health care waste management (HCWM) strategies/framework and environmental systems for donor counterparts to strengthen environmental compliance in areas including general hygiene; waste management (non-hazardous and hazardous); health and safety; water, sanitation, and hygiene (WASH); and HIV/AIDS prevention.
Some highlights over my career before joining KTL include the following:
- While working on the USAID-funded Supply Chain Management System (SCMS) project, I developed and successfully implemented large-scale organizational initiatives that have played integral roles in achieving the organization’s mission.
- I was assigned to support the Liberia Ministry of Health to establish a waste management strategy plan to dispose of unusable pharmaceutical waste in the supply chain. The assignment took about three months to successfully develop a waste management strategy plan that was used to properly collect and dispose of around 700,00 tons of unusable pharmaceutical waste.
- In 2013, I led a team of three international technical experts to develop a HCWM system for the U.S. President’s Emergency Plan for AIDS Relief (PEPFAR)-supported Voluntary Medical Male Circumcision (VMMC) campaign in the Kingdom of Eswatini. The country required a proactive solution for the safe handling and disposal of more than 30,000 kg (66,000 lbs) of health care risk waste generated during its one-year lifespan. In collaboration with the Environmental Health Department within the Ministry of Health, the World Bank, and other relevant partners, the team was able to develop a sound policy that defines clear objectives, activities, roles and responsibilities, timelines, infrastructure, and control requirements for the execution of a new and improved national HCWM system. In addition, the team developed a VMMC HCWM toolkit for the safe and proper disposal of male circumcision hazardous waste.
What types of clients do you work with? What are the biggest issues you see them facing right now?
I’m currently part of an incredible KTL Environmental Compliance Support (ECOS) team that provides consulting services as part of the USAID ECOS contract. The ECOS contract provides USAID staff and Implementing Partners worldwide with technical, educational, and knowledge management assistance to facilitate compliance with 22 CFR 216, Foreign Assistance Act (FAA) Sections 117/118/119, regulatory requirements, and Executive Order and policy objectives.
In addition, the KTL ECOS team offers the USAID’s Bureau Environmental Officer (BEO) of Global Health (GH) and other BEOs a consistent, quality approach to environmental compliance to minimize duplication of systems and effort, facilitate the sharing of lessons learned, reduce compliance risks, and other related services.
The most significant issue facing USAID’s BEO, much like many organizations in the public and private sector, is the lack of funding to ensure staff and Implementing Partners have the tools and knowledge to implement environmentally sound projects.
What would you say is a highlight of your job?
I enjoy interacting with the KTL ECOS team to solve complex problems, while providing trainable moments for USAID staff and Implementing Partners.
What do you like to do in your free time?
I like traveling to places, learning about new cultures, and enjoying the food. Of course, I also enjoy the fine arts (i.e., symphony, musicals, and museums). But most of all, I enjoy life’s simple things with my partner, friends, and family, no matter the occasion.
Read Scott’s full bio.
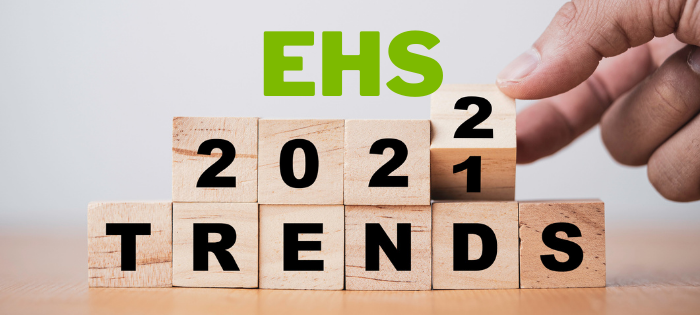
EHS: Top Trends to Watch in 2022
As we’ve seen businesses manage their way through the pandemic over the past two years and a new Administration take hold in office, a number of environmental, health, and safety (EHS) trends are rising to the surface. Some of these may sound familiar, as certain challenges and opportunities in EHS remain ongoing. Some are just gaining traction as we move into the new year.
Here are the top EHS trends KTL’s EHS professionals are keeping watch on in 2022—and some advice on what you can do to prepare…
OSHA Enforcement: Happy 50th Birthday OSHA!
The Build Back Better Act (BBBA) introduced the first amendment to the Occupational Safety and Health (OSH) Act in nearly 20 years. This would include increased funding to make significant improvements in workplace safety protection for American workers, as well as significant increases in the Occupational Safety and Health Administration’s (OSHA) maximum penalties. While the future of the BBBA is uncertain, it provides a good picture of where OSHA is headed by enacting high enough penalties to significantly impact businesses that violate the law and injure or kill workers. While OSHA doesn’t have the resources to audit or fine everyone, the agency will likely make an example of a few major violators to deter others from non-compliance.
To prepare: Make sure you have the processes, programs, and systems in place—and documented—to ensure you are always protecting employees’ safety and health and meeting OSH Act requirements.
EPA Inspections and Enforcement: Focus on Ammonia Refrigeration
With the new Administration, 2021 brought a significant uptick in Environmental Protection Agency (EPA) multi-media inspections, enforcement actions, and large penalties for violations, particularly related to anhydrous ammonia storage, risk management, and chemical accident prevention planning. Many of these violations have been uncovered as part of a National Compliance Initiative (NCI), which is working to enforce the regulatory aspects of the Clean Air Act’s (CAA) Chemical Accident Prevention Program, including Risk Management Plan (RMP) regulations (40 CFR Part 68), General Duty Clause (GDC) (CAA Section 112(r)), Emergency Planning and Community Right-to-Know Act (EPCRA) (CAA Section 312), Process Safety Management (PSM) regulations (29 CFR 1910.119).
To prepare: If your facility uses anhydrous ammonia and you have not conducted a hazard analysis, you are at significant risk of incurring enforcement actions of fines. It is important you invest the time and resources required to:
- Understand the hazards posed by chemicals at the facility.
- Assess the impacts of a potential release.
- Design and maintain a safe facility to prevent accidental releases.
- Coordinate with local emergency responders.
- Minimize the consequences of accidental releases that do occur.
PFAS/PFOA Contamination
Because of per- and polyfluoroalkyl substances’ (PFAS) persistence in the environment and widespread use in firefighting foams and products that resist grease, water, and oil, PFAS contamination is an extremely complicated issue—and concern is mounting over its impacts and how to regulate these chemicals going forward. On October 18, 2021, EPA Administrator Michael Regan announced EPA’s comprehensive Strategic Roadmap to tackle PFAS contamination through increasing investments in research, leveraging authorities to act now to restrict PFAS chemicals from being released, and accelerating cleanup of PFAS contamination. More and more facilities are going to be directly impacted by mitigation efforts and future regulatory action.
To prepare: Proper usage strategies, a comprehensive environmental management system (EMS), and a forward-thinking Emergency Response Plan will remain vital tools for companies potentially dealing with PFAS to effectively manage the associated risks.
Resource Constraints and Compliance Efficiency Tools
There are a few trends we see time and again, which generally can be tied back to many EHS “departments” (which often consist of just one person) lacking the resources—financial and personnel—to manage the sheer number of EHS requirements they are required to comply with. Frequently, companies may not understand or have the resources to manage everything that needs to be in place to satisfy compliance requirements. This is an area where EHS compliance efficiency and tracking tools are becoming essential to allow companies to do more with fewer resources.
To prepare: A compliance management system (CMS) brings information technology (IT) and management systems together to coordinate, organize, control, analyze, and visualize information in such a way that helps organizations remain in compliance and operate efficiently. A CMS can help provide operational flexibility, generate business improvement, and prepare organizations to address these and other EHS compliance challenges that will continue to surface.
Hazardous Waste Incineration Backlog
The changing hazardous waste market continues to create a fair amount of uncertainty regarding whether hazardous waste management capacity can actually meet demand. Many Large Quantity Generators (LQGs) and Small Quantity Generators (SQGs) are still experiencing a hazardous waste incineration slowdown, and most of the permitted transport, storage, and disposal facilities (TSDFs) are backlogged. EPA predicts that this backlog may not fully resolve until the end of the first quarter of 2022. EPA has offered multiple existing regulatory options for various regulated entities that generate and manage hazardous waste as temporary solutions to address the backlog.
To prepare: If you are in the situation where you are coming up against your time limits, contact your EPA Regional Administrator and ask for guidance on how to manage the situation. Keep very careful and accurate records of all hazardous waste information to demonstrate appropriate management.
Environmental Justice and Citizen Science
On January 27, 2021, President Biden issued Executive Order (EO) 14008 – Tackling the Climate Crisis at Home and Abroad, amending EO 12898, which directed federal agencies to develop environmental justice (EJ) strategies to help federal agencies address disproportionately high and adverse human health or environmental effects of their programs on minority and low-income populations. EO 14008 further directs Federal agency actions to support making EJ part of its mission by identifying and addressing the effects of all programs, policies, and activities on minority and low-income populations. As part of EPA’s EJ efforts, the Agency is charting a new pathway for the use of citizen science. Citizen science engages the public in identifying research questions, collecting and analyzing data, interpreting results, and developing technologies and applications to resolve environmental problems. Citizen science provides a resource in times of restricted budgets and to address dispersed or hyperlocal environmental issues.
To prepare: Equipment loan programs are available for anyone who would like to participate. KTL is aware of clients receiving money from the state to make equipment updates. In addition there are a number of EJ grants, funding, and other technical assistance available.
Sustainability
As developing nations continue to industrialize and increase their material consumption, resource demands and pressures on our supply chains will only increase. The Biden Administration has committed to a net zero economy by 2050, and the number of net zero commitments from local governments and businesses continues to grow and push further down the supply chain. There are more incentives for businesses to find clean/renewable energy solutions and to manage waste more sustainably. As one example, Sustainable Material Management (SMM) considers the entire of a product and/or process to help create a circular economy.
To prepare: Consider the following sustainability activities as part of your company’s business strategy:
- Conduct a lifecycle analysis (LCA) to identify and quantify the inputs and outputs in a process and use data to assess the potential environmental impacts across the lifecycle.
- Check with your local utility to have an energy audit completed of your facilities.
- Get input from employees on what initiatives are important to them by enacting a sustainability committee or adding sustainability to your EHS agenda.
Set Your Goals for 2022
With these trends toward more regulations, more enforcement, and more focus on sustainability, EHS management needs to play a more integral role in company strategy. Companies must take the time to be informed, be prepared, and be proactive. Establish company-wide EHS priorities and goals and commit the appropriate resources to ensure the required programs and systems are in place for 2022 and beyond.
If you would like help evaluating your current EHS risk level and assessing your priorities for 2022, please contact KTL.