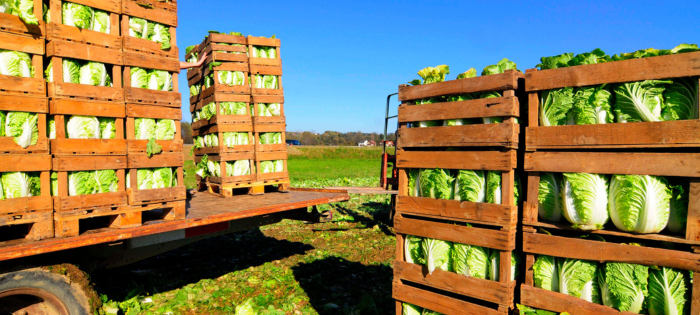
Comments: No Comments
Traceability Rule Compliance Date Extension
Traceability has been a hot issue for most food companies since the Food and Drug Administration (FDA) passed the final Food Traceability Rule in November 2022, especially with the original January 2026 compliance deadline approaching. However, food companies will likely have extra time to prepare, as the FDA announced on March 20, 2025 its intention to extend the compliance date for the Food Traceability Rule by 30 months.
Additional Time
KTL originally reported in our Top Food Trends for 2025 article of speculation that this deadline could be delayed due to a provision in the current draft House appropriations bill that would prohibit funding for implementation, administration, or enforcement of these regulations. According to FDA, “The compliance date extension affords covered entities the additional time necessary to ensure complete coordination across the supply chain in order to fully implement the final rule’s requirements—ultimately providing FDA and consumers with greater transparency and food safety.”
The FDA is planning to follow appropriate procedures and publish a proposed rule to extend the compliance date at a later time to be determined. The Agency remains committed to implementing the full requirements of the final rule but giving industry additional time to comply and itself time to provide additional technical assistance, tools, and other resources to assist industry.
Stay the Course
Regardless of the compliance deadline, organizations should continue working on their traceability systems and programs. This includes performing traceability exercises to help identify gaps, testing protocols and verifying effectiveness, implementing corrective actions, and ensuring adequate traceability processes are in place. Investing in a good technology solution that integrates with the food safety management system (FSMS) will help to further streamline the process.
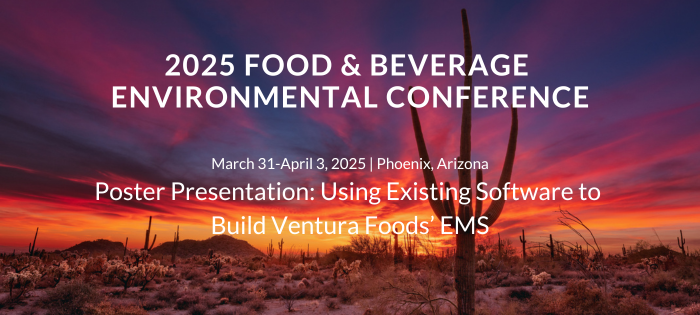
KTL to Present at the Food + Beverage Environmental Conference
The Food + Beverage Environmental Conference (FBEC) is the premier and most comprehensive environmental event for the food and beverage industry in the U.S., focusing on the latest trends and innovations affecting sustainability, water resource management, supply chain, air quality, environmental compliance, and much more.
When: March 31 – April 3, 2025
Where: Rennaissance Downtown Phoenix
Who: Environmental professionasl in any business related to the food and beverage industry
Poster Presentation
Be sure to stop by and see the KTL and Ventura Foods poster at the Poster Session & Social Hour on Thursday, April 3 at 5:00 pm: Using Existing Software to Build the Ventura Foods EMS. We will talking about how Ventura Foods built and implemented an ISO 14001 EMS to meet customer requirements with limited resources.
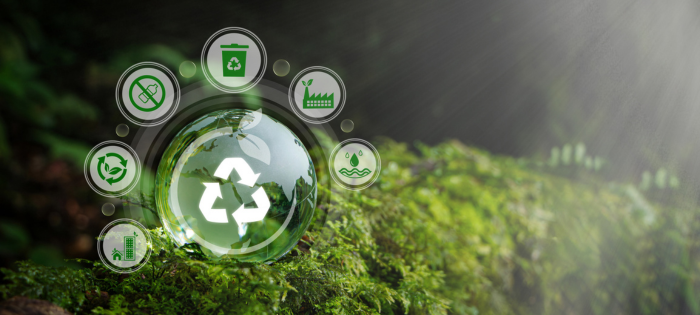
Comments: No Comments
5 Tips to Become a Recycling Superstar
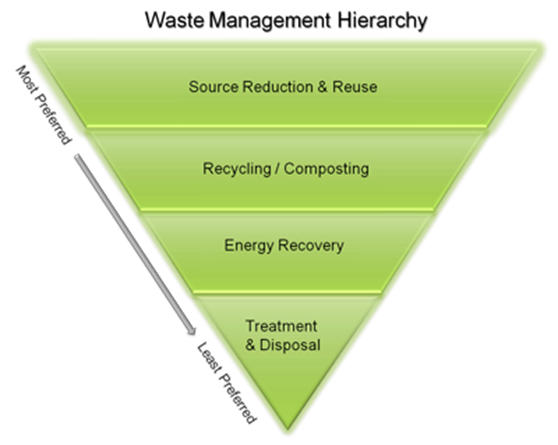
No single waste management strategy is suitable for managing all waste streams in all situations (Environmental Protection Agency (EPA)). As such, EPA’s non-hazardous materials and waste management hierarchy ranks the various waste management strategies from most to least environmentally preferred. Not surprisingly, the hierarchy emphasizes reducing and reusing—followed by recycling—as best practices for sustainable materials management, when possible.
While the best way to reduce waste is to never create it, recycling is a valuable way to collect used, reused, or unused items that would otherwise be considered waste and turn them into something valuable. From Fortune 500 companies to local businesses, to the restaurant on the corner—all have materials that can and should be recycled. The five tips below offer best practices for effectively managing your recycling efforts.
1. Conduct a trash audit.
A trash audit is a process in which an organization systematically analyzes and evaluates the contents of its waste, typically by sorting through the trash to identify the types and quantities of materials being discarded. This in-depth process provides a good baseline in developing a Recycling Program, as it helps to document the contents and quantity of your waste streams and then allows you to define how that waste gets managed.The audit helps to answer questions such as: What are you throwing away? How much is wasted food? Can you separate that out and send it to a composter? Can you stop making that trash? Can you reuse something? Can you sell it to someone else? Can you recycle it?
While not all trash can be reused or repurposed, it is consistent with EPA’s hierarchy to identify the materials produced that can be reused or repurposed as the first and most sustainable waste management solution (e.g., some tools can be sent back to the manufacturer to be refurbished and resold, or there may also be a “second life” outlet for materials). If materials are not able to be reused, the next best consideration is recycling.
2. Understand state and local regulations.
Once your trash audit identifies what items you want to recycle, it is important to consider the regulations. Different states and local governments may have specific requirements for the materials you want to recycle. For example, many states have compliance requirements for electronic wastes, used oil, or other universal wastes. In addition, EPA has very specific requirements for solid and hazardous waste recycling to ensure it is managed properly to avoid environmental and safety hazards. Engage experts, where necessary, if you have questions about certain materials that may have very specific or unclear requirements.
3. Implement a Recycling Program.
Based on the trash audit and regulatory requirements, a Recycling Program can be developed to serve as the roadmap for what gets recycled and how. The Recycling Program should clearly:
- Define what materials get recycled.
- Discuss proper disposal of materials, focusing on the most common items employees would handle in their day-to-day tasks.
- Identify collection points, so employees understand where to put items for recycling.
- Detail storage procedures for recyclable materials.
- Outline roles and responsibilities, including the parties responsible for recycling (see below).
- Provide for worker training to ensure the program is followed as intended.
- Reinforce the purpose of recycling and leadership’s commitment to the cause.
- Address how the program will be communicated to visitors, contractors, customers, shareholders, etc.
4. Partner with the right recyclers.
An important part of your Recycling Program is finding reputable recyclers who understand recycling regulations and are certified to handle the materials you are generating. This means working with recyclers who are transparent. Recyclers who are open about their practices are less likely to mishandle your recyclables than shady operators who could end up getting your company in a lot of trouble. Your recycler should help you identify the best ways to recycle your materials (e.g., setting up separate dumpsters for paper, plastic, food) and identify whether there are any cash-back opportunities for recycling certain materials (e.g., cardboard, scrap metal, electronic waste, etc.).
5. Maintain safe storage and handling practices.
As noted above, a trash audit will help you know what you are recycling. You also need to know how to properly store these materials while they are waiting to be recycled so they do not become a bigger hazard. For example, keep batteries for recycling in cool, dry places away from heat.
Conduct a proper risk assessment for the proposed storage spaces to capture and mitigate potential risks before finalizing your choice, document this in your Recycling Program, and then train employees on how to safely handle the material they are bringing to the recycling area. Precautions may include having the proper fire detection and suppression equipment for the area where you are storing material for recycling, or ensuring employees have the proper personal protective equipment (PPE) to wear when handling materials.
Creating a Recycling Culture
The above five tips can help ensure you have the systems, practices, programs, and partners in place to manage your trash and recycling. By following them, organizations can streamline their waste management processes, comply with environmental standards, and promote resource conservation and cost savings. But to truly become a “recycling superstar”, it is also important that you:
- Avoid all or nothing thinking—set realistic goals for what you can accomplish while still complying with regulations.
- Implement robust quality control processes to avoid making mistakes.
- Think creatively about how your team can work together reduce, reuse, repurpose and recycle your trash and get closer to zero waste.
- Measure your results. Conduct your trash audits annually to assess what is working and what is not and then set new goals to continually improve.
Effective waste management and recycling are essential for organizations striving to operate sustainably and reduce their environmental impacts. Ultimately, fostering a culture of creativity, continuous improvement, and accountability will lead organizations closer to their zero-waste goals, benefiting the environment and the bottom line.
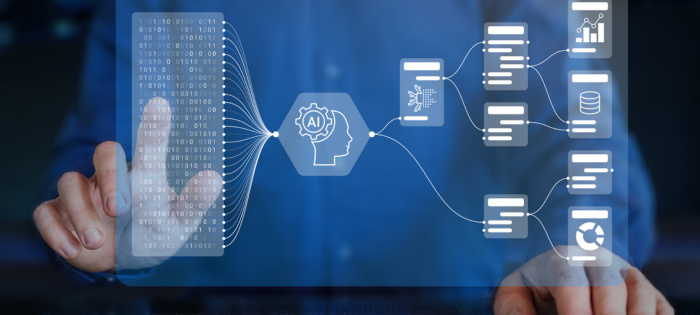
Tech Corner: Power Automate Tasks
Functionality: What does it do?
As part of Microsoft’s Power Platform®, Power Automate® is a workflow automation tool used to automate repetitive tasks and workflows. The purpose of workflow automation tools is to streamline manual processes and tasks in order to maximize company time and resources, increase operational efficiency, and improve overall business productivity.
Common Power Automate tasks include the following:
- Notifications: This can be as simple as creating a notification when something is submitted or changed or setting alerts to act according to a designated schedule (e.g., seven days before due date).
- Approvals: Documents and list items can be routed to specific individuals by email with a simple button to approve or decline and then automatically move along to the next step in the process.
- Document Management: Email attachments can be automatically added to OneDrive® or SharePoint; metadata (e.g., time/date, sender, and email body) can also be added.
- Form Processing: Form processing can automatically create ID numbers for list items to help with tracking. In addition, data from one form can be used to populate multiple lists. For example, entering data into a customer feedback form includes a checkbox asking if it requires a corrective and preventive action (CAPA). If so, relevant data from the feedback form populates a new entry in the CAPA list.
- Records Management: When a record is created, the retention period can be added. When the retention period expires, the record is then automatically archived or deleted.
- Calendar Management: With calendar management, you can do things like email yourself a list of your calendar entries daily or weekly, email reminders for any calendar entries you have not yet responded to, and create Outlook events or meetings from a Power App® button.
- Data Management: Large data sets can be transferred easily from Microsoft Excel® to SharePoint. Data can also be manipulated, cleaned, or transformed during or after the transfer.
Benefits: Why do you need it?
- Fewer mistakes. Replacing manual data entry with automation reduces opportunities for human error and the potential mistakes, inaccuracies, and costs that can accompany it.
- Streamlined processes. Workflow automation creates more efficiency by automatically making assignments and moving projects/documents/tasks along in the process. It is also easier to track and manage processes and performance when all steps are in Power Automate.
- Improved productivity. Automating manual tasks frees up time and resources to focus attention elsewhere. Being able to easily track a project or process through an automated system can further improve productivity and ensure tasks are completed as planned.
- Enhanced collaboration and accountability. A clearly designed workflow helps ensure all employees understand the process and their role in it. A common system further enables cross-functional collaboration and improves accountability.
- Informed business decisions. Power Automate offers real-time reporting and performance metrics that can be used to inform decisions and modify processes to enhance performance.
Technology Used
Microsoft Power Automate
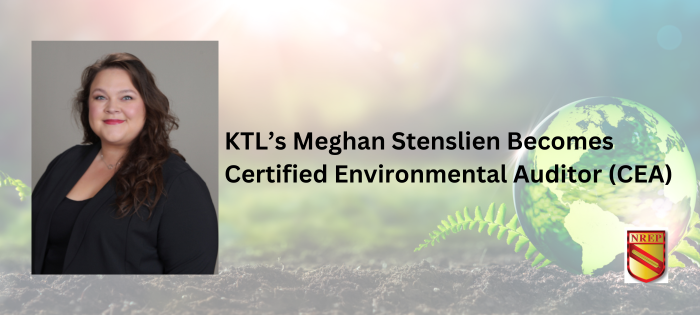
Comments: No Comments
KTL Consultant Meghan Stenslien Becomes CEA
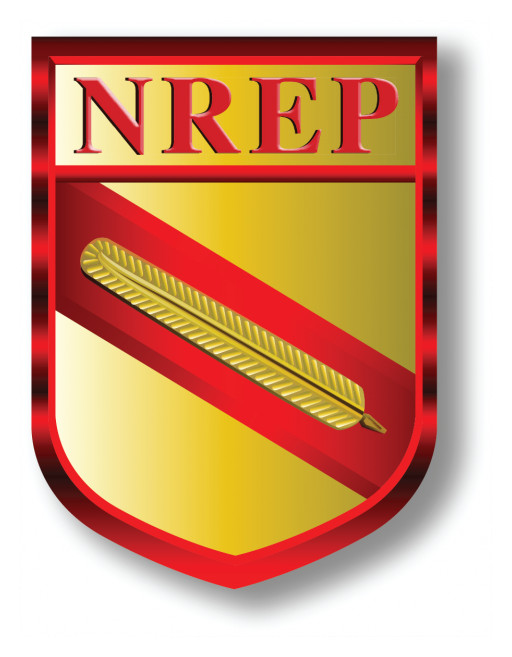
Consultant Meghan Stenslien has become KTL’s newest Certified Environmental Auditor (CEA). Meghan has completed all experience and eligibility requirements—including recently passing the rigorous National Registry of Environmental Professionals (NREP) CEA exam. The CEA certification is a specialty certification program intended for professionals conducting environmental compliance and risk audits of operating facilities, related equipment and ongoing procedures.
Meghan is a Consultant with a diverse background in food safety; quality; and environmental, health, and safety (EHS) compliance. She has conducted routine environmental, safety, quality, and food safety environmental audits and facility assessments and designed programs, policies, and procedures to effectively manage requirements to help ensure regulatory compliance. In addition to her CEA certification, Meghan is a certified ISO 45001 (safety) and 14001 (environment) Lead Auditor, Wisconsin Department of Natural Resources (WDNR) Green Tier Auditor, R2 certified Lead Auditor, and HACCP certified.
NREP is widely considered to be the foremost not-for-profit organization in the environmental and safety industry. Earning a CEA certification demonstrates the highest level of knowledge, experience, and education in the environmental field.
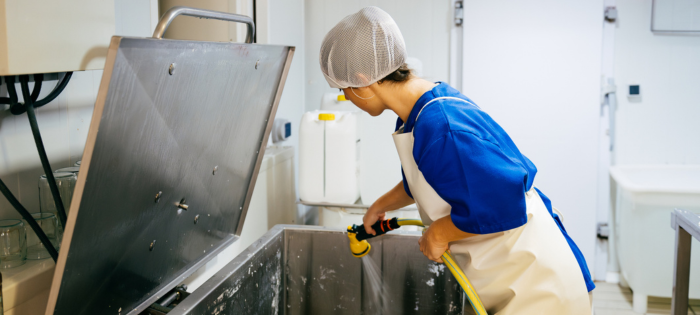
Comments: No Comments
Preventing Foodborne Illness and Avoiding Recalls
The U.S. experienced several high-profile food recalls in 2024 that have caused illnesses and deaths—and heightened public awareness and unease. The emergence of new bacterial and viral strains and the evolution of pathogens that are becoming resistant to traditional food safety measures are growing concerns when it comes to preventing foodborne illnesses. According to the U.S. Public Interest Research Group’s Food for Thought 2025 Report, hospitalizations and deaths from contaminated food doubled in 2024, and recalls from Listeria, E. coli, and Salmonella increased by 41%.
Regulatory Focus on Microbiological Safety
The Food and Drug Administration’s (FDA) new unified Human Foods Program outlines a number of strategies focused on microbiological food safety that are intended to prevent and mitigate foodborne illnesses. In January 2025, FDA also released the draft Establishing Sanitation Programs for Low-Moisture Ready-to-Eat (LMRTE) Human Foods and Taking Corrective Actions Following a Pathogen Contamination Event: Guidance for Industry to help manufacturers of LMRTE human foods comply with 21 CFR part 117 and establish routine sanitation programs that can prevent pathogen contamination events.
FDA’s LMRTE Guidance specifically discusses the importance of establishing and implementing a detailed Sanitation Program and routine environmental monitoring to help prevent pathogen contamination events.
Sanitation and Good Manufacturing Practices (GMPs)
Having a properly implemented Sanitation Program and adequate GMPs provides the essential foundation for preventing pathogen harborage and product contamination events.
GMPs are intended to reduce cross-contamination by defining hygienic personnel practices, controlling traffic and product flow, ensuring proper equipment design and maintenance, and ensuring sanitary building conditions. To be effective, GMPs must be developed based on the company’s specific operations and must be implemented consistently to minimize the risk of contamination and foodborne illness.
Correspondingly, Sanitation Programs include written procedures outlining how cleaning and sanitizing tasks should be done, including the frequency and methods for cleaning surfaces, equipment, and utensils. Sanitation Programs should be regularly monitored, which might include visual checks/inspections for cleanliness. Lastly, Sanitation Programs need to be verified for effectiveness, which brings in environmental monitoring.
Environmental Monitoring
From a consumer protection perspective, environmental monitoring is intended to protect consumers by keeping harmful pathogens from contaminating the food we eat. An Environmental Monitoring Program (EMP) refers to an entire program that focuses on identifying, monitoring, and mitigating environmental risks, particularly pathogens—and foodborne illness—that may compromise food safety. EMPs involve systematic sampling and testing of the production environment for pathogens, spoilage and indicator organisms, and allergens to verify that the Sanitation Program and associated controls are working as intended to prevent foodborne illness.
Environmental monitoring is typically done by swabbing various surfaces in a designated bio-zone for pathogens and sending those samples to an accredited lab for analysis. This monitoring helps to:
- Assess how effective the plant’s cleaning, sanitation, and cross-contamination processes are.
- Determine whether there are any pathogen harborage points in the facility so it can respond accordingly (e.g., adjusting cleaning procedures, addressing equipment or facility issues, etc.).
Ultimately, the purpose of an effective EMP is to help a facility identify and implement strategies to eliminate pathogens and prevent their recurrence. It can help serve as an early warning system for identifying a potential contaminant before it spreads throughout the facility and into food that reaches the consumer. Analyzing EMP data collected over time for trends is particularly effective in continuously improving sanitary conditions.
To-Do Today
There are a number of key actions food processors can undertake today to prevent environmental pathogens from contaminating their facilities and food products:
- Apply GMPs. GMPs apply to EMPs, as with every other aspect of a strong Food Safety Program. GMPs that will impact environmental monitoring results include employee hygiene practices, cross-contamination controls, sanitary facility and equipment design, and cleaning and sanitation processes.
- Evaluate, implement, and verify preventive controls. Identify your greatest risks for environmental pathogens and proactively develop strategies to implement controls in your process flow. These may include controlling pedestrian walkways to avoid personnel contamination; using dedicated tools, equipment, and/or staff post-process; having special uniforms for staff, etc. Just as important, you must verify the performance of your preventive controls through environmental monitoring and take corrective action immediately if problems arise.
- Ensure employees and other resources are qualified. Employees responsible for sanitation, sampling, and overseeing the EMP must have the necessary training and/or experience for assigned duties. In addition, any outside labs used for environmental testing must be accredited under ISO 17025.
- Regularly review and update the Sanitation Program, GMPs, and the EMP. Products, operations, equipment, employees, processes, and other environmental factors change—and all of these can impact the Sanitation Program, GMPs, and the EMP. Conducting periodic reviews to ensure processes and procedures reflect any new conditions is important in ensuring a facility’s overall hygiene and its products’ quality and safety. Reviewing the EMP results and trending on a regular basis and adjusting your program according to the results is important to keep ahead of any potential issues.
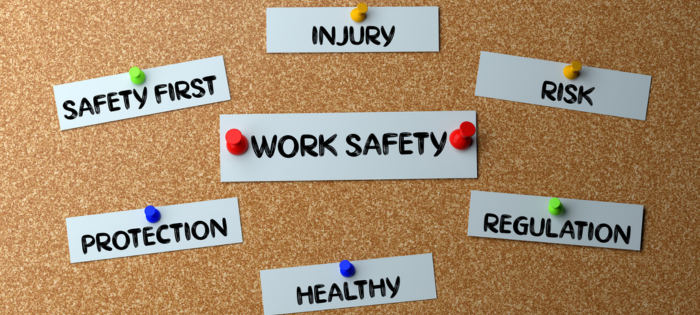
Comments: No Comments
5 Resolutions for Health and Safety
As discussed in KTL’s recent EHS: Top Trends for 2025 article, there are a number of anticipated challenges and opportunities in environmental, health, and safety (EHS) for 2025—some ongoing and some just gaining traction with impacts yet to be known, particularly with the change in Administration just taking hold. Regardless, the importance of investing in a strong health and safety program cannot be underestimated. Here are five tips to help start the year strong in health and safety.
1. Plan for Consistency. With so many changes happening in the world at such a rapid-fire pace, consistency creates a predictable environment for employees to maintain positive health and safety practices. Consistency in both action and communication is equally important in the health and safety world. Inconsistent expectations and actions lead to inconsistent behaviors. Ambiguity in messaging and instructions can further cause health and safety hazards.
Keep it simple and consistently reinforce the same message to elicit consistent safety performance. As some examples:
- Always use the right tool for the job.
- Stop work when needed to address hazards.
- Communicate with other personnel about hazards.
- Always wear the proper personal protective equipment (PPE) for each task.
2. Focus on Continuous Small Improvements. Continuous improvement does not mean erratic change. Change should be sustainable, and that happens best when it is introduced and implemented incrementally. Small changes can lead to big differences; it just requires a plan. Identify the big goal, and then define those small steps needed to reach it. Thinking big but acting small can help create buy-in across the organization, consume fewer resources, and create small “wins” more quickly to drive momentum toward reaching the big goal.
3. Prioritize Communication in All Forms. When it comes to the characteristics of an excellent safety culture, communication is at the top. It is vital that all levels of management (i.e., senior, middle, supervisory) communicate their commitment to safety clearly to workers. It is equally important that workers feel empowered to discuss their safety concerns. Having a safety culture where workers do not feel like they can speak up at work when it comes to their safety can present significant threats to workers and the overall well-being of the company.
- Use a variety of communication channels (e.g., one-on-one conversations, regular safety briefings, written materials, visual aids) to improve worker understanding.
- Practice active listening; communication goes two ways!
- Be clear, concise, and consistent in your messaging (see #1 above).
4. Incorporate Leadership. In its Recommended Practices for Safety and Health Programs, the Occupational Safety and Health Administration (OSHA) outlines best practices for implementing and maintaining a health and safety program. Management leadership is a core element. According to the guide, management provides the leadership, vision, and resources needed to implement an effective health and safety program. Management can exhibit this in several ways:
- Demonstrate a commitment to continuously improving workplace health and safety, including eliminating hazards and protecting workers.
- Make safety and health a core organizational value with associated health and safety goals and objectives.
- Establish program expectations and responsibilities that engage employees.
- Provide adequate resources and support for the program
- Set a good example when it comes to prioritizing health and safety.
- Communicate regularly with workers about the importance of workplace health and safety.
5. Encourage Worker Participation. Worker participation is another of OSHA’s core elements of workplace health and safety in its Recommended Practices for Safety and Health Programs. Engaging workers at all levels in establishing, implementing, evaluating, and improving health and safety in the workplace creates buy-in. It is important that organizations encourage workers to report health and safety concerns and promote a psychologically safe environment. Organizations should also work to actively engage employees in other health and safety initiatives, such as conducting hazard assessments, developing policies, serving on safety committees, leading toolbox talks, and more.
All of these tips come down to one thing—protecting employee health and safety. Regardless of external factors (e.g., regulatory uncertainty, supplier requirements, consumer demands, financial incentives, etc.), protecting employees should always be a top priority, and these five tips can help ensure you start the year strong.
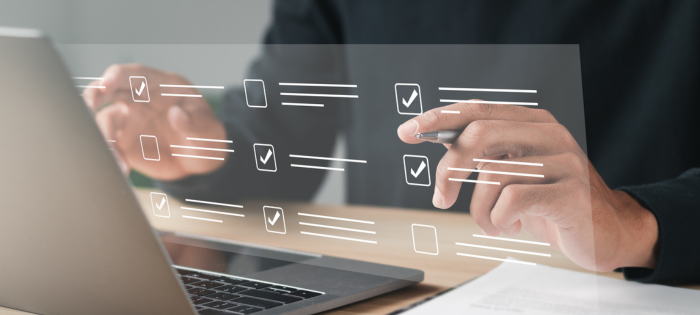
Tech Corner: Task Tracking Tool
Functionality: What does it do?
Organizations face endless numbers of tasks associated with compliance, certification, and other internal and external requirements. Task tracking can provide an effective project management tool to track all these tasks and their associated deadlines in one place. Leveraging Microsoft SharePoint®, KTL’s Task Tracking Tool not only tracks tasks to completion, it also allows project managers to assign tasks to responsible individuals, automate reminders, attach documents, share updates with their team, and more for any task—from project management to regulatory deadlines.
Benefits: Why do you need it?
KTL’s Task Tracking Tool offers the following benefits:
- Centralization: Users can view all tasks, owners, details, and due dates in one place.
- Customizable: All aspects of a task list can be customized to track the information you need.
- Notifications: Custom notifications can be tailored for upcoming deadlines, status changes, and task assignments.
- Recurring Tasks: Routine tasks can be scheduled to recur according to desired schedules.
- Dashboards and Reporting: Data related to tasks (e.g., percent completion) can be displayed visually to help identify and report on trends and patterns.
Technology Used
- SharePoint
- Power Automate
- Power Apps or alternative
- Power Bi
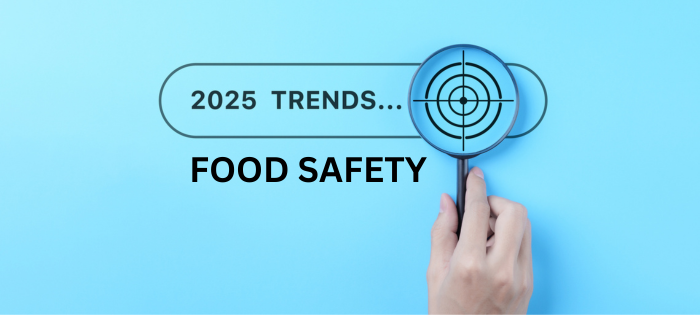
Comments: No Comments
Food Safety: Top Trends for 2025
The food system and supply chains continue to change and evolve at an accelerated pace. That introduces new risks and challenges—and heightens some familiar ones. As we move into 2025, the Food and Drug Administration (FDA) has established priorities that will impact how food companies operate in the coming year. In addition to the FDA’s priorities, here are some of the top food safety trends KTL’s food safety experts are tracking in 2025…
FDA 2025 Priorities
On October 1, 2024, the Food and Drug Administration (FDA) began implementing its reorganization, including launching a unified Human Foods Program (HFP) to oversee all activities related to food safety and nutrition. The HFP has prioritized key deliverables for FY 2025 to strengthen regulatory oversight, advance science, and better leverage partnerships in the areas of microbiological food safety, food chemical safety, and nutrition. The FDA also restructured the Office of Regulatory Affairs (ORA) into the Office of Inspections and Investigations (OII) to allow the Agency’s field operations unit to focus on inspections, investigations, and imports.
As with any regulatory change, FDA-regulated companies need to understand the restructuring and its potential impacts. The HFP has outlined priorities and compliance expectations that companies need to align with their internal programs, protocols, etc. It will also be important to prepare for potential changes when it comes to inspections, including more frequent and more specialized inspections.
Update: According to Food Safety Magazine, on January 21, 2025, federal public health agencies within the U.S. Department of Health and Human Services (HHS) received orders from the new Administration to temporarily pause all external communications until further notice. This includes the FDA and U.S. Center for Disease Control and Prevention (CDC), which are jointly responsible for ensuring the safety of most of the U.S. food supply and responding to foodborne illness outbreaks. All external communications must be reviewed and approved by a Presidential appointee before being issued. The directive will be in effect until February 1, 2025
Foodborne Illness
The U.S. has experienced several high-profile food recalls in 2024 that have caused illnesses and deaths—and heightened public awareness and concern. The emergence of new bacterial and viral strains and the evolution of pathogens (e.g., Listeria, E. coli, Salmonella) that are becoming resistant to traditional food safety measures are growing concerns when it comes to preventing foodborne illnesses.
The FDA’s focus on microbiological food safety (see above) is intended to advance strategies to prevent and mitigate foodborne illnesses. On July 29, 2024, U.S. Department of Agriculture (USDA) issued its proposed rule and determination to more effectively reduce Salmonella contamination and illnesses associated with raw poultry products; final rulemaking is anticipated in 2025. The USDA Food Safety and Inspection Service (FSIS) further announced several immediate initiatives to enhance its approach to mitigating foodborne pathogens, including modernizing L. monocytogenes regulation and ready-to-eat (RTE) sampling, in response to the Boar’s Head inspection results.
Companies need to re-evaluate their food safety programs and their effectiveness. This review may necessitate changing the current level of scrutiny for current and prospective suppliers. If sourcing any products implicated in recalls, re-evaluating current suppliers’ compliance with food safety regulations is also recommended. Sanitary equipment design, robust cleaning procedures, effective traceability programs, adherence to Good Manufacturing Practices (GMPs), and adequate training will remain key to avoiding recalls.
Supply Chain Traceability
There continues to be a real need for standardization, stronger linkages throughout the supply chain, improved communication and recordkeeping, and faster response when it comes to product traceability. As such, the FDA has prioritized the advancement of traceability tools and resources to help remove contaminated products from the marketplace more quickly.
From a regulatory standpoint, companies must start meeting the requirements of the Food Traceability Rule by January 2026, though there is speculation this may be delayed due to a provision in the current draft House appropriations bill that would prohibit funding for implementation, administration or enforcement of these regulations. Regardless, organizations should be performing traceability exercises to help identify gaps, testing protocols and verifying effectiveness, implementing corrective actions, and ensuring adequate traceability processes are in place. Investing in a good technology solution that integrates with the food safety management system (FSMS) will help to further streamline the process.
Sustainability
The U.S. Environmental Protection Agency (EPA) cites that food and food packaging materials make up almost half of all municipal solid waste in the U.S. Federal and state regulatory agencies, as well as various food safety certification schemes, have begun incenting—or requiring—organizations to incorporate sustainable food management and recycling practices into their operations. For example, the New Jersey Recycled Content Law, which came into effect on January 18, 2024, is considered one of the most ambitious recycled content laws to date.
A thorough food and packaging assessment serves as the foundation for reduction efforts. Having a general understanding of operations and waste streams can help identify appropriate strategies to avoid waste, cut down on disposal costs, reduce over-purchasing and labor costs, optimize inventory management, use more recycled content, and reduce water and energy use associated with food production.
Employee Safety
Between October 2018 and September 2019, the Occupational Safety and Health Administration (OSHA) issued 1,168 citations resulting in over $7 million in fines to the food manufacturing industry, with lockout/tagout and machine guarding topping OSHA’s annual list of the most frequently cited standards in food manufacturing. Occupational safety and health risks in food manufacturing are often heightened because of the nature of the product (i.e., food or drink) being manufactured.
OSHA is watching, and facilities need to prioritize employee safety. Conduct a thorough hazard analysis of the facility, operations, and processes to identify potential safety hazards. Based on the analysis, develop, implement, and maintain the appropriate safety programs, procedures, and instructions. Provide the proper personal protective equipment (PPE) to keep employees safe. And, importantly, train employees so they understand what they need to do to protect themselves and others.
PFAS
The EPA continues to make significant contributions to confront the human health and environmental risks of per- and polyfluoroalkyl substances (PFAS). In April 2024, EPA introduced the first national drinking water standards for PFAS, and many states are introducing policies related to PFAS, including monitoring and testing for PFAS in water and banning PFAS in food packaging, clothing, and other consumer products. The FDA is further working to limit PFAS in food and food packaging. In 2024-2025, the FDA has committed to testing foods from the general food supply to more accurately estimate exposure to PFAS from foods. This includes testing total dissolved solids (TDS) samples, conducting a survey of bottled water, and conducting additional seafood testing.
Organizations need to address PFAS in their operations, products, supply chains, and waste streams; stay informed about ongoing PFAS regulatory developments; and adjust compliance programs and operational practices, as needed.
Digital Transformation
According to McKinsey & Company, automation could increase productivity by up to 20% in the food manufacturing sector. More companies are employing technology solutions to improve business efficiency, and the FDA has prioritized developing AI approaches to help monitor new data and trends in FY 2025.
AI is quickly becoming a more viable solution for many food companies in automating, monitoring, and managing food safety, helping to identify contamination risks, analyze data, predict potential hazards, conduct training simulations, and even optimize cleaning schedules. While the efficiencies and other benefits of technology solutions are many, the increased reliance on AI will require an investment, not just financially but also in oversight and management, training, and cybersecurity measures. As the digital transformation continues, companies will need to determine where automation is appropriate and where the human factor is still required.
Others to Watch
- Red No. 3: On January 15, 2025, the FDA amended its color additive regulations to no longer allow for the use of Red No. 3 in food and ingested drugs. Manufacturers who use Red No. 3 will have until January 15, 2027 (food) or January 18, 2028 (ingested drugs) to reformulate products. Foods imported into the U.S. must also comply with this requirement.
- Produce Safety Rule: Pre-Harvest Agricultural Water: In May, 2024, the FDA released the updated requirements for the Produce Safety Rule, Subpart E for pre-harvest agricultural water. Facilities are now able to justify not testing agricultural water if there are no conditions (e.g., animals, human waste, or biological soil amendments of animal origin (BSAAO)) on nearby or adjacent land that pose a risk to the water source. The first compliance date for large farms is April 7, 2025.
- SQFI New Edition 10: The Safe Quality Food Institute (SQFI) is slated to release SQF Edition 10 in July 2025. Anticipated updates focus on the identification of new food safety risks, changes in the global supply chain that may impact food safety, unforeseen events (e.g., foodborne illness outbreaks), new technology, and harmonization with other internal food safety programs.
- Bird Flu (H5N1): With the rise in cases and mutations, the USDA has announced different approaches to prevent the spread of H5N1, including testing bulk raw milk. The State of California also declared a state of emergency to allocate more resources to address the continued spread of Bird Flu.
- Food Date Labeling Reform: In December 2024, the FDA and USDA announced a joint Request for Information (RFI) regarding food date labeling (e.g., ‘Sell By,’ ‘Use By’ and ‘Best By’). Open date labeling is currently not mandated or standardized by federal law. The RFI seeks information on industry practices and preferences for date labeling.
Set Your Goals for 2025
In 2025, organizations will continue to encounter workplace challenges, regulatory adjustments, food safety concerns, and rapid technology advancements—and, in most cases, fewer resources to manage it all. KTL suggests completing the following early in 2025 to prepare for whatever is on the horizon:
- Get senior leadership commitment and invest in creating a food safety culture that prioritizes food safety, quality, and employee health and safety. Focus on changing from a reactionary to a preventive mindset. And remember that your people are as important as your products.
- Conduct a comprehensive food safety and quality gap assessment. Know your operations, inventory your ingredients, understand your supply chain, quantify your food waste. This assessment should be the starting point for understanding your regulatory and certification obligations and current compliance status—and for ensuring you are prepared to meet pending regulatory developments.
- Explore technological advancements that allow for further digitization and promote more timely and accurate collection and management of important data. This could mean stepping into the world of AI and machine learning; it could also mean implementing a digital FSMS to help manage compliance/certification and recordkeeping requirements. Technology advancements can help create significant business efficiencies when used appropriately.
- Train your staff. Every trend discussed above requires employee understanding. Train your team routinely on requirements, responsibilities, processes, expectations, etc. Of particular note for Preventive Controls Qualified Individuals (PCQIs), the International Food Protection Training Institute (IFPTI) has released Version 2.0 of the Preventive Controls for Human Foods course. The old version will no longer be taught as of May 2025, but the training will still be recognized.
- Seek third-party oversight. Having external experts periodically look inside your company provides an objective view of what is really going on, helps you to prepare for audits, and allows you to implement corrective/preventive actions that ensure compliance. An outside expert can often provide the “big picture” view of what you have vs. what you need; how your plans, programs, and requirements intersect; and how you can best comply with changing requirements.
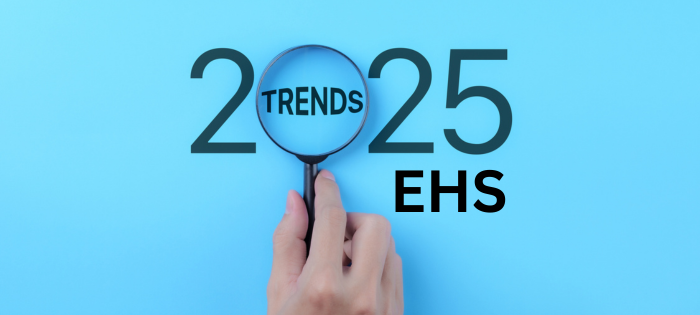
Comments: No Comments
EHS: Top Trends for 2025
Every year, we see a number of environmental, health, and safety (EHS) trends rise to the surface that have the potential to impact many industries. As we enter 2025, some challenges and opportunities in EHS remain ongoing; some are just gaining traction with impacts yet to be known, particularly with a change in Administration just taking hold. Here are some of the top EHS trends KTL is keeping watch on in 2025…
Regulatory Landscape
In 2022, the Environmental Protection Agency (EPA) published its FY 2022-2026 EPA Strategic Plan to communicate the Agency’s vision, priorities, and strategies. Specifically, the Plan includes targeted objectives and outcomes in the areas of climate change; environmental justice; compliance enforcement; clean land, air, and water; and chemical safety. The Occupational Safety and Health Administration’s (OSHA’s) focus centers on National Emphasis Programs (NEPs) for 2025 related to combustible dust, fall protection/prevention, heat, silica crystalline, and warehousing and distribution center operations, as well as many regional directives.
With a new Administration taking office in January, a big unknown of the coming four years is how the EHS regulatory landscape will change. There is speculation regarding plans to reorganize the EPA and establish “pause and review” teams to assess major rules, guidance materials, grants, legal settlements, budgets, etc. How this will translate into regulatory action remains to be seen.
Update: According to InsideEPA.com, acting EPA Administrator James Payne issued a directive on January 24, 2025, ordering all EPA staff to stop all communications with external parties pending further instruction. Exemptions will allow EPA staff to continue to communicate with state and federal agencies, provided they do not discuss enforcement matters; talk to relevant partieis to facilitate imports; and continue conducting inspections. It is unclear at this time how long the directive will remain in place.
Mental Health
Companies are increasingly recognizing that traditional safety programs must evolve to prioritize mental health as much as physical health—from mental health days to employee assistance programs, to stress management training, to flexible work hours. Correspondingly, psychological safety is becoming a critical concept for building effective teams and encouraging workplace innovation and success. A psychologically safe culture allows employees to take reasonable risks in a safe environment without negative interpersonal consequences.
A related concept is safety culture, which is concerned with many cognitive aspects of safety, like norms, perceptions, beliefs, and values. Emphasizing mental health as part of the organization’s safety culture may become a priority for mature organizations. As the concept of total worker health continues to expand, the focus on mental health is also likely to be reinforced by new regulations and standards regarding psychological safety in the workplace.
Sustainability and Climate Change
Environmental, Social, and Governance (ESG) initiatives have dominated many corporate agendas for the past several years, particularly with Europe and Canada advancing standards related to sustainability and climate change data reporting and ISO’s recent Climate Change Amendments. Many organizations have worked to significantly improve their data collection efforts and have integrated climate change management and circular economy principles into their sustainability strategies.
The change in Administration may increase scrutiny regarding the value of these ESG initiatives. We have already seen the Securities and Exchange Commission’s (SEC) March 2024 Climate-Related Disclosures Rule stayed due to multiple petitions and lawsuits. This may be a sign of things to come. Many companies have invested in their ESG efforts and will continue to do so, but 2025 may present an opportunity to reassess and streamline initiatives to ensure they are practical and upholding sustainability goals, while also contributing value to the company.
PFAS
Per- and polyfluoroalkyl substances (PFAS) became a focal point for EPA in 2021 with the publication of its PFAS Strategic Roadmap, which committed to addressing concerns related to PFAS exposure. Actions have included improving reporting on PFAS, as well as adding seven additional PFAS to the Toxics Release Inventory (TRI) in January 2024 and an additional nine in January 2025. In April 2024, EPA announced three more notable actions, including introducing the first-ever national drinking water standards and designating perfluorooctanoic acid (PFOA) and perfluorooctane sulfonic acid (PFOS) as “hazardous substances” under Superfund. In addition, the updated Interim Guidance on the Destruction and Disposal of PFAS and Materials Containing PFAS will require entities to report releases of these “forever pollutants” that exceed threshold quantities.
Beyond federal regulations, many states are introducing policies related to PFAS, including monitoring and testing for PFAS in water and sewage sludge and banning PFAS in food packaging, clothing, and other consumer products. Organizations need to address PFAS in their operations, products, supply chains, and waste streams; stay informed about ongoing PFAS regulatory developments; and adjust compliance programs and operational practices, as needed.
Personal Protective Equipment (PPE)
Properly fitting PPE is essential for workers to complete their tasks safely. If PPE is not correctly fitted to the body, it can cause discomfort and increase the risk of workplace accidents and injuries. On December 11, 2024, the Occupational Safety and Health Administration (OSHA) announced its finalized revision to the PPE Standard for Construction, which requires PPE to properly fit any construction worker who needs it, including women and physically smaller or larger workers.
Employers must ensure that every employee not only has the right PPE, but that it also fits. Fit testing may identify the need for PPE alternatives to meet the anthropometric needs of all workers. Importantly, employees must be trained and empowered to speak up if PPE does not fit appropriately to ensure their safety.
Technology/AI
Artificial intelligence (AI) and machine learning technologies have the capacity to significantly alter how companies manage their EHS programs. While still not fully mature, these technologies are becoming more sophisticated. As AI evolves and becomes more generally accepted, more companies are likely to start adopting it to automate routine compliance tasks, conduct EHS assessments, perform training simulations, predict potential safety incidents, monitor workplace conditions in real-time, and more.
While the efficiencies and other benefits of technology solutions are many, the increased reliance on AI and machine learning will require increased oversight and management. In particular, companies will need to determine where automation is appropriate and where the human factor is still required. Not all processes lend themselves to AI. It will also be imperative to consider stronger data privacy protocols to ensure the security of the company.
Others to Watch
- OSHA Reporting: On January 1, 2024, the Department of Labor’s (DOL’s) final rule requiring employers in designated high-hazard industries to electronically submit injury and illness information to OSHA took effect. KTL inspections routinely find errors and omissions in OSHA recordkeeping. Effective solutions, particularly areas where hard copies can be replaced by digital forms, are needed.
- Hazard Communication Standard: The final Hazard Communication Standard took effect on July 19, 2024, implementing the first major updates since 2012. The first compliance date requires chemical manufacturers, importers, and distributors to update labels and Safety Data Sheets (SDSs) for chemical substances by July 19, 2026.
- Lead Levels: In January 2024, the EPA reduced the acceptable amount of lead in soil for residential exposure, stating that no level of lead is acceptable. These reduced levels may soon be translated into commercial exposures.
- One Health: Both the Society of Environmental Toxicology and Chemistry (SETAC) and Society of Toxicology (SOT) have adopted One Health initiatives as an integrated, unifying approach that aims to sustainably balance and optimize the health of people, animals, and ecosystems (SOT). The idea is to look at the health of our environment and all aspects of our environment as a whole and not one component at a time. This idea is being translated into health impact assessments.
- Pesticide/Herbicide Re-evaluation: The EPA has initiated re-evaluations of registered pesticides, herbicides, rodenticides, and fungicides, including the highly publicized Roundup. These reviews are expected to result in a recommendation to focus the use of these chemicals rather than using a general broadcast application.
- Microplastics: Microplastics have been found in every ecosystem on the planet—in food, beverages, and human and animal tissue. Scientists do not fully understand the impacts of microplastics on human health and aquatic life, and industry is struggling with how to manage them due to their pervasive nature and wide variety of shapes and sizes. Ongoing research in pollution prevention will be forthcoming.
Getting Ahead in 2025
In 2025, organizations will continue to encounter evolving workplace challenges, regulatory adjustments, societal demands, economic pressures, and rapid advancements in technology—some of which can be anticipated, some which remain to be seen. KTL suggests completing the following early in 2025 to prepare for whatever is on the horizon:
- Get senior leadership commitment. Even with the best EHS personnel, the organization and its EHS system will only be as strong as the top leadership and what they prioritize.
- Stay abreast of regulatory developments. Monitor what is going on at the federal (i.e., EPA and OSHA) and state levels, assess your regulatory applicability, and evaluate how any potential regulatory changes over the next year(s) may impact your operations.
- Conduct a comprehensive gap assessment to ensure you are efficiently meeting your EHS requirements (i.e., regulatory, management systems, internal, supply chain). Think critically about how overlapping requirements may apply (e.g., your chemical inventory may uncover requirements for air permitting, waste management, Tier II report, etc.) and how you can integrate systems to improve efficiency and compliance.
- Determine where you can integrate technology solutions into your operations. This could mean stepping into the world of AI and machine learning; it could also mean implementing compliance information management systems to help manage compliance and reporting requirements. Technology advancements can help create significant business efficiencies when used appropriately.
- Seek third-party oversight. Many EHS departments are severely understaffed. Having external experts periodically look inside your company provides an objective view of operations, helps you to prepare for audits, and allows you to implement corrective/preventive actions that ensure compliance. An outside expert can often provide the “big picture” view of what you have vs. what you need; how your plans, programs, and requirements intersect; and how you can best comply with changing requirements.