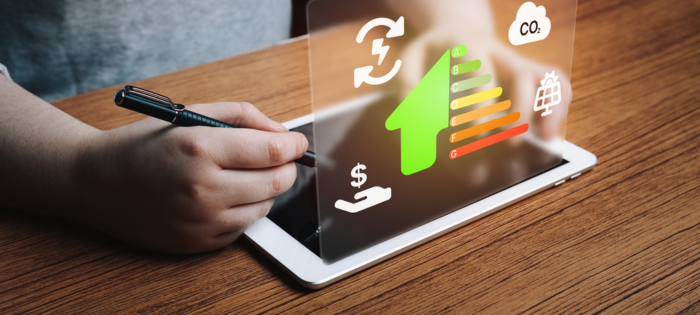
Comments: No Comments
What Is an Energy Audit–And Why You Should Do One
Want to reach your sustainability goals, improve your energy efficiency, and save money? An energy audit can help you better understand your energy usage and issues—and identify opportunities to create energy efficiencies, reduce your carbon footprint, and positively impact your stakeholders.
What Is an Energy Audit?
An energy audit is a key part of energy management. Energy management involves monitoring and controlling energy consumption across an organization to save energy, save money, and protect people and the environment. Energy management should be part of any organization’s overall strategy. An energy audit helps determine energy usage and opportunities for efficiency projects at your facility, building, or process. The overarching goal of an energy audit is ultimately to reduce energy consumption and improve efficiency without impacting work processes or products.
Types of Energy Audits
An energy audit can take a range of forms depending on how detailed and extensive it needs to be:
- Preliminary Analysis: Review bill, conduct energy usage trending.
- Treasure Hunt: Conduct a group exercise walking around identifying obvious wastes.
- General Audit: Analyze specific systems, conduct detailed inspection.
- Comprehensive Audit: In addition to the areas covered above, may include longer term monitoring and mechanical/electrical/civil engineering reviews.
- Ongoing Audit: Long-term monitoring of efficiency systems, scheduling retro-commissioning.
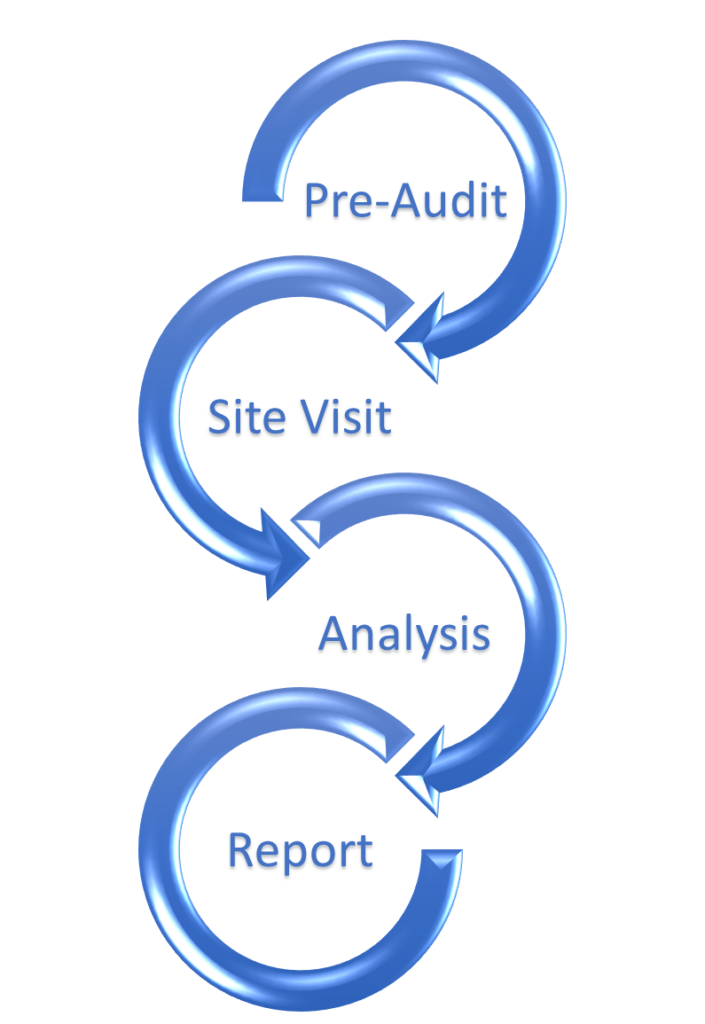
General Energy Audit Process
In general, the energy audit process comprises several steps and activities that culminate in final recommendations to improve energy performance and efficiency.
The pre-audit is a desktop review that helps to identify energy consumption patterns, including the energy “hogs” and peak usage trends (i.e., the hours of the day during which demand for electricity is the highest). It consists of the following activities:
- Review utility bill for demand charges, power usage, load factor.
- Demand charges are fees applied based on the highest amount of power drawn during any interval during the billing period. Demand charges can comprise a significant proportion of commercial customers’ bills.
- Load factor is a measure of the utilization rate or efficiency of electrical energy usage. It is an indicator of how efficiently energy is being utilized.
- Review equipment repair and occupant complaint logs.
- Review past audit results.
- Discuss with management internal goals, financial criteria, upgrades, and future plans.
The site visit allows the auditor to observe facility operations and assess how systems are operating in practice. It comprises activities such as the following:
- Conducting interviews with operators, key decision-makers, and other plant staff.
- Collecting data, including facility data, nameplate data, forms, and logs.
- Performing a site walkthrough/tour to review:
- Site development.
- Building envelope.
- BTUs of boiler/HVAC, compressors, refrigeration, large equipment, etc.
- Building exterior (e.g., roof plan, outdoor lighting, exterior equipment).
- Taking measurements (i.e., combustion, lighting, temperature, ultrasonic).
After collecting the pre-audit documentation and site visit observations, the auditor is able to then perform a detailed analysis of energy performance. This analysis involves calculating the following:
- Energy usage, including baseload and peak energy, adjusted for weather, occupancy, and production.
- Energy costs, including accurate application of rates, time of use applications, seasonal applications, utility bill ratchet.
- Energy efficiency measures (EEMs), including material and installation, disposal, engineering design, permits and fees, and rebates and incentives.
The final report provides an action plan highlighting short-term (i.e., low-hanging fruit) opportunities, long-term budgeted improvements, and company goals. It should also reference site management, potential future problems, and testing programs that can all impact energy programs and operations.
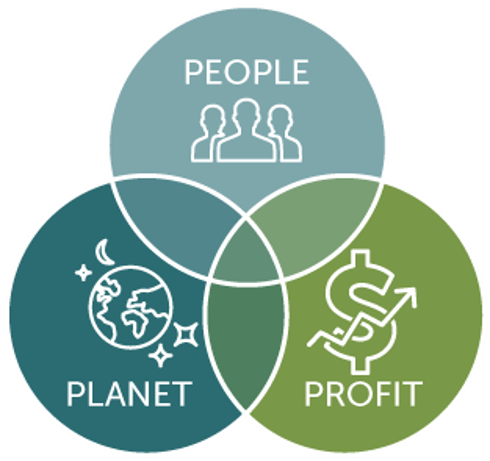
Impacting People, Planet, and Profit
Energy audits directly impact the three Ps of the triple bottom line:
People. The United Nations has identified climate change as the number one threat to human societies. Brown energy releases can substantially impact air quality and have significant negative impacts on human health. Creating energy efficiencies and reducing the use of non-renewable energy is key to mitigating this threat. Beyond the human health threat, improved EEMs can improve employee satisfaction and, subsequently, create a corporate culture shift that embraces sustainability. For example, optimized lighting, ventilation controls, and incentives for driving electric vehicles may lead to healthier and happier employees and improved retention.
Planet. In its simplest terms, reducing energy usage helps reduce carbon footprint and mitigate the impacts of global warming. For example:
- Fossil fuels are a finite resource. Reliance on them leads to the destruction of protected ecosystems and habitat. Lower energy demand decreases the need for power generation and the use of fossil fuels.
- Energy audits identify ways to reduce energy use. This, in turn, reduces air emissions and global pollution levels. The equation is simple: the less energy you use, the fewer carbon emissions you produce.
- Beyond energy efficiencies, energy audits also identify waste. Eliminating these waste streams prevents unnecessary landfill use and contributes to environmental sustainability.
Profit. The Carbon Trust estimates that most businesses can cut their energy costs by at least 10% (often by 20%) with simple actions that offer a quick return on investment. Operating more efficiently reduces energy consumption, which equates to significant savings on utility bills. This is particularly important as energy costs reach all-time highs. In addition, organizations that consume significant amounts of energy are at greater risk of being impacted by energy price increases or supply shortages. When an organization can reduce its demand for energy, it also reduces the risks associated with an energy shortage. Having greater control over energy consumption creates resiliency against energy price fluctuations.
Return on Investment
Once you have a comprehensive understanding of how energy is being consumed, it becomes possible to identify inefficiencies and opportunities for improvement, whether related to behavior (e.g., asking employees to turn off lights every night), technology (e.g., implementing integrated building management systems), or process (e.g., increasing operations during off-peak hours).
Energy audits may identify the following opportunities to reduce costs:
- Reducing operational inefficiencies, including continual running of motors, unoccupied spaces (light sensors), compressed air leaks, and others.
- Implementing EEMs, such as monitoring systems for malfunctions, insulating hot/cold water piping, implementing efficient lighting, and ensuring heat recovery.
- Optimizing building systems, including ventilation systems, lighting control systems, insulation, efficient windows, green roofs, etc.
- Identifying financial incentives, rebates, and demand response programs.
Energy Audit Best Practices
To get the most out of an energy audit, it takes time, data, budget, and buy-in. The following can help ensure your audit is successful and provides return on investment:
- Start small, plan ahead. Select the right type of audit based on the resources (i.e., time, financial, personnel) you have available. You can scale up your efforts over time.
- Set clear objectives. Identify what your organization wants to get out of the audit. Consider the 3 Ps—people, planet, and profit—and be open-minded. It may be about energy savings and cost reduction, but it also may be about meeting sustainability goals, creating a culture change, or retaining and attracting employees.
- Gather data. Review utility bills. Trend energy consumption. Assess building specifications.
- Enlist audit expertise. Engage the right auditors with the right qualifications. A Certified Energy Manager (CEM) and someone with an engineering background can add a depth of expertise to help identify concerns and opportunities beyond the “low-hanging fruit”.
- Conduct routine inspections and assessments. Update your maintenance program to include steam trap surveys, compressed air leak inspections, duct cleaning, and other routine inspections. These routine inspections allow for early detection of costly issues, and predictive maintenance can help reduce downtime and expand equipment life.
- Conduct routine measurement and verification. Just because you have implemented a system, process, or equipment does not mean that it is functioning as intended. Assess your EEMs regularly to ensure they are achieving the desired results.
- Engage your stakeholders. Include management staff, employees, and other decision-makers in your efforts. Engaging these stakeholders in creating solutions can help create buy-in and a culture change that makes energy efficiency and sustainability a way of doing business.
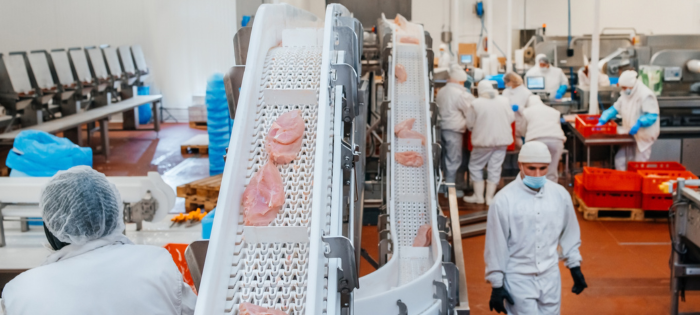
Comments: No Comments
Challenging the Food Defense Program
The Food and Drug Administration’s (FDA) Intentional Adulteration (IA) Rule aims to prevent acts targeting the food supply that are intended to cause wide-scale harm to public health. The IA Rule requires food businesses to assess and identify vulnerabilities in their processes, operations, and facilities; implement strategies to reduce those vulnerabilities; and then regularly monitor and verify the effectiveness of those strategies to reduce the occurrence of IA acts. A food defense “challenge” (also known as an intrusion test) is then used to assess how well those strategies are implemented throughout the organization.
What is the purpose of the IA intrusion test?
The purpose of an intrusion test is to evaluate a company’s existing food defense programs for proper implementation across the company by “challenging” the system’s efficacy. In an unannounced intrusion test, a food safety expert scopes out the facility and its vulnerabilities, attempts to gain access to sensitive areas, and tests how the food defense system works in practice.
The test helps facilities to:
- Assess whether food defense procedures are effectively implemented throughout the facility—and are being followed by personnel.
- Highlight facility strengths and implementation failures.
- Close identified gaps and reinforce programs, where needed.
- Meet FDA regulatory and Global Food Safety Initiative (GFSI) certification standard requirements.
Am I required to do one of these challenges?
To truly ensure food safety and defense programs work, they need to be challenged. The GFSI benchmarked certification standards all require some version of testing:
- SQF: The food defense program must be tested to ensure food defense strategies are effective, appropriate, and documented. This test can be based on a fictitious scenario that allows an intruder to enter the building and challenge the system.
- FSSC 22000: Organizations must conduct and document a food defense threat assessment based on defined methodology to identify and evaluate potential threats linked to processes and products.
- BRCGS: A documented risk assessment must be conducted to identify potential risks to the security of product and to ensure appropriate controls implemented to reduce the risk.
- IFS: The food defense plan must be tested for effectiveness and reviewed at least annually or whenever significant changes occur.
What does the process look like?
An important part of these tests is that they are unannounced, so personnel continue to operate as usual versus being on heightened alert. Tests are typically coordinated and scheduled with company leadership to take place at a time/date that is undisclosed to plant employees. Company leadership provides the food safety expert with documentation that confirms the test and outlines who to contact when/if “apprehended” to help keep the food safety expert safe.
Prior to conducting the test, the food safety expert will generally tour the facility to identify sensitive areas to target and opportunities to enter the facility. This is important since the first critical step in conducting the test involves gaining access to the building, whether through finding unlocked doors, pretending to be plant personnel, or even creating a cover story and walking through the front door.
Once the food safety expert is in the facility, the objective becomes to try to access as many sensitive areas as possible to truly “test” the system. The intrusion test is followed up with a detailed findings report that provides recommendations for closing gaps and strengthening the facility’s food defense program.
What does the IA intrusion test include?
An IA internal intrusion test evaluates company preparedness for intentional trespassing and internal attacks on sensitive areas inside the facility. The intruder will take advantage of employee movement (e.g., arrivals, breaks, lunches, departures); focus on physical controls of building access (e.g., employee entrances, garage doors, receiving/loading areas); and target sensitive internal areas within the building. The challenge will involve testing facility procedures and employee implementation, as well as the following food defense mechanisms:
- Card access/badge system/key protocol
- Reception area
- Visitor control/sign-in program
- Security guards
- Camera system
- Exterior door security
- Lighting
- Shipping/receiving areas
- Fencing
- Parking lot
What are common missteps identified in intrusion tests?
In many cases, the issues encountered are seemingly small things; however, the small issues can quickly result in very big problems if an intruder is able to access sensitive areas. Some of these include the following:
- Employees forget to ensure the door is shut and fully latched when leaving an area.
- Employees do not question the presence of visitors and, in some cases, will even open the door for an unknown individual.
- Badges and uniforms are left unattended throughout the facility for intruders to steal and use as identification. With this identification, interior areas are relatively easy to access and contaminate.
- Doors are not locked—either inadvertently or because locking mechanisms are not repaired—or are propped open for ease of access.
- Equipment on the exterior of the facility (e.g., ladders, company vehicles, tools, etc.) is not adequately controlled.
What can facilities do to prevent IA?
Training staff to understand food defense risks, identify suspicious activities and individuals, and implement preventive measures is key to reducing IA risk. FDA and the Department of Homeland Security’s (DHS) See Something, Say Something Campaign reminds front-line employees of what to look for and how to respond if suspicious activity occurs.
Importantly, staff must feel empowered to notify management if they notice anything suspicious. This might include someone taking notes or videos in the plant; an individual attempting to gain access to restricted areas; theft of employee uniforms, badges, or packaging labels; unattended vehicles illegally parked near the facility; unattended items near the business (e.g., boxes, bags); and suspicious work behaviors/hours from employees.
Best practices to prevent this suspicious activity from causing wide-scale harm include the following:
- Post security personnel to serve as a deterrent for intruders.
- Properly maintain exterior doors, parking lots, and outside lighting.
- Keep doors locked and closed, including entrance, break room, and loading docks.
- Ensure visitor stickers are removed and disposed of upon checkout.
- Secure open containers of food/food ingredients.
- Control access of all employees, visitors, contractors, delivery personnel, etc. to sensitive areas.
- Make sure visitors to the facility are accompanied by an employee.
- Monitor products for evidence of tampering (i.e., seals, labels, packaging).
- Complete background checks on employees.
- Train personnel to report suspicious individuals or activities.
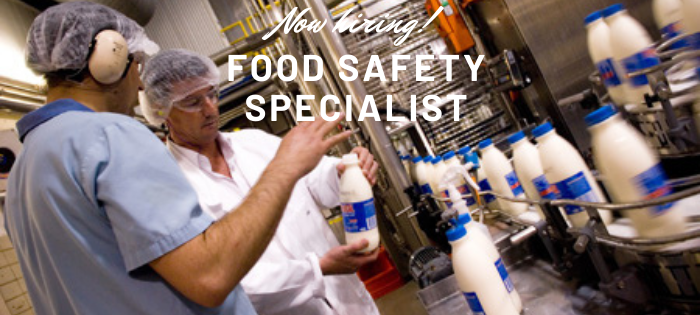
Now Hiring: Food Safety Specialist
Location: Chicago, Illinois (other locations considered)
KTL is seeking a Food Safety Specialist with 5-10 years of professional food safety consulting or relevant food industry experience to join our team. This individual will work under the direction of KTL Project Managers and Senior Consultants to manage and execute tasks for KTL’s food safety projects and meet client expectations. The Food Safety Specialist must have working knowledge of FDA, USDA, and GFSI requirements as they apply to food/food packaging manufacturing, processing, and distribution, and experience implementing/maintaining food safety documents and plans.
Responsibilities and tasks include the following:
- Providing HACCP, SOP, and SSOP development and implementation support
- Conducting gap assessments to FDA, USDA, and GFSI (i.e., IFS, BRC, FSSC22000, SQF) requirements
- Conducting relevant food safety training for clients
- Researching FDA, USDA, and GFSI regulatory requirements and maintaining standards updates
- Researching labeling regulatory review
- Interpreting third–party regulatory audits
- Reviewing, recommending, and coordinating efforts for environmental contaminants and pathogen testing program
- Working with clients and KTL senior staff to identify Food Safety Management System (FSMS) and program gaps and implement solutions for continuous improvement
- Maintaining and updating documents to ensure conformance and compliance consistency
- Participating in the development and management of KTL’s SharePoint® tools
- Assisting in growing clients and other business development efforts, as requested
Salary Range: $65,000 to $90,000 per year
Requirements
- B.S. degree in food science, biology, chemistry, technology, microbiology, or other related life science
- 5-10 years of related food industry experience in Quality Assurance/Control; experience in cooking, processing, manufacturing dairy, low-acid canned food, meat, or seafood preferred
- Excellent communication and presentation skills
- Excellent research, analytical, writing, and organizational skills
Preferred
- Microsoft SharePoint® and information management systems experience
- High–risk food or ingredients experience
- Understanding of food safety in food packaging
How to Apply
Forward a resume to recruiting@goktl.com.
Company Description
KTL is a management consulting firm providing EHS, sustainability, food safety, and quality consulting services to a wide range of industry, municipal, university, and government clients. Our focus is to build strong, long-term client partnerships and provide value-added solutions that simplify management systems, improve compliance, and establish more sustainable operations. KTL specializes in developing and implementing strategies, processes, and tools that complement our clients’ investments in existing programs and resources. Our highly qualified personnel have an in-depth knowledge of U.S. federal, state, and international EHS requirements; global food safety compliance; ISO management systems; and information management tools. Our consultants possess the education, work experience, and professional registrations necessary to provide value-adding consulting services to our clients.
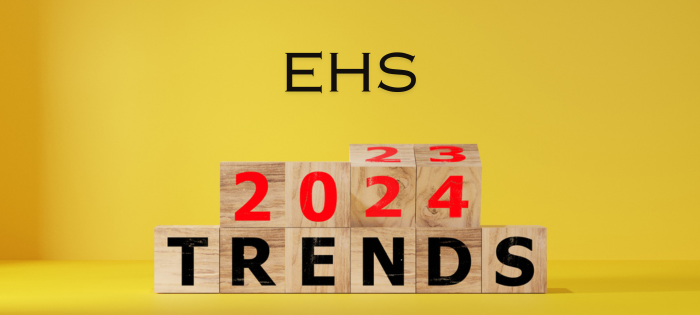
Comments: No Comments
EHS: 2024 Trends on Tap
According to a December 2023 press release, the Environmental Protection Agency (EPA) moved further and faster than ever before to deliver on its mission and protect human health and the environment in 2023. These actions—in addition to other trends in business efficiency, employee safety, and sustainability—have given rise to several new (and some ongoing) challenges and opportunities in environment, health, and safety (EHS). As a new year begins, it is important that companies understand their obligations, assess potential impacts, and prioritize efforts to ensure ongoing compliance and business performance.
Here are some of the top EHS trends KTL is keeping watch on in 2024—and some guidance to help you as you set your EHS strategy for the new year.
New OSHA Reporting Requirements
The Occupational Safety and Health Administration (OSHA) is focused on increasing transparency regarding workplace injuries with its new reporting requirements, which are effective as of January 1, 2024. The Administration is requiring organizations with more than 100 employees in certain high-risk industries to electronically submit information from OSHA Forms 300 and 301 to OSHA annually. In addition, certain high-hazard industries are now required to submit case-specific information. The data is intended to allow employers, employees, customers, the public, and other stakeholders to make more informed decisions about workplace health and safety. The deadline to submit information via the Injury Tracking Application is March 2, 2024.
Guidance: Maintaining robust occupational health and safety and incident records becomes even more important with these enhanced reporting requirements. Information technology (IT) tools, such as KTL’s OSHA 300 PowerApp with its comprehensive intake form tailored to OSHA 300 and OSHA 300A requirements, make it easier to collect, search, and analyze data—and maintain OSHA compliance. Using a digital format helps ensure no crucial data points are missed and makes it easy to filter, search, and analyze records and data to offer deeper insights into safety performance.
Climate Change and Environmental, Social, and Governance (ESG) Standards
In March 2022, the U.S. Securities and Exchange Commission (SEC) issued a proposed ESG Disclosures Rule that would require companies to 1) disclose how they are dealing with oversight and governance of climate-related risks; 2) identify any material climate-related risks and articulate their impacts on financial performance; and 3) provide comprehensive reporting of Scope 1, 2, and 3 greenhouse gas (GHG) emissions.
Leading the way, California passed its Climate Corporate Data Accountability Act (SB 253) and Climate-Related Financial Risk Act (SB 261) in 2023 to address the physical, human, and financial risks associated with climate change by requiring companies publicly disclose GHG emissions and climate change threats. Thousands of organizations that do business in California will now have to provide carbon emissions data by 2026—and companies across the country need to be prepared to follow suit.
Guidance: If it isn’t happening already, facilities need to start gathering emissions data, develop and implement a system to track GHG emissions, and create an action plan for climate disclosure. Accurate carbon accounting and energy management will allow companies to gain a deeper understanding of their emissions profiles and implement changes to improve energy efficiency and sustainability. If managed appropriately, these new disclosure requirements can provide a significant opportunity for companies to demonstrate a commitment to corporate social responsibility and improve brand reputation.
EPA Regulatory Enforcement
According to EPA, enforcement has been revitalized. We saw this trend pick up in 2023 with significant investments being made to enforce compliance with the nation’s environmental laws, including $213 million for civil enforcement efforts, $148 million for compliance monitoring efforts, and $69 million for criminal enforcement efforts. The past year has brought increases in onsite inspections, new criminal investigations, civil settlements, and cleanup enforcement. In 2024, EPA intends to continue its enforcement path, holding environmental violators and responsible parties accountable.
Guidance: Facility audits and assessments offer a systematic, objective tool to assess compliance across the workplace and to identify any opportunities for improvement before they become findings in an EPA inspection. These audits can also present an opportunity for organizational learning and development, particularly related to non-conformances. Conduct a gap assessment to evaluate whether processes and systems are functioning as intended, and then implement corrective and preventive actions to ensure compliance, particularly at the time of inspection. Look at the big picture and consider changes in production and business operations that may also change compliance requirements.
Per- and Polyfluoroalkyl Substances (PFAS)
EPA continues to make significant contributions in research and regulations, according to the PFAS Strategic Roadmap, to confront the human health and environmental risks of PFAS. In October 2023, the Agency finalized two new rules to improve reporting on PFAS. This January, EPA finalized a rule to prevent inactive PFAS from reentering commerce and added seven additional PFAS to Toxics Release Inventory (TRI) reporting. The Food and Drug Administration (FDA) is further working to understand and limit PFAS in food and food packaging.
Guidance: It is important for facilities to have a good understanding of PFAS and PFAS-containing chemicals used onsite, as reporting requirements now apply regardless of the quantity used. Implementing a chemical inventory management system that documents and manages PFAS data can make reporting more efficient and help ensure the facility meets these new requirements. Proper usage strategies, a comprehensive environmental management system (EMS), and a forward-thinking Emergency Response Plan will also remain vital tools for companies potentially dealing with PFAS to effectively manage the associated risks.
Environmental Justice (EJ)
The focus on EJ remains a top priority for the Biden Administration. In November 2023, EPA announced the largest single investment in EJ history, funded by President Biden’s Inflation Reduction Act. The Community Change Grants build on Biden’s Justice40 Initiative and will provide approximately $2 billion in funding for community-driven projects that deploy clean energy, strengthen climate resilience, and build capacity to manage environmental and climate justice challenges. EPA also launched the EJ Thriving Communities Grantmaking Program to expand its technical assistance and project grants for communities, as well as the EJScreen screening and mapping tool, which provides EPA with a consistent approach for combining environmental and demographic socioeconomic indicators.
Guidance: Take the time to understand the communities where you operate—be informed, be prepared, and be proactive. Establish organization priorities and goals and commit the appropriate resources to address EJ concerns. With EPA focused on more regulations, more enforcement, and improved climate change and EJ, environmental management needs to play an integral role in company strategy.
Chemical Safety
EPA is working to strengthen chemical safety with the long-awaited implementation of the 2016 amendments to the Toxic Substances Control Act (TSCA). In addition, the Agency has advanced rules to better protect communities from harmful chemicals like TCE and methylene chloride. These rulemakings align with Goal 7 of the FY 2022-2026 EPA Strategic Plan to ensure the safety of chemicals for people and the environment.
Guidance: Facilities need to have a good understanding of chemicals used onsite so they can take action now to phase out any regulated chemicals (e.g., TCE), as the phaseout period will be quick. Take an inventory of onsite chemicals to determine what chemicals the facility manufactures, distributes, and/or uses. For many chemicals, safer alternatives may be available to eliminate the use of banned chemicals. Be aware of compliance deadlines as you make the transition.
Other Issues to Watch
The following OSHA issues also ones to watch in 2024:
- OSHA Hazard Communications Standard (HCS): In 2021, OSHA proposed to modify the HCS to maintain conformity with the United Nations Globally Harmonized System (GHS) revision 7, align certain provisions with Canadian and other U.S. agencies, and address issues with the 2012 HCS. The proposed updates are intended to increase worker protections and reduce the incidence of chemical-related occupational illnesses and injuries by improving the information on labels and safety data sheets (SDS) for hazardous chemicals. The Agency expects to release finalized changes to the HCS in early 2024.
- OSHA Emergency Response Standard: OSHA has released an unofficial version of its new Emergency Response Proposed Rule and anticipates publication in the Federal Register in January 2024. The proposed rule would replace OSHA’s existing Fire Brigades Standard (29 CFR 1910.156), which covers only a subset of emergency responders. The proposed Rule provides basic workplace protection for workers who respond to emergencies as part of their regularly assigned duties (e.g., fire departments, emergency medical service, and technical search and rescue).
- OSHA National Emphasis Program (NEP) on Warehousing and Distribution Center Operations: Effective July 13, 2023, OSHA announced an NEP for inspections at warehousing and distribution centers, mail/postal processing and distribution centers, and other high-risk retail establishments. The comprehensive safety inspections will focus on workplace hazards common to those industries, including powered industrial vehicle operations, material handling/storage, walking-working surfaces, means of egress, and fire protection.
Set Your Goals for 2024
There is a common need across industry to manage emerging EHS risks with solutions that also provide transparency, security, and sustainability. Heightened EPA enforcement, new OSHA reporting requirements, and pending SEC requirements for ESG are necessitating solutions to help manage business and EHS requirements—and that will continue in 2024.
KTL suggests completing the following early in 2024:
- Get senior leadership commitment. Even with the best EHS personnel, the organization and its EHS system will only be as good as the top leadership and what is important to them.
- Conduct a comprehensive gap assessment to ensure you are meeting the requirements of all applicable EHS regulations, particularly given new environmental, health and safety, and ESG requirements. Think critically about what you have and how overlapping requirements may apply (e.g., your chemical inventory may uncover requirements for air permitting, waste management, Tier II report, etc.). This assessment should be the starting place for understanding your regulatory obligations and current compliance status.
- Seek third-party oversight. Having external experts periodically look inside your company provides an objective view of operations, helps you to prepare for audits, and allows you to implement corrective/preventive actions that ensure compliance. An outside expert can often provide the “big picture” view of what you have vs. what you need; how your plans, programs, and requirements intersect; and how you can best comply.
- Create an integrated management system (e.g., ISO 9001/14001/45001) by finding commonalities between the standards and leveraging pieces of each to develop a reliable system that works for your organization.
- Leverage IT solutions—whether to inventory chemicals and GHG emissions, track OSHA performance, or manage compliance requirements. Technology advancements can help create significant business efficiencies.
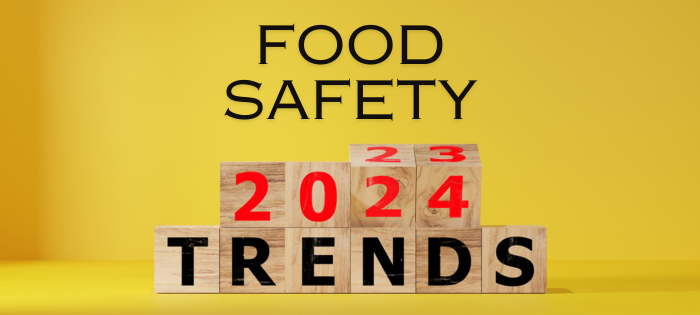
Comments: No Comments
Food Safety: 2024 Trends on Tap
Every year, we see a number of food safety trends rise to the surface that have the potential to impact companies across the food manufacturing and packaging industries. Some challenges and opportunities in food safety remain ongoing; some are just gaining traction with impacts yet to be known. Regardless, the start of a new year provides the opportunity to plan for food safety issues and trends on the horizon and prioritize efforts to ensure ongoing compliance.
Here are some of the top food safety trends KTL is keeping watch on in 2024—and some guidance to help you as you set your food safety strategy for the new year.
Product Reformulations
In November 2023, California became the first state in the U.S. to ban four food additives in foods sold in California through the California Food Safety Act. These additives—Red No. 3, brominated vegetable oil, potassium bromate, and propylparaben, have been linked to an array of diseases, including cancer. The rulemaking will require companies to tweak their recipes to offer products with healthier ingredients by the Act’s 2027 compliance deadline.
On the heels of California’s action, the Food and Drug Administration (FDA) is also reevaluating the use of additives, such as Red No. 3 and brominated vegetable oil. In addition, New York proposed a Bill for a similar statewide ban earlier in 2023.
Guidance: Several top brands, including Coke, Pepsi, Dunkin’ Donuts, and Panera, have taken the lead in voluntarily pulling these additives. Companies who produce foods that commonly use these additives (e.g., candy, fruit juices, packaged baked goods, and more) should be prepared for pending state and federal legislation. It is important to inventory all ingredients and to start adjusting and testing new recipes with healthier alternatives to ensure products do not have to be pulled from the shelves when compliance deadlines hit.
Food Safety Culture
Food safety culture continues to garner attention across the food industry, as it is being integrated more completely and significantly into the Global Food Safety Initiative (GFSI)-benchmarked food safety certification standards, including SQF, BRCGS, and, most recently, FSSC 22000. In fact, FSSC 22000 Version 6.0 incorporates both food safety and quality culture, requiring senior management to “establish, implement, and maintain a food safety and quality culture objective as part of the management system.” Organizations must develop and implement a documented Food Safety and Quality Culture Plan that outlines objectives and timelines and follows the management system process of continuous improvement.
Guidance: Shifting culture is a complex process that requires not just developing a Plan, but truly implementing it. Developing a robust food safety culture requires addressing how people work and what they believe. Senior leadership must prioritize food safety and quality to help create awareness, understanding, and ownership of the organization’s shared beliefs and values. Implementing robust food safety management systems (FSMS) can further help ensure consistent commitment, communication, procedures, training, performance measurement, and trust.
Food Loss and Food Waste
Wasted food makes up the largest percentage—over 20%—of any one material sent to landfills and incinerators each year in the U.S., and 58% of methane emissions released to the atmosphere from landfills are from food waste. In December 2023, the FDA, U.S. Department of Agriculture (USDA), and Environmental Protection Agency (EPA) published a Draft National Strategy for Reducing Food Loss and Waste and Recycling Organics. The Strategy defines four objectives and associated actions to meet the National Food Loss and Waste Reduction Goal of reducing food waste by 50% by 2030.
Efforts are also underway at the state level. As recent examples, New Jersey published its Recycled Content Law requiring manufacturers to meet minimum recycled content requirements for regulated containers and packaging products sold or offered for sale in New Jersey beginning on January 18, 2024. In addition, California Senate Bill 1383 further mandates a 75% reduction in organic waste disposal and requires that not less than 20% of edible food that is currently disposed be recovered for human consumption by 2025.
Guidance: GFSI standards like FSSC 22000 are now requiring organizations to develop a documented policy with objectives and detailed strategy to reduce food loss and waste within the organization and the related supply chain. A thorough food and packaging assessment serves as the foundation for these reduction efforts. Having this general understanding can help identify appropriate strategies to avoid waste, cut down on disposal costs, reduce over-purchasing and labor costs, reduce water and energy use associated with food production, and reduce greenhouse gas (GHG) emissions.
Food Traceability
The focus on supply chain management and food traceability remains a concern as companies prepare to meet the requirements of FDA’s Food Traceability Rule by January 2025. Significant efforts and investments are being made to improve traceability recordkeeping to create standardization, stronger linkages throughout the supply chain, enhanced communication, and faster response.
Guidance: Having a good document/records management system will be essential for maintaining the vast number of documents required by the Food Traceability Rule. Such a system can help ensure process and document standardization; central and secure storage, organization, and access to documents and records; enhanced workflows for approving and completing tasks involving documents; and easy access to documents for audits and clear audit trail.
Bioengineered Foods
In April 2023, FDA issued a letter to developers and manufacturers who intend to transfer genes for proteins that are known food allergens into new plant varieties for foods. The letter serves as an important reminder that developers of these new plant varieties are obligated to 1) make sure the products they market are safe for consumers; and 2) implement all measures needed to comply with the Food, Drug, and Cosmetic (FD&C) Act. If not appropriately managed, the development of these plants could result in the presence of an unexpected allergen in the bioengineered food product. And if an unexpected allergen enters the food supply, there is real risk of a severe or even life-threatening allergic reaction and, subsequently, needing to recall affected products.
Guidance: The FDA is asking developers to consider the food safety risks posed by such allergens and to plan early in development to manage those risks. Developers who intend to create these plant varieties using proteins that are food allergens need to develop a robust risk management plan that includes significantly stronger mitigation strategies and practices (e.g., crop segregation) to provide assurance that foods containing the transferred allergen are not mixed with other foods, as well as proper labeling to declare the presence of allergens.
CBD and FDA
The FDA issued a decision on January 26, 2023, concluding that “a new regulatory pathway for CBD is needed that balances individuals’ desire for access to CBD products with the regulatory oversight needed to manage risks.” FDA is concerned with the growing number of products containing CBD that are being marketed for therapeutic or medical uses without FDA approval. The Agency has sent warning letters to companies illegally selling CBD products that claim to “prevent, diagnose, treat, or cure serious diseases,” as well as to companies that sell CBD-infused food and beverages (e.g., cookies, gummies, etc.). Until a regulatory framework is established, FDA will continue to act against CBD and other cannabis-derived products to protect the public.
Guidance: Companies getting involved in this growing industry need to stay on top of the rapidly changing regulatory environment. Take the time now to assess operations, determine what emerging standards might be appropriate, identify gaps in existing programs, prepare for a new regulatory framework—state and/or federal—and begin implementing solutions to eliminate risks.
Tech Solutions
There is a common need across the food industry to manage emerging risks with solutions that also provide transparency, security, and sustainability. The recent heightened enforcement of the Foreign Supplier Verification Program (FSVP), traceability regulations, and food security concerns are pushing requirements down the supply chain and testing the entire supply chain management system. More food companies are relying on technology solutions to help manage these businesses and food safety requirements—and that will continue in 2024. Artificial Intelligence (AI) is still emerging as a business tool and could have significant impacts on how companies do business in the future.
Guidance: Having a simple, centralized FSMS to manage, track, communicate, and report compliance program information can enable staff to complete required tasks, improve compliance performance, and support operational decision-making. Companies can and should leverage existing information technology (IT) solutions to create compliance efficiencies. A well-designed and executed compliance information management system brings IT and management systems together to coordinate, organize, control, analyze, and visualize information in such a way that helps organizations remain in compliance and operate efficiently.
Other Regulatory Issues to Watch
The following Acts are all ones to watch in 2024:
- Food Labeling Modernization Act of 2023 would align labeling regulations with the latest nutrition science and advance national public health priorities through food labeling policies. The Act would require FDA to establish a standard front-of-package nutrition labeling system for all the packaged foods it regulates.
- No Toxics in Food Packaging Act of 2023 aims to prohibit certain harmful chemicals, including ortho-phthalates, PFAS, bisphenol A, styrene, and antimony trioxide, from being used in food packaging due to their cancer-causing and hormone-disrupting effects.
- Food Chemical Reassessment Act of 2023 proposes the creation of a new office within the Center of Food Safety and Applied Nutrition. The Office of Food Safety Food Assessment would reassess the safety of food additives and food contact substances.
- Transparency, Readability, Understandability, Truth, and Helpfulness (TRUTH) in Labeling Act of 2023 would require FDA to develop new front-of-package labels for foods and beverages to improve consumer access to health information.
Set Your Goals for 2024
With these challenges simultaneously competing for attention—and with fewer resources to manage it all—companies need to assess priorities, needs, and requirements and create a plan for how to meet them. KTL suggests completing the following early in 2024:
- Get senior leadership commitment and invest in creating a food safety culture that prioritizes food safety and quality.
- Understand current and pending regulatory and certification requirements and their applicability to your company. Know your operations, inventory your ingredients, understand your supply chain, quantify your food waste. All of this is necessary to help ensure compliance and sustainability.
- Seek third-party oversight. Having external experts periodically look inside your company provides an objective view of what is really going on, helps you to prepare for audits, and allows you to implement corrective/preventive actions that ensure compliance.
- Leverage IT solutions to streamline compliance, manage certification requirements, create transparency, and ensure business efficiencies.
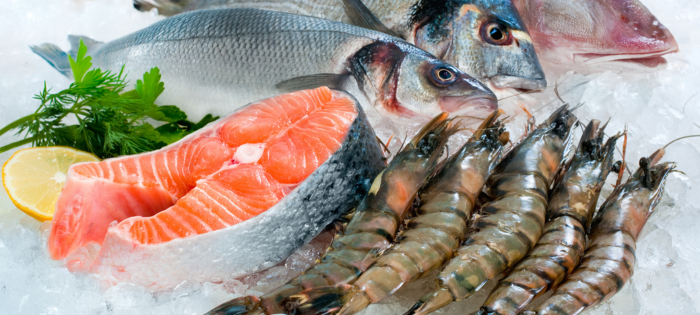
Comments: No Comments
Food Fraud and Fish: New Guidance
Food fraud—also known as economically motivated adulteration (EMA)—occurs when someone intentionally misrepresents a less expensive food product or ingredient for a more expensive one. The Food and Drug Administration (FDA) estimates food fraud impacts about 1% of the food industry worldwide, though this number is likely higher since food fraud can be difficult to detect. Beyond its economic impacts, food fraud can cause significant health issues, ranging from lead poisoning to allergic reactions that may even result in death.
Seafood Fraud
Seafood fraud often happens when a less expensive species of fish is substituted for a more expensive species. For example, wild-caught salmon and shrimp are more expensive than farm-raised (i.e., aquacultured) salmon and shrimp. Producers who swap or mislabel fish to say it is wild caught when it is not can fraudulently earn higher profits at lower cost.
Misbranding such as this clearly results in economic fraud due to the market value of different species of fish. Of more concern, this misbranding may also prevent consumers from correctly identifying what they are eating—and the potential safety hazards associated with certain seafood. These hazards may include allergenic proteins, natural marine toxins, and scombrotoxin formation, which can all present food safety risks if the food is not accurately labeled.
This practice of mislabeling is prohibited under FDA’s Food, Drug, and Cosmetic (FD&C) Act Section 403: Misbranded Food. The Food Safety Modernization Act (FSMA) Intentional Adulteration Rule further requires companies to implement preventive controls to protect against intentional adulteration of human and animal food.
New Industry Guidance
In August 2023, FDA issued new industry guidance, including The Seafood List, to provide more information on the acceptable market, common, scientific, and vernacular names of seafood species sold in the U.S. The intent of this guidance is to:
- Help industry properly label seafood and products containing seafood ingredients with a name that is not false or misleading.
- Facilitate consistency in the U.S. marketplace.
- Reduce confusion among consumers.
In September 2023, in collaboration with the National Oceanic and Atmosphere Administration (NOAA), the National Institute of Standards and Technology (NIST) also announced four new reference materials to help assess the authenticity of seafood and verify where fish is caught or produced. These reference materials specifically address Wild-caught Coho Salmon (RM 8256), Aquacultured Coho Salmon (RM 8257), Wild-caught Shrimp (RM 8258), and Aquacultured Shrimp (RM 8259),
NIST’s reference materials are intended to help regulators and law enforcement agencies differentiate between farmed and wild-caught salmon and shrimp and assess whether imported salmon and shrimp are authentic:
- For shrimp, genetic analysis methods are used to determine the origin of the shrimp, as wild-caught shrimp are a different species than aquacultured shrimp.
- For salmon, scientists analyze the ratio of omega-3 to omega-6 fatty acids. Aquacultured salmon has roughly twice the amount of omega-3 fatty acids compared to wild-caught salmon.
Importantly, these materials can also be used for food safety purposes and detecting allergens, as well as testing for metals and other contaminants. Values for crude protein are provided in the guidance for labs to detect allergens.
According to NIST chemist Benjamin Place, “If a food processing place can use the reference material to say this is the species that it is, then consumers can have more confidence. You now know when you go to a store, you can have full faith the seafood product is the species it says it is and that the labels are true.”
What You Can Do
As always, it is better to take a proactive approach to managing food fraud rather than being caught on the defensive. Facilities should:
- Conduct a vulnerability analysis to identify those areas that pose the greatest risk of food fraud or intentional adulteration.
- Develop and implement a Food Defense Plan to outline risks, mitigation/prevention strategies, monitoring plans, corrective action response, verification activities, and recordkeeping policies.
- Train employees to understand what food fraud is, how to identify fraudulent products specific to their work, and their responsibilities in ensuring food safety by reporting suspicious materials.
- Conduct a mock exercise to assess the effectiveness of the Food Defense Plan and intentional adulteration programs.
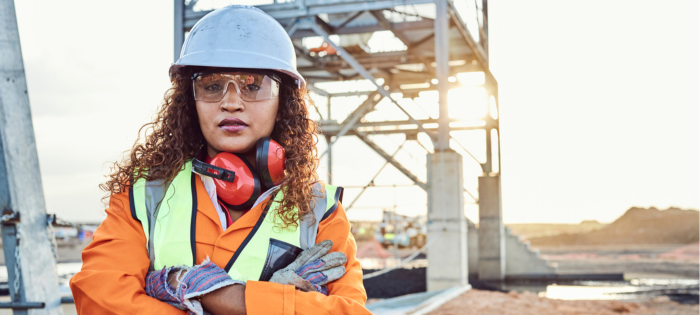
Comments: No Comments
Safety Focus: One Size Does Not Fit All
Women make up nearly 30% of the manufacturing sector and 78% of all healthcare jobs. The number of women working in construction has steadily increased between 2012 and 2020. And yet, a 2019 report from the American Society of Safety Professionals (ASSP) found acquiring properly fitting personal protective equipment (PPE) is still a challenge for this growing segment of over eight million female workers.
Properly fitting PPE is essential in every industry to help ensure workers can complete their tasks safely. And when it comes to PPE, a one-size-fits-all approach does not suffice.
Regulatory Framework
According to the Occupational Safety and Health Administration’s (OSHA) PPE General Requirements Standard (29 CFR 1910.132), all PPE must be designed and constructed for the work to be performed, and employers are required to select PPE that properly fits each affected employee. OSHA guidance specifically states that PPE used by women should be based upon female anthropometric data. (See more below on anthropometry.) OSHA is also in the process of developing a proposed rule that may create more robust standards for employers to ensure all workers receive adequately fitted PPE.
In September 2023, ASSP issued a Technical Report: Guidance of Personal Protective Equipment for Women (registered with ANSI: ASSP TR-Z590.6-2023) to provide guidance for the selection, fit, and use of PPE for women. This ANSI-registered report aims to help employers develop tailored PPE programs and/or adjust their existing PPE programs to account for women workers. The guidance addresses fit issues, selection, assessment, and use of such PPE and outlines anthropometric considerations and sizing for:
- Head
- Face/eyes/mouth
- Body/torso
- Hand
- Foot
Focusing on Anthropometry
According to the National Institute for Occupational Safety and Health (NIOSH), the use of anthropometric data is important to ensure adequate PPE fit. Anthropometry is the science that defines a person’s size, body shape, and functional capabilities. There are intrinsic differences in the shape and size of women’s bodies vs. men’s bodies that require PPE to be tailored differently to fit appropriately—not just be sized down. For example, women tend to have smaller wrists, hands, and feet; shorter arms and legs; and wider hips than men.
PPE has historically been designed and manufactured for men based on outdated anthropometric data collected from the military in the 1950s and 1970s, resulting in poor-fitting PPE for women and other individuals who do not fall into the “average” range. A survey conducted by CSA Group in Canada found that of almost 3,000 women who regularly use PPE on the job, over 80% experience some PPE-related challenges (e.g., improper fit, inadequate selection, or discomfort).
Cause for Concern
If PPE is not correctly fitted to the body, it can cause discomfort and increase the risk of workplace accidents and injuries. According to 2020 U.S. Bureau of Labor Statistics reports, women experience more fatal injury events than men in the category of exposure to harmful substances or environments. This may be attributed to PPE not being adequate to appropriately reduce exposure to harmful substances. The CSA Group survey further found that injuries and incidents related to PPE were reported among 40% of the women.
Using standard PPE in a smaller size that does not consider anthropometry is not a solution. Ill-fitting PPE may prevent the wearer from moving comfortably, hamper productivity, and cause other significant safety hazards. For example:
- Gloves and clothing: If clothing and gloves are too loose, they are more likely to get caught in machinery and equipment, potentially causing amputations or even fatalities. Improperly fitting gloves can also cause the wearer to drop or mishandle items.
- Footwear: Ill-fitting footwear can cause trouble walking/tripping, create blisters, or provide inadequate toe protection. It may even eventually lead to foot deformities over time.
- Eye protection: Bulky or ill-fitting eye protection may leave gaps in protection and could allow debris to enter the eyes.
- Fall protection: Poor fitting PPE used when working from height (e.g., personal fall arrest systems) may not distribute weight evenly and could render such systems ineffective. Improperly sized safety vests and fall harnesses can also increase the severity of fall injuries.
- Respiratory protection: If respirators don’t fit correctly, they could prevent access to clean air and expose workers to respiratory irritants. Bloodborne pathogen exposures could also occur.
When PPE does not fit right, employees may feel inclined to alter their PPE. This can compromise the integrity of the PPE, prevent it from performing as intended, directly impact the employee’s ability to work, and jeopardize the level of protection. Even worse, women just may not opt to wear the ill-fitting PPE, significantly increasing overall accident exposure.
Best Practices
It is crucial that employers provide adequate PPE to all workers to prevent potential safety risks, especially those stemming from wearing ill-fitting PPE. Employers cannot afford to wait for employees to complain about ill-fitting PPE or, worse yet, for an accident to occur. The focus should be on adopting the following best practices to ensure all employees are well protected and productive:
- Review policies and procedures. Employers should regularly assess PPE policies and procedures and revise them, as needed, to comply with current and pending OSHA requirements and industry guidelines.
- Conduct fit testing. Comfort is a major factor with PPE. To encourage usage, PPE must fit comfortably. Employers can ensure this by conducting regular fit testing for employees to ensure the PPE fits and functions as intended.
- Look for better alternatives. Smaller sizes alone do not cut it for PPE. Employers should continually look for alternatives for better PPE that will meet the anthropometric needs of all workers, particularly as new options continually come on the market that are designed specifically for women.
- Promote inclusivity. Recognize that workers may require specific PPE needs based on sex, height, weight, physical abilities, and cultural differences. Addressing the safety needs of all workers goes a long way in creating a more inclusive work environment the values the safety of all employees. The ASSP Guidance provides an excellent resource to help companies consider the anthropometric needs of women when assessing fit. Other PPE options to consider may include maternity PPE, PPE for workers with limb differences, and PPE for workers with cultural or religious needs.
- Train, train, train. Employees need to understand how PPE should fit. They also need to be empowered to speak up if PPE does not fit appropriately to ensure their safety.
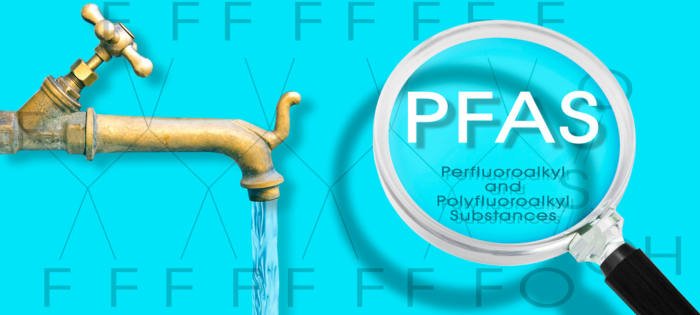
Comments: No Comments
EPA Regulatory Alert: Enhanced PFAS Reporting
Per- and polyfluoroalkyl substances (PFAS) are a group of manmade chemicals that have been manufactured and used in a variety of industries since the 1940s. PFAS are often referred to as “forever chemicals”. They are very persistent in the environment and the human body, where they bioaccumulate in blood and organs over time. Most PFAS exposure comes through ingesting food and water that becomes contaminated with PFAS when it migrates into soil, water, and air during use and/or disposal. Studies show that exposure to PFAS may be linked to harmful health effects in humans and animals.
The Environmental Protection Agency (EPA) has taken a number of actions to tackle PFAS contamination, including the development of a PFAS Strategic Roadmap to confront the human health and environmental risks of PFAS. In October 2023, the Agency finalized two new rules to improve reporting on PFAS.
TRI Reporting Requirements
The Toxic Release Inventory (TRI) tracks the management of certain toxic chemicals that may pose a threat to human health and the environment. U.S. facilities in different industry sectors must report annually how much of each chemical is released to the environment and/or managed through recycling, energy recovery, and treatment.
EPA’s new rule designates PFAS as chemicals of special concern for TRI reporting purposes and, correspondingly, eliminates the exemption that allowed facilities to avoid reporting information on PFAS when those chemicals were in small concentrations (i.e., under 100 pounds). However, PFAS are often used at low concentrations in many products. By removing this exemption, covered industry sectors and federal facilities that use any of the 189 TRI-listed PFAS will have to disclose any quantity of PFAS they manage or release into the environment.
By eliminating the de minimus exemption, EPA will receive more comprehensive data on PFAS, including quantities of chemicals released into the environment or managed as waste, to support more informed decision-making.
TSCA Reporting and Recordkeeping Requirements
EPA also published a final rule under the Toxic Substances Control Act (TSCA) that will require any entity that has manufactured or imported PFAS in any year since 2011 to report information on its uses, production volumes, disposal, exposures, and hazards.
Specifically, these facilities will have 18 months following the effective date of the rule to report the following data to EPA for each PFAS chemical substance or mixture:
- Covered common/trade name, chemical identity, and molecular structure.
- Category(ies) of use.
- Total amount manufactured or processed, amounts for each category of use, and estimates of the respective proposed amounts.
- Descriptions of byproducts resulting from manufacture, processing, use, or disposal.
- Information regarding environmental and health effects.
- Number of individuals exposed and reasonable estimates of the number of individuals who will be exposed in their workplace and the duration of exposure.
- Manner or method of disposal.
This rule is intended to help EPA better characterize the sources and quantities of manufactured PFAS in the U.S. by creating the largest-ever dataset of PFAS manufactured and used in the U.S.
How This Impacts You/What You Need to Do
Federal and state initiatives and regulations to manage PFAS are rapidly growing. KTL does not see the challenges associated with PFAS going away any time soon. If anything, we anticipate more facilities will be directly impacted by mitigation efforts and regulatory action to support EPA’s PFAS Strategic Roadmap, such as those outlined above.
It is important for facilities to have a good understanding of PFAS and PFAS-containing chemicals used onsite, as reporting requirements now apply regardless of the quantity used. Implementing a chemical inventory management system that documents and manages PFAS data can make reporting more efficient and help ensure the facility meets these new requirements. Proper usage strategies, a comprehensive environmental management system (EMS), and a forward-thinking Emergency Response Plan will also remain vital tools for companies potentially dealing with PFAS to effectively manage the associated risks.
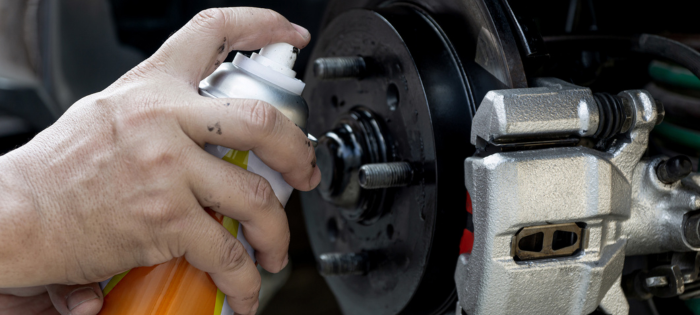
Comments: No Comments
EPA Regulatory Alert: Ban on TCE
Trichloroethylene (TCE) is an extremely toxic chemical used in cleaning and furniture care products, degreasers, brake cleaners, and tire repair sealants, amongst other uses. TCE is commonly found at Superfund sites as a contaminant in soil and groundwater. It is known to cause liver cancer, kidney cancer, and non-Hodgkin’s lymphoma, as well as damage to the central nervous system, immune system, reproductive organs, and fetal health. Environmental and human health risks are present with even very small concentrations of TCE.
Proposed Rule
On October 23, 2023, EPA issued a proposed rule under the Toxic Substances Control Act (TSCA) to ban the manufacture, processing, distribution, and use of TCE to prevent soil and groundwater contamination and protect the public from the associated health risks. This proposal aligns with President Biden’s Cancer Moonshot approach to end cancer and advances the Administration’s commitment to environmental justice.
EPA’s proposed TCE ban would phase out the manufacturing, processing, distribution, and use of TCE over the course of one year. For uses where a longer transition timeframe is necessary (e.g., critical Federal Agency uses, battery separators, manufacture of certain refrigerants), EPA is proposing stringent worker protections to reduce exposure while phasing out TCE.
How This Impacts You/What You Need to Do
It is important for facilities to have a good understanding of chemicals used onsite and to start taking action now to phase out any TCE, as the one-year phaseout period will be quick. Facilities should:
- Inventory Chemicals: Take an inventory of onsite chemicals to determine whether the facility manufactures, distributes, and/or uses any TCE. Consult safety data sheets (SDS) for ingredients. TCE can be referred to as trichlor, trike, or tri and may be sold under a variety of trade names. TCE is identified by its Chemical Abstract Service (CAS) Number: 79-01-6.
- Identify Alternatives: For most uses of TCE as a solvent, safer alternatives are already available. EPA’s Safer Choice Program provides a list of solvents (including degreasers) identified as “safer” alternatives. The University of Massachusetts Toxics Use Reduction Institute (TURI) also has an extensive database of safer alternatives to TCE (and other toxic solvents and cleaners) used for degreasing purposes.
- Make the Transition: The best way to prevent TCE from entering the environment is to eliminate its use in facility operations (i.e., source reduction). Follow EPA’s Pollution Prevention (P2) approach to implement cleaning and degreasing modifications, such as switching to aqueous and less toxic cleaning solvents, adopting other mechanical cleaning techniques, or substituting equipment.
- Dispose Correctly: TCE waste can be characterized in a few ways depending on what it is and how it is used (or not used). TCE waste should be properly characterized and managed at a permitted disposal facility—most likely an incinerator.
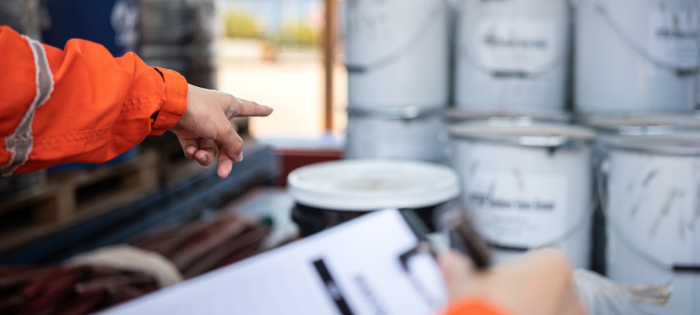
Comments: No Comments
EPA Regulatory Alert: TSCA Risk Evaluation Process
The Environmental Protection Agency’s (EPA) Toxic Substances Control Act (TSCA) (modified in 2016 by the Frank R. Lautenberg Chemical Safety Act) requires EPA to conduct a risk evaluation to determine whether a chemical substance presents an unreasonable risk to health or the environment under the conditions of use.
On October 19, 2023, EPA proposed a new rule to strengthen its process for conducting these risk evaluations under TSCA. The rule is intended to:
- Ensure EPA’s processes better align with the provisions of the law.
- Support more robust evaluations that account for all risks.
- Provide a foundation for protecting workers and communities from toxic chemicals with more protective rules for workers and communities.
TSCA Background
The TSCA inventory is a list of all existing chemical substances manufactured, processed, or imported in the U.S. The current inventory contains 86,718 chemicals, of which 42,242 are active in U.S. commerce. EPA evaluates existing and new chemicals for the inventory:
- Existing chemicals: EPA prioritizes existing chemicals on the list and selects chemicals to determine if the risk is reasonable or unreasonable. If the risk is unreasonable, EPA will impose restrictions to eliminate the risk. The list of ongoing and completed evaluations is available online.
- New chemicals: Any chemical that is not currently on the inventory is considered a “new chemical substance.” Anyone who plans to manufacture or import a new chemical substance for a non-exempt commercial purpose must provide EPA with a Premanufacture Notice (PMN) at least 90 days before initiating the activity. During the notice review period, EPA will review the PMN and determine if the chemical presents unreasonable risk(s) to human health or the environment.
Proposed Provisions
The new proposed rule aims to strengthen EPA’s process for conducting its TSCA chemical risk evaluations. EPA initially finalized a risk evaluation framework rule in 2017; however, it was quickly challenged in Court. The October 2023 proposed rule addresses the Court’s revisions and adds provisions requiring that risk evaluations:
- Consider the disproportionate harms facing overburdened communities, including multiple exposure pathways to the same chemical and combined risks from multiple chemicals.
- Be comprehensive and not exclude conditions of use or exposure pathways.
- Consider risks to workers.
- Use best available science.
- Provide a single determination of whether the chemical presents unreasonable risk, rather than multiple determinations based on individual chemical uses.
- Ensure transparency through updated risk evaluation documents.
- Better align manufacturer-requested risk evaluations with EPA-initiated risk evaluations.
While many of these changes were announced in 2021 and have been incorporated into TSCA risk evaluations over the past two years, they have not been finalized in the Code of Federal Regulations. Doing so will help ensure more certainty regarding the process for conducting TSCA risk evaluations moving forward.
How This Impacts You/What You Need to Do
This rulemaking aligns with Goal 7 of the FY 2022-2026 EPA Strategic Plan to ensure the safety of chemicals for people and the environment. That Plan focuses on strengthening EPA’s ability to successfully implement TSCA with appropriate resources to complete EPA-initiated chemical risk evaluations and risk management actions.
- If you manufacture or import chemicals, determine if the chemical is on the TSCA inventory.
- If you manufacture or import a chemical that is not on the inventory, complete a PMN at least 90 days before initiating the activity.
EPA will conduct a risk evaluation to determine the risk(s) the chemical poses to human health or the environment. Under the proposed rule, these evaluations will be more robust to account for all risks to better protect workers and communities from toxic chemicals.