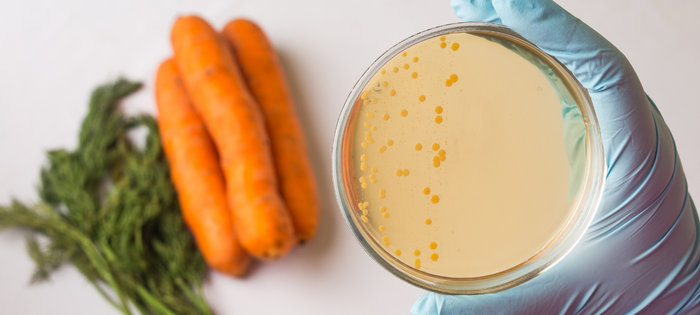
Comments: No Comments
Q&A: Environmental Monitoring for Food Safety
When preparing for compliance and certification audits, environmental monitoring is an area where there are often questions: What are my requirements? How much do I need to do? What happens if I have a deviation? There are many intricacies associated with environmental monitoring that can depend largely on operational processes and compliance and certification requirements—many of which are not always clearly defined. KTL’s food safety experts offer their high-level perspective on some common questions regarding environmental monitoring.
What is environmental monitoring?
Environmental monitoring involves sampling and testing your facility’s environment for pathogens, spoilage and indicator organisms, and allergens to prevent foodborne illness. Environmental monitoring is typically done by swabbing various surfaces for pathogens and sending those samples to an accredited lab for analysis. This monitoring helps to 1) assess how effective the plant’s cleaning and sanitation programs are, and 2) determine whether any pathogens are living in the facility so it can respond accordingly (e.g., adjusting cleaning procedures, addressing personnel hygiene issues, etc.).
What is an Environmental Monitoring Program (EMP)?
An EMP refers to an entire program for organizing the monitoring process to prevent pathogens—and foodborne illness—in finished product. The EMP helps to identify those areas where harmful microorganisms could be harboring in the facility and to implement and verify the effectiveness of pathogen controls (e.g., cleaning and sanitation procedures, sampling frequency and methodology, employee hygiene practices). Ultimately, the purpose of an effective EMP is to help a facility identify and implement strategies to eliminate pathogens and prevent their recurrence.
Who needs an EMP?
Certain foods are considered high risks for harboring pathogens and growing bacteria. These include beef, poultry, dairy, seafood/shellfish, ready-to-eat (RTE) food, baby food, leafy greens, and tree nuts. According to U.S. Public Health Service, the organisms in the table below—and their sources—are the biggest culprits of foodborne illness:
Organism | Sources |
Campylobacter | Raw and undercooked poultry and other meat, raw milk, and untreated water |
Clostridium botulinum | Improperly prepared home-canned foods |
E. coli 0157:H7 | Beef, produce, raw milk, and unpasteurized juices and ciders |
Listeria monocytogenes | Unpasteurized dairy products, sliced deli meats, smoked fish, hot dogs, pate’, and deli-prepared salads |
Norovirus | Any food contaminated by someone who is infected with this virus |
Salmonella | Raw and undercooked eggs, undercooked poultry and meat, fresh fruits and vegetables, and unpasteurized dairy products |
Staphylococcus aureus | Cooked foods high in protein that are held too long at room temperature |
Shigella | Salads, unclean water, and any food handled by someone who is infected with the bacterium |
Toxoplasma gondii | Raw or undercooked pork |
Vibrio vulnificus | Raw or undercooked seafood, particularly shellfish |
The kill step is the point in food manufacturing when dangerous pathogens are removed from the product. This is often done by killing pathogens through processes such as cooking, pasteurization, irradiation, and freezing. It is one of the most important steps in keeping food safe. The following questions can help determine whether an EMP may be necessary for your facility:
- Does your process have a kill step that removes dangerous pathogens from the product?
- Is your product exposed to the environment after the kill step and before packaging?
- Does your product combine RTE products without including a kill step?
Why do I need an EMP?
From a compliance perspective, the Food and Drug Administration’s (FDA) Food Safety Modernization Act (FSMA) Final Rule for Preventive Controls for Human Food requires it: “A facility who has identified a potential environmental pathogen or indicator organism as a hazard to RTE foods is required to include an EMP in its Food Safety Plan. A trained Preventive Controls Qualified Individual (PCQI) needs to review EMP test results to ensure that the Food Safety Plan is being followed.”
From a certification perspective, most Global Food Safety Initiative (GFSI) food safety certification schemes also require an EMP, and failure to have an effective program will result in a major non-conformance.
From a consumer protection perspective, environmental monitoring is intended to protect consumers by keeping harmful bacteria from contaminating the food we eat. An EMP can help serve as an early warning system for identifying a potential contaminant before it spreads throughout the facility and into food that reaches the consumer.
What does an EMP include?
EMP requirements are set forth by FDA and GFSI certification programs, but retailers and consumers may also have their own requirements that impact the food supply chain. According to FDA, a FSMA-compliant EMP should include:
- Established, written, and scientifically valid procedures.
- Identified testing microorganisms, adequate locations, and number of collection sites.
- Identified timing and frequencies for collecting and testing samples.
- Identified corrective action procedures in compliance with CFR 21 section 117.150.
- Testing performed by an accredited laboratory.
An EMP should be tailored to the facility’s specific operations and food products; however, there are several steps that every program should include:
- Perform a risk assessment. Determine the risks associated with the plant’s operations, including identifying high-risk foods and potential pathogens that could be present. The frequency of environmental monitoring will be determined by the hazards and risks identified.
- Determine hygienic zones. An EMP should include sampling to assess activities, pathogens, associated risks, and mitigation options within the following zones (from highest to lowest risk):
- Zone 1: Direct food contact services (e.g., counters, conveyers, utensils).
- Zone 2: Indirect food contact surfaces that are close to food contact surfaces (e.g., crevices of equipment, drip shields).
- Zone 3: Indirect food contact surfaces that are not close to food contact surfaces (e.g., walls, floors, drains).
- Zone 4: Areas distant from food contact surfaces and processing areas (e.g., locker rooms, lunchrooms, offices).
- Implement and manage testing protocols. Testing and sampling protocols should identify the frequency of sampling required (depending on risks), number of samples (depending on the facility size), timing of sampling (before/during/after production), person responsible for conducting sampling, and an accredited lab (ISO 17025) to use for testing, as needed. Some facilities may opt to conduct internal “rapid tests” at interim phases of production by trained staff to provide more immediate and cost-effective results and leave third-party lab testing for the final product. Regardless of whether testing is done internally or by a lab, an effective EMP will swab different sites each time to reduce the likelihood of contamination going undetected.
- Develop corrective action procedures. Sampling is intended to identify high-risk areas. How an establishment responds to any findings—and how quickly—is critical. Potential corrective actions may include changing cleaning chemicals, increasing frequency of cleaning program, requiring uniforms, etc.
- Verify and validate the EMP. Data, programs, and procedures should be regularly reviewed to ensure the EMP is serving its intended purpose. Verification provides proof the EMP is working; validation provides proof it is effective.
What do I do if I have a deviation?
The FDA anticipates that facilities with EMPs will occasionally detect environmental pathogens. If this happens, the facility should immediately enact the corrective actions outlined in the facility’s EMP (see above). This may include modifying cleaning and sanitation procedures, recleaning areas, conducting retesting, holding product, or even issuing a product recall.
It is important for facilities to remember that any environment has the potential to become contaminated with a pathogen. Never having a positive result for a common environmental pathogen might not necessarily mean that the EMP is “perfect;” rather, it might be a sign that the right areas are not being swabbed adequately. Keep in mind that any positive result offers an opportunity to improve the EMP and related cleaning/sanitation/hygiene procedures.
How can I prevent environmental pathogens?
There are a number of key actions food processors can undertake to prevent environmental pathogens from contaminating their facilities and food products:
- Apply Good Manufacturing Practices (GMPs). GMPs apply to EMPs, as with every other aspect of a strong food safety program. GMPs that will impact environmental monitoring results include employee hygiene practices, sanitary facility and equipment design, and cleaning and sanitation processes.
- Evaluate, implement, and verify preventive controls. Identify your greatest risks for environmental pathogens, and proactively develop strategies to implement controls in your process flow. These may include controlling pedestrian walkways to avoid personnel contamination; using dedicated tools, equipment, and/or staff post-process; having special uniforms for staff, etc. Just as important, you must verify the performance of your preventive controls through environmental monitoring and take corrective action immediately if problems arise.
- Ensure employees and other resources are qualified. Employees responsible for sanitation, sampling, and overseeing the EMP must have the necessary training and/or experience for assigned duties. In addition, any outside labs used for environmental testing must be accredited under ISO 17025.
- Review and update the EMP. Products, operations, equipment, employees, processes, and other environmental factors change—and all of these can impact the EMP. Conducting periodic reviews to ensure processes and procedures reflect any new conditions is important in ensuring a facility’s overall hygiene and its products’ quality and safety.
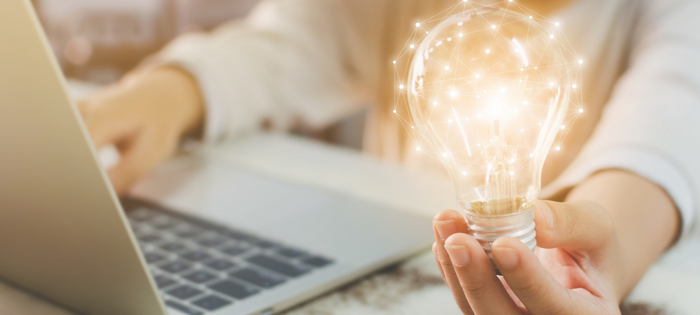
Comments: No Comments
Q&A with KTL’s Certified Energy Manager (CEM)
According to the International Energy Agency (IEA)’s World Energy Outlook 2022, “The world is in the midst of the first truly global energy crisis, with impacts that will be felt for years to come” due to energy shortfalls and high prices of natural gas and coal—much related to Russia’s invasion of Ukraine. The Outlook further states that advanced economies/governments have committed well over $500 billion to protect consumers, but the key takeaway from IEA is clear: “Today’s energy shock is a reminder of the fragility and unsustainability of our current energy system.”
Greater energy efficiency is a key part of the solution—and not just at a federal level. With significant government policies and pledges to achieve a NetZero Economy by 2050, organizations large and small need to be thinking about energy management. What does this mean? KTL Senior Consultant and Certified Energy Manager (CEM) Coulter Wood answers a few questions to offer some insight.
What is energy management?
Energy management involves monitoring and controlling energy consumption across an organization to save energy and, subsequently, save money. Energy management should be part of the overall strategy of a company, with the ultimate objective of reducing the cost of energy (i.e., creating energy efficiencies) without impacting work processes or products.
The energy management process involves four key steps:
- Collect and analyze energy usage data. The more data—and the more detailed it is—the easier it is to identify energy waste within operations. Often, your local utility or energy provider is a good source for this type of data.
- Identify opportunities to improve energy efficiency and optimize energy usage. The easiest and most cost-effective energy-saving opportunities often require little capital investment.
- Implement energy optimization solutions. Gaining cross-functional support is key to realizing a return on investment.
- Track and monitor progress/results through an established “measurement and verification” process. Demonstrate results to garner additional support, adjust solutions, as needed, and repeat.
Why should companies be concerned with energy management?
Sound energy management practices can have many benefits to organizations:
- Reduce costs: The Carbon Trust estimates that most businesses can cut their energy costs by at least 10% (often by 20%) with simple actions that offer a quick return on investment. Operating more efficiently reduces energy consumption, which equates to significant savings on utility bills. This is particularly important as energy costs reach all-time highs.
- Reduce carbon emissions: The equation is simple: the less energy you use, the fewer carbon emissions you produce.
- Reduce risk: Organizations that consume significant amounts of energy are at greater risk of being impacted by energy price increases or supply shortages. When an organization can reduce its demand for energy, it also reduces the risks associated with an energy shortage. Having greater control over energy consumption creates resiliency against energy price fluctuations.
How does energy management relate to sustainability?
On a global level, energy consumption is the major contributor to climate change, making up nearly 60% of the world’s greenhouse gas (GHG) emissions. Consuming less energy, finding more energy efficient solutions, and/or using alternate renewable energy sources help to reduce energy consumption, reduce carbon emissions, reduce dependence on fossil fuels, and reduce the damage being done to the planet. This ties directly to sustainability goals, including carbon neutral incentives, and helps promote a strong environmental, social, and governance (ESG) image.
What about ISO 50001?
As part of the ISO family of management system standards, ISO 50001:2018 focuses on Energy Management Systems as a strategic tool to help organizations better manage their energy use and:
- Improve productivity.
- Reduce environmental impact.
- Enhance corporate reputation.
- Drive down costs.
- Improve competitiveness.
According to ISO, “ISO 50001 is designed to help organizations improve energy performance by making better use of its energy-intensive assets.” Like other ISO standards, ISO 50001 follows the plan-do-check-act (PDCA) process for continual improvement. This involves:
- Developing and implementing an energy policy.
- Setting achievable targets for energy use.
- Designing action plans to reach objectives (e.g., implementing energy-efficient technologies, reducing energy waste, improving current processes to cut energy costs).
- Measuring progress.
How do I get started?
Energy monitoring is a key first step in effective energy management, as it allows organizations to understand their energy consumption patterns and identify routine waste in the process. A basic initial action is to work with a CEM to review and analyze your utility bill (a 12-month history is ideal). This action alone can offer significant insights into how your organization consumes energy and what opportunities may exist for immediate savings.
Once you have a comprehensive understanding of how energy is being consumed, it becomes possible to identify inefficiencies and opportunities for improvement, whether related to behavior (e.g., asking employees to turn off lights every night), technology (e.g., implementing integrated building management systems), or process (e.g., increasing operations during off-peak hours).
KTL has experience reviewing utility bills and helping organizations of all sizes identify energy consumption patterns and energy efficiency solutions. Please contact us for assistance in meeting your energy, environmental, and sustainability objectives.
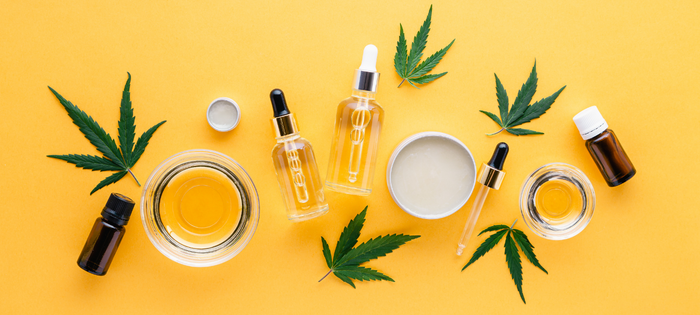
Comments: No Comments
One to Watch: FDA and CBD
With a rapidly growing market, pending regulatory action related to marketing cannabidiol (CBD) products is certainly an issue to watch. And the Food and Drug Administration (FDA) set the tone for 2023, issuing a decision on January 26, 2023, concluding that existing regulatory frameworks for food and dietary supplements are not appropriate for regulating CBD. Rather, the FDA press release states, “A new regulatory pathway for CBD is needed that balances individuals’ desire for access to CBD products with the regulatory oversight needed to manage risks.”
Regulating CBD Products
Products containing cannabis or cannabis-derived compounds are subject to the same requirements as FDA-regulated products containing any other substance. FDA has currently approved only one cannabis-derived and three cannabis-related drug products, all of which are only available with a prescription from a licensed healthcare provider. There are no other FDA-approved drug products that contain CBD. In addition, there are currently three generally recognized as safe (GRAS) notices for the following hemp seed-derived food ingredients: hulled hemp seed, hemp seed protein powder, and hemp seed oil.
While the FDA recognizes the potential therapeutic benefits CBD could offer, the agency is committed to following the drug approval process to help ensure the safety and efficacy of any products derived from cannabis. The use of CBD in dietary supplements and food (both human and animal) raises a variety of safety concerns for the FDA—especially associated with long-term use and vulnerable populations (e.g., children, pregnant women)—that are not fully understood. As a result, the FDA’s internal working group concluded that “it is not apparent how CBD products could meet the safety standards for dietary supplements or food additives”:
- Dietary Supplements. CBD products are excluded from the dietary supplement definition under section 201(ff)(3)(B) of the Food, Drug & Cosmetic (FD&C) Act [21 U.S.C. § 321(ff)(3)(B)]. This exclusion applies unless the FDA issues a regulation finding that the product would be lawful under the FD&C Act. To date, no such regulation has been issued for any CBD substance. All products that are marketed as dietary supplements must then comply with the regulations governing dietary supplement products, including current Good Manufacturing Practices (cGMPs) and labeling.
- Human and Animal Food Additives. It is a prohibited act to introduce or deliver for introduction into interstate commerce any food (i.e., human or animal) to which CBD has been added under FD&C Act [21 U.S.C. § 331(ll)].
Warning Letters
The FDA is concerned with the growing number of products containing CBD that are being marketed for therapeutic or medical uses without FDA approval. The agency has sent warning letters to companies illegally selling CBD products that claim to “prevent, diagnose, treat, or cure serious diseases,” as well as to companies that sell CBD-infused food and beverages (e.g., cookies, gummies, etc.). Until a regulatory framework is established, FDA will continue to act against CBD and other cannabis-derived products to protect the public.
New Regulatory Pathway
The FDA believes there is currently not adequate evidence to determine how much CBD can be consumed and for how long before causing harm, and the agency’s existing foods and dietary supplement authorities provide only limited tools for managing the potential risks associated with CBD products. As such, a new regulatory pathway would “benefit consumers by providing safeguards and oversight to manage and minimize risks related to CBD products for humans and animals.”
Risk management tools could include:
- cGMPs
- Clear labeling on products
- Prevention of contaminants
- CBD content limits
- Measures to mitigate the risks of ingestion by children (e.g., minimum purchase age)
Many states are trying to close the gap the best they can by putting some regulations in place, but this is currently being done piecemeal. In addition, several organizations have launched cannabis standards and certifications—often based on the Global Food Safety Initiative (GFSI) and cGMPs—to improve the overall safety and quality of cannabis and cannabis-infused products in the market.
Companies getting involved in this growing industry need to stay on top of the rapidly changing regulatory environment. Take the time now to assess operations, determine what standards might be appropriate, identify gaps in existing programs, prepare for a new regulatory framework—state and/or federal—and begin implementing solutions to eliminate risks.
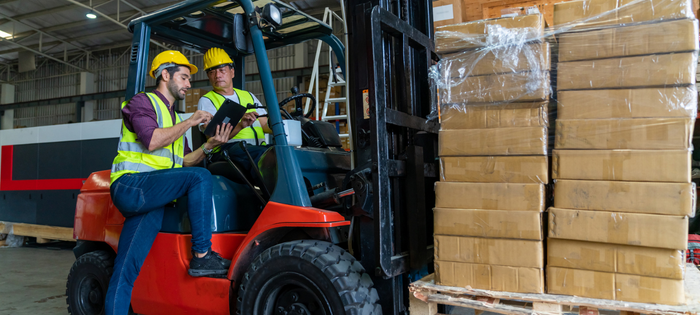
Tech Corner: Forklift Pre-Op Inspection Form
Functionality: What does it do?
A pre-operation forklift inspection is used by forklift operators to conduct safety and maintenance checks prior to operation. The intent of the inspection is to reduce the likelihood of avoidable injuries caused by forklifts. Typically, these inspections are done via paper forms. The KTL forklift inspection tool creates a mobile form for electronic data collection in the plant/field. Inspection data is submitted directly to the system and can then be further analyzed through dashboards to identify concerns and trends. Notifications for identified issues and program compliance can also be configured to create greater visibility of the forklift safety program.
Benefits: Why do you need it?
- Data can be submitted directly and immediately for review with no manual data entry required.
- Data is stored for future analysis and improvements.
- Issues with forklifts can be identified quickly and assigned to relevant people for resolution.
- Program compliance is tracked in real time.
Technology Used
- Power Automate
- Power Apps or alternative
- Power BI
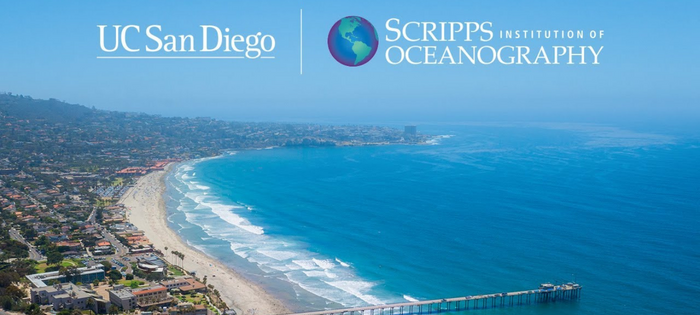
Comments: No Comments
Joe Tell Appointed to Scripps Institution of Oceanography Director’s Council
KTL Principal Joe Tell was recently appointed to the Director’s Council of the Scripps Institution of Oceanography at University of California (UC) San Diego. Scripps is one of the most important centers for global earth science research and education in the world.
Director’s Council members are leaders in business, government, philanthropy, or the nonprofit sector. The Council meets formally twice per year to review the institution’s progress and to advise the Director in strategic planning for priorities, new directions, and high-level outreach.
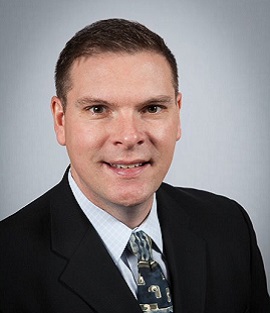
Joe brings over 25 years of experience working with industrial, government, and institutional clients in operational and business risk management, process improvement, information management systems, and compliance assurance to his Director’s Council position. His expertise is focused on creating strategies for developing and implementing risk-based management systems that sustain the environment and public health, emphasize strong leadership commitment, and ensure cross-functional stakeholder engagement. Joe is particularly interested in making connections between the private sector, government agencies, and the NGO community to promote collaborative solutions to global environmental and health issues.
Scripps was founded as the Marine Biological Association of San Diego in 1903. The Institution leads research in climate change impacts and adaptation, resilience to hazards, conservation and biodiversity, oceans and human health, national security, and innovative technology to observe the planet.
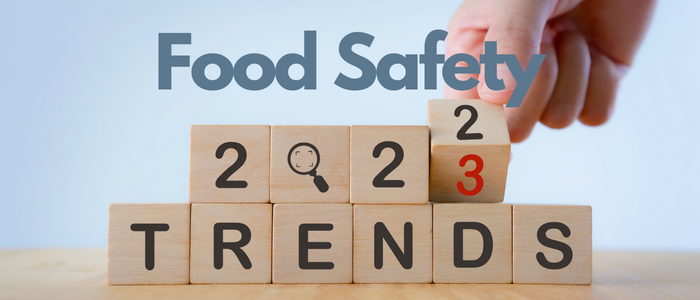
Comments: No Comments
Food Safety Trends to Watch in 2023
A November 29, 2022, reader poll conducted by Quality Assurance & Food Safety Magazine identified the following top food safety concerns for 2023: 25% recalls, 25% traceability, 25% supplier/supply chain issues, 12% labor shortages, 12% something else.
Over the past few years, KTL has seen many of these concerns—and others—present challenges across the food industry. We also recognize the opportunity some of these present when appropriately and proactively addressed. Here are some of the top food safety trends KTL is tracking in 2023—and some guidance to help you as you establish your food safety priorities.
Resource Constraints and Technology Solutions
Not surprisingly, one of the biggest challenges we have witnessed our clients grappling with is related to staffing, from turnover in the quality department to being understaffed in production. Employees are stretched thin and are carrying more responsibilities that they aren’t necessarily qualified to do, including food safety. Achieving and maintaining food safety compliance and Global Food Safety Initiative (GFSI) certification requires great management and expertise to ensure all aspects of a company’s technical compliance have been identified and are being actively handled. KTL has been working with more and more food safety and quality departments to fill these gaps—either with outsourced personnel or compliance efficiency tools—as companies look to recruit food safety staff.
Guidance:
- Invest in food safety training and education for all staff and start with the basics. Even experienced workers can benefit from refresher training to correct bad habits and build efficiencies.
- Develop a relationship with someone you trust to do things in your best interest. Use them to assess your operations, help you understand what regulations apply, identify gaps in your programs, and implement solutions to eliminate risks. Rely on them as a part of your team.
- Employ information technology (IT) solutions to create compliance efficiencies. A well-designed and executed compliance information management system brings IT and management systems together to coordinate, organize, control, analyze, and visualize information in such a way that helps organizations remain in compliance and operate efficiently.
- Build a better food safety culture starting at the top and focusing on the details (see below).
Food Traceability
Without a doubt, food traceability is a hot topic with the Food and Drug Administration (FDA) publishing the Final Food Traceability Rule in November 2022. While the agency has had previous food traceability requirements, the new rule under FSMA Section 204(d) is intended to enhance traceability recordkeeping for certain identified foods beyond a limited “one-up, one-back” traceback approach—creating standardization, stronger linkages throughout the supply chain, improved communication and recordkeeping, and faster response. The compliance date for all entities subject to the updated recordkeeping requirements is January 21, 2025.
Guidance:
- The rule is complicated with unanswered questions about recordkeeping and FDA enforcement. Do what you can to understand your requirements. Review the Food Traceability List (FTL) and start building systems and processes now that address requirements for traceability lot codes, critical tracking events (CTEs), key data elements (KDEs), and recordkeeping.
- Having a good document/records management system will be essential for maintaining the vast number of documents required by the Food Traceability Rule. Such a system can help ensure process and document standardization; central and secure storage, organization, and access to documents and records; enhanced workflows for approving and completing tasks involving documents; and easy access to documents for audits and clear audit trail.
Food Safety Culture
Food safety culture continues to garner attention and visibility across the food industry, as it is being integrated more completely and significantly into many of the GFSI-benchmarked food safety certification standards. For example, BRCGS Issue 9, which was launched on August 1, 2022, emphasizes two core themes: building core competencies and developing food safety culture. These actions are creating defined requirements, timelines, and measurements to create a culture that embraces food safety.
Guidance:
- Get senior leadership commitment in prioritizing food safety and quality.
- Assess current food safety program elements, identify improvements that are internally desirable and required, and implement those updates that will create a strong food safety culture.
- Put robust systems in place to ensure consistent commitment, communication, procedures, training, performance measurement, and trust.
Environmental Focus
Food companies continue to see regulatory bodies—beyond FDA and USDA—taking much more interest in them. U.S. Environmental Protection Agency (EPA) multi-media inspections, enforcement actions, and large penalties for violations persist. EPA’s proposed Safer Communities by Chemical Accident Prevention (SCCAP) rule, which is intended to strengthen current Risk Management Plan (RMP) regulations, has the potential to create significant industry requirements in the future. Facilities that use anhydrous ammonia as refrigerant may be particularly vulnerable. In addition, EPA is investing resources in addressing per- and polyfluoroalkyl substances (PFAS) contamination. Many manufacturers, especially those in the food and beverage industry, are facing new concerns about whether and how to test for and remediate PFAS contamination.
Guidance:
- Evaluate your current environmental risk level and develop strategies to minimize risks to the extent possible. Proper usage strategies, a comprehensive environmental management system (EMS), and a forward-thinking Emergency Response Plan will remain vital tools for companies to effectively manage the associated risks
- Outline steps to improve performance and safe operations, including defining organizational roles and responsibilities.
- Streamline compliance methods and improve operational efficiencies by implementing IT solutions and compliance management systems that coordinate, organize, control, analyze, and visualize information.
Food Recalls
FDA took another step toward reducing the public’s exposure to the risks of foodborne illness on March 3, 2022, issuing its final guidance for voluntary recalls: Initiation of Voluntary Recalls Under 21 CFR Part 7, Subpart C. FDA’s guidance outlines the steps companies should take before a recall is mandated, including developing policies and procedures, establishing training, maintaining records, and initiating communications.
Guidance:
- Establish recall initiation procedures. Prepare, maintain, and document written procedures for initiating a recall to minimize delays and uncertainty when/if a voluntary recall becomes necessary.
- Identify and train appropriate personnel (and alternates) on recall-related responsibilities. The recall team should have a thorough understanding of recall procedures and their respective roles in carrying out a recall plan. Regular training, including mock recalls, helps ensure competency.
- Establish a recall communications plan to address communications with employees, FDA, supply chain, direct accounts, and the public, as necessary. Identify key contacts and develop draft templates that can be easily customized and distributed when needed.
Food Investments
We continue to see private equity firms investing heavily in food companies and, subsequently, in their food safety infrastructure. Any merger and acquisition (M&A) transaction, no matter the size or structure, can have a significant impact on the acquiring company—and food safety is a critical factor. Undertaking adequate due diligence is vital. It can lead to the discovery of regulatory inconsistencies that may lessen the value of an entire product line or business—and opportunities to make improvements. It can provide better insights into the risks and potential benefits of a transaction that will ensure a smoother, more effective, and sustainable business integration.
Guidance:
An assessment of the operations, production processes, equipment conditions, food safety management, quality, regulatory compliance, and all related documentation needs to be completed as part of any food-related acquisition. Prior to any acquisition, it is important to determine:
- Condition of operations (i.e., personnel, equipment, processes, facility) necessary to effectively meet existing performance standards.
- Level of food safety compliance to regulatory requirements and applicable voluntary industry certifications.
- Any potential high-level risks that would impact the transaction.
Cannabis
FDA is watching! The agency issued a number of warning letters in 2022 to companies that sell CBD-infused food and beverages and seems particularly concerned about food products that may appeal to children (e.g., cookies, gummies, etc.). While the regulatory framework for managing cannabis production is still unclear, this is a rapidly growing market, and we anticipate progress—whether at the state level or federal level—in the development and implementation of regulations and controls (e.g., Good Manufacturing Practices (GMPs), labeling requirements, etc.).
Guidance:
Several organizations have launched cannabis standards and certifications—often based on GFSI and GMPs—to improve the overall safety and quality of cannabis and cannabis-infused products in the market. Those getting involved in this rapidly growing industry need to assess operations, determine what standards might be appropriate, identify gaps in existing programs, prepare for potential regulatory action and/or certification opportunities, and implement solutions to eliminate risks.
Sustainable Food Management
According to a January 2023 article in Food Logistics Magazine, “By 2050, the Food and Agriculture Organization (FAO) estimates we will need to produce 60% more food to feed a world population reaching nearly 10 billion. Even if we hit that mark, 300 million people will still be grappling with food scarcity.” The regulatory community has identified a real need for addressing food waste and the lack of circularity in the food industry. Sustainable management of food involves “a systematic approach that seeks to reduce wasted food and its associated impacts over the entire lifecycle, starting with the use of natural resources, manufacturing, sales, and consumption, and ending with decisions on recovery of final disposal” (EPA). Watch for efforts to promote sustainable food management to expand to meet demand.
Guidance:
A thorough food and packaging assessment can help identify appropriate strategies to avoid waste, cut down on disposal costs, reduce over-purchasing and labor costs, reduce water and energy use and greenhouse gas (GHG) emissions associated with food production.
Food Safety Verification Program (FSVP)
While not a new rule, FSVP remains a key focus as the surge in food demand and lack of supply has created an environment ripe for food fraud. FDA recently sent a number of warning letters to companies across the U.S. putting them on notice for not having FSVPs for a number of imported food products, a significant violation of compliance with FSVP regulations. On January 10, 2023, FDA issued its final FSVP guidance document to help importers comply with the FSVP regulation. It offers clarification on what foods/entities the FSVP regulation applies to, what information must be included in the FSVP, and who must develop and perform FSVP activities.
Guidance:
- Assess your supplier approval/management program, focusing on the fundamental aspects of FSVP—those requirements that must be verified, recorded, and evident in documents supporting foreign shipments of food product(s) under the rule.
- Evaluate potential foreign suppliers’ performance and the risks posed by the food. Use FDA’s guidance document to determine and conduct appropriate foreign supplier verification activities.
- Implement a supplier approval and management system to improve coordination with and communication of approved suppliers; manage supplier requirements and supplier evaluations/approvals; and maintain all required documentation.
- Train your staff to have the knowledge needed to implement a successful FSVP that meets compliance requirements.
Set Your Goals for 2023
With these challenges simultaneously competing for attention—and with fewer resources to manage it all—companies need to assess priorities, needs, and requirements and create a plan for how to meet them. KTL suggests completing the following early in 2023:
- Get senior leadership commitment and invest in creating a food safety culture that prioritizes food safety and quality.
- Conduct a comprehensive food safety and quality gap assessment. This should be the starting point for understanding your regulatory and certification obligations and current compliance status—and for ensuring you are prepared to meet pending regulatory developments.
- Get your documentation in place. Update and/or develop the procedures, programs, and records you need to demonstrate compliance, and implement a reliable system to keep them organized and readily accessible.
- Leverage IT solutions to streamline compliance, manage certification requirements, and create business efficiencies.
- Seek third-party oversight. Having external experts periodically look inside your company provides an objective view of what is really going on, helps you to prepare for audits, and allows you to implement corrective/preventive actions that ensure compliance.
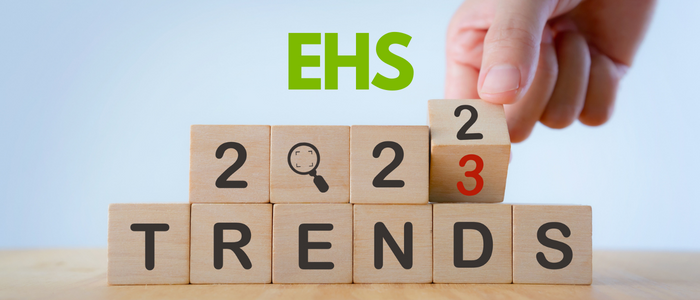
EHS Trends to Watch in 2023
Every year, we see a number of environmental, health, and safety (EHS) trends rise to the surface that have the potential to impact many industries. Some challenges and opportunities in EHS remain ongoing; some are just gaining traction with impacts yet to be known. Regardless, the start of a new year provides the opportunity to plan for EHS issues and trends on the horizon and prioritize efforts to ensure ongoing compliance.
Here are some of the top EHS trends KTL is keeping watch on in 2023—and some guidance to help you as you set your EHS strategy for the new year.
Resource Constraints and Technology Solutions
EHS personnel are being asked to manage a lot—and often in growing areas that may be outside their education, expertise, and/or experience. Resource constraints—particularly related to staffing—remain a significant concern across industry, and EHS is certainly not immune. Impacts from the “Great Resignation” of November 2021 and beyond continue to leave many companies without the resources needed to effectively manage EHS requirements.
Achieving and maintaining EHS compliance requires great management and expertise to ensure all aspects of a company’s technical compliance have been identified and are being actively handled. KTL has been working with more and more EHS departments to fill these gaps—either with outsourced personnel or compliance efficiency tools—as companies look to recruit EHS staff and meet compliance obligations.
Guidance:
- Develop a relationship with someone you trust to do things in your best interest, understanding that EHS should be a process of continuous improvement. Use them to help you understand what regulations apply. Let them help you prioritize your compliance plan. Use them to do your annual training. Rely on them as a part of your team.
- Employ information technology (IT) solutions to create compliance efficiencies. A well-designed and executed compliance information management system brings IT and management systems together to coordinate, organize, control, analyze, and visualize information in such a way that helps organizations remain in compliance and operate efficiently. A system like this will help provide operational flexibility, generate business improvement, and prepare organizations to address these and other EHS compliance challenges that will continue to surface.
EPA Inspections and Enforcement
EPA intends to continue its enforcement path, holding environmental violators and responsible parties accountable. Significant investments are being made to enforce and ensure compliance with the nation’s environmental laws, including $213 million for civil enforcement efforts, $148 million for compliance monitoring efforts, and $69 million for criminal enforcement efforts. The Agency also has plans to improve inspections by sending 75% of EPA inspection reports to facilities within 70 days of inspection and conducting 55% of annual EPA inspections at facilities that affect communities with potential environmental justice (EJ) concerns (see more on EJ below).
Guidance:
- Design and maintain a safe facility to prevent accidental releases and minimize the consequences of accidental releases that do occur. Conduct a gap assessment to ensure the required processes and systems are functioning as intended.
- Establish a quick response internal inspection team that can evaluate all areas of risk in your facility to ensure you are in compliance, particularly at the time of inspection.
- Understand the hazards posed by chemicals at the facility and assess the impacts of a potential release. Complete a waste characterization for all hazardous and solid waste streams to make sure you are appropriately managing your universal waste and hazardous waste.
- Check your Emergency Response Plan to ensure it has identified emergency contacts for your facility and that the contacts are current. Coordinate with local emergency responders.
Environmental Justice (EJ)
EPA’s Strategic Plan includes a goal that EJ and civil rights will be embedded into EPA’s programs, policies, and activities to reduce disparities in environmental and public health conditions. This focus on EJ has continued to gain momentum with a slew of additional significant actions taken in 2022 to further elevate EJ priorities and deliver on the Administration’s promises to advance justice and equity when it comes to ensuring clean air and water for all communities; safeguarding and revitalizing communities (i.e., Superfund and RCRA); and ensuring safety of chemicals through civil rights and compliance reviews, audits, and community outreach.
Guidance:
- Take the time to understand the communities where you operate—be informed, be prepared, and be proactive. Establish companywide priorities and goals and commit the appropriate resources to address EJ concerns.
- There are a number of EJ grants, funding, and other technical assistance available. EPA’s new Office of Environmental Justice and External Civil Rights is positioned to deliver new grants and technical assistance to meet EJ goals.
Sustainability and Climate Change
The Biden Administration previously committed to a net zero economy by 2050. EPA is focused on reducing greenhouse gas (GHG) emissions by promulgating rules to reduce pollution from the power sector, setting vehicle emission standards, and partnering with the public and private sectors communities (especially those underserved and disproportionally at risk) to increase energy efficiency in the residential, commercial, and industrial sectors. In addition, there is $100 million in grants to support efforts to reduce GHG emissions and increase resiliency in the nation’s infrastructure and $35 million to implement the American Innovation in Manufacturing Act to continue phasing out GHGs.
Guidance:
- Conduct a lifecycle analysis (LCA) to identify and quantify the inputs and outputs in a process and use data to assess the potential environmental impacts across the lifecycle.
- Have an energy audit completed of your facilities.
- Get input from employees on what initiatives are important to them by enacting a sustainability committee or adding sustainability to your EHS agenda.
Safer Communities by Chemical Accident Prevention (SCCAP)
EPA proposed on August 31, 2022 to strengthen the Risk Management Program (RMP) regulations with the SCCAP proposed rule. The proposed SCCAP amendments include a number of requirements that were originally promulgated by the Obama Administration EPA in 2017 and subsequently rescinded during the Trump Administration in 2019, plus several new requirements considering impacts of climate change, EJ concerns, employee participation, and enhanced community notification. Proposed changes would require RMP-regulated facilities to better consider surrounding communities and the consequences of potential chemical accidents that could have significant impacts on industry requirements going forward.
Guidance:
- Identify/understand/prioritize your compliance risks and develop strategies to minimize them to the extent possible.
- Outline steps to improve performance and safe operations, including defining organizational roles and responsibilities. Plan and conduct required tabletop exercises and coordinate with Local Emergency Planning Committees (LEPCs) to ensure your plans work in practice.
- Streamline compliance methods and improve operational efficiencies by implementing IT solutions and compliance management systems that coordinate, organize, control, analyze, and visualize information.
PFAS Contamination
More and more facilities are going to be directly impacted by mitigation efforts and future regulatory action related to per- and polyfluoroalkyl substances (PFAS). PFAS contamination is an extremely complicated issue—and concern is mounting over its impacts and how to regulate these chemicals going forward. EPA has set aside $126 million to increase its understanding of human health and ecological effects of PFAS contamination, restrict its uses, and remediate PFAS that have been released. Over the course of 2022, EPA took several actions to further protect individuals and communities from the health risks posed by these forever chemicals and more is on the way.
Guidance:
- Evaluate your current environmental risk level and develop strategies to minimize risks to the extent possible. Proper usage strategies, a comprehensive environmental management system (EMS), and a forward-thinking Emergency Response Plan will remain vital tools for companies potentially dealing with PFAS to effectively manage the associated risks.
- Work with LEPCs to coordinate emergency response efforts and exercises to keep communities informed and safe.
Set Your Goals for 2023
With these trends toward more regulation, more enforcement, and more focus on EJ and sustainability—but with fewer resources to manage it all—companies need to accurately assess compliance requirements and create a plan for how to meet them. KTL suggests completing the following early in 2023:
- Get senior leadership commitment. It is often clear how an organization prioritizes EHS with little digging. Even with the best EHS personnel, the organization and its EHS system will only be as good as the top leadership and what is important to them.
- Conduct a comprehensive gap assessment to ensure you are meeting the requirements of all applicable EHS regulations. This should be the starting place for understanding your regulatory obligations and current compliance status.
- Perform a comprehensive onsite risk assessment with associated risk minimization planning and plan/conduct annual spill drills to practice emergency response for hazardous chemical incidents.
- Organize your records. Know what records you need. Document your inspections and your training. Develop standard operating procedures (SOPs) so people know what to do.
- Create an integrated management system (e.g., ISO 9001/14001/45001) by finding commonalities between the standards and leveraging pieces of each to develop a reliable system that works for your organization. Implement IT solutions to streamline compliance and create business efficiencies.
- Seek third-party oversight. Having external experts periodically look inside your company provides an objective view of what is really going on, helps you to prepare for audits, and allows you to implement corrective/preventive actions that ensure compliance.
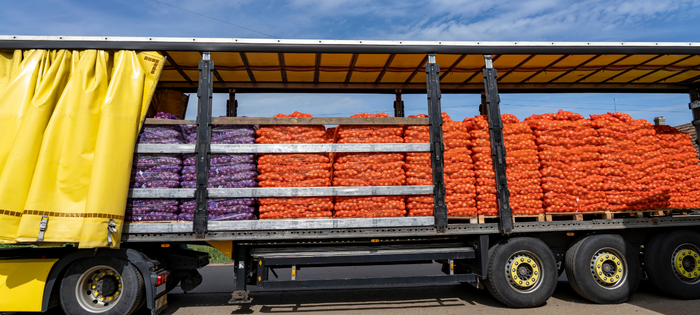
Comments: No Comments
Final Guidance: Foreign Supplier Verification Program
On January 10, 2023, the U.S. Food and Drug Administration (FDA) issued its final guidance for the Foreign Supplier Verification Programs (FSVP) for Importers of Food for Humans and Animals.
Part of the Food Safety Modernization Act (FSMA), FSVP establishes risk-based foreign supplier verification activities that importers of human and animal foods must follow to ensure their imports are not adulterated or misbranded and are produced in compliance with section 418 or 419 of the Food, Drug, and Cosmetic (FD&C) Act, as appropriate. The intent of FSVP is to hold importers accountable for verifying foreign suppliers are meeting U.S. food safety standards.
The new industry guidance document provides information to help importers comply with the FSVP regulation. It offers clarification on what foods/entities the FSVP regulation applies to, what information must be included in the FSVP, and who must develop and perform FSVP activities. It also includes recommendations on the requirements to:
- Analyze the hazards in food.
- Evaluate a potential foreign supplier’s performance and the risk posed by the food.
- Determine and conduct appropriate foreign supplier verification activities.
- Meet modified FSVP requirements in a variety of categories, such as requirements for importers of dietary supplements or very small importers.
The final guidance document is available online.
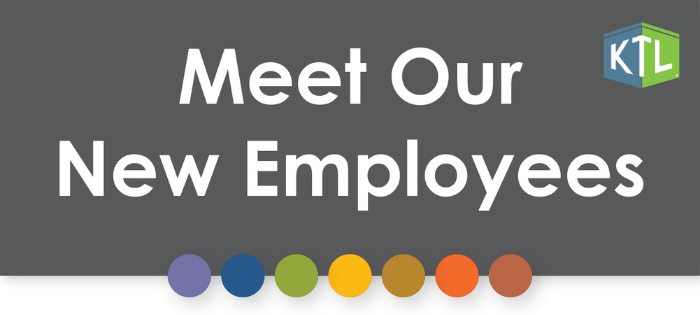
KTL News: New Food Safety Consultant
KTL is pleased to welcome the newest member of our food safety team!
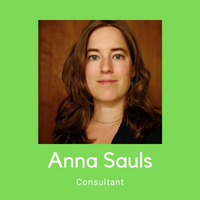
Anna Sauls, Senior Consultant
Anna Sauls is a food safety and quality professional with more than ten years of experience. Prior to joining KTL, she served as an industry trainer for food, beverage, and natural products. Anna has in-depth knowledge of FDA food safety regulations and a strong ability to effectively communicate and train others on meeting food safety and quality requirements. Her areas of expertise include 21 CFR, food safety hazards, Hazard Analysis and Critical Control Points (HACCP), current Good Manufacturing Practices (cGMPs), Preventive Controls for Human Foods, food defense, environmental monitoring, sanitation, auditing, and documentation. Anna is based in Candler, NC. Read her full bio…
asauls@goktl.com | 252.339.7583
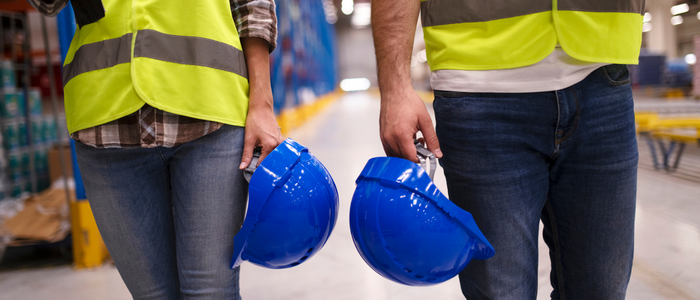
Comments: No Comments
Pending Changes to PSM
In August 2013, President Obama signed Executive Order (EO) 13650, Improving Chemical Facility Safety and Security, with the objective to “improve the safety and security of chemical facilities and reduce the risks of hazardous chemicals to workers and communities.” A key element of EO 13650 involves modernizing federal policies, regulations, and standards.
The Order specifically calls on the Occupational Safety and Health Administration (OSHA) and Environmental Protection Agency (EPA) to, among other things, review the Process Safety Management (PSM) and Risk Management Program (RMP) rules to determine if their covered hazardous chemical lists should be expanded.
Over nine years have passed since EO 13650 was issued, and the PSM/RMP modernization efforts are still underway. EPA’s most recent action on August 31, 2022 proposed to strengthen the RMP regulations with the Safer Communities by Chemical Accident Prevention (SCCAP) proposed rule. OSHA has yet to propose updates to the PSM rule, which has not been updated since its publication in 1992; however, the PSM rulemaking project is back on the Unified Agenda, and OSHA is working to make progress.
Progress on PSM
OSHA published the PSM standard (29 CFR 1910.119) in 1992 in response to several catastrophic chemical-release incidents. PSM requires employers to implement safety programs that identify, evaluate, and control highly hazardous chemicals. Unlike other standards, PSM is “performance-based” rather than prescriptive. It outlines 14 management system elements for controlling highly hazardous chemicals. Employers have the flexibility to tailor their PSM programs to the unique conditions at their facilities.
In response to EO 13650, OSHA published a Request for Information (RFI) in December 2013 and then completed a Small Business Advocacy Review Panel (SBAR) in June 2016. Following the SBAR, PSM was moved to the Long-Term Actions list on the Unified Agenda but was placed back on the Unified Agenda in Spring 2021.
Most recently, OSHA held an informal stakeholder meeting on October 12, 2022, to reengage stakeholders and solicit comments on the modernization topics mentioned in the RFI and SBAR panel report.
Potential PSM Changes
The PSM and RMP rules were written to complement each other. OSHA and EPA continue to coordinate as both agencies consider revisions to their respective rules. The Federal Register notice for OSHA’s stakeholder meeting lists the following potential changes to the scope of the current PSM standard that OSHA is considering:
- Clarifying the exemption for atmospheric storage tanks.
- Expanding the scope to include oil- and gas-well drilling and servicing.
- Resuming enforcement for oil and gas production facilities.
- Expanding PSM coverage and requirements for reactive chemical hazards.
- Updating and expanding the list of highly hazardous chemicals in Appendix A.
- Extending PSM requirements to cover dismantling and disposal of explosives and pyrotechnics.
- Clarifying the scope of the retail facilities exemption
- Defining the limits of a PSM-covered process.
- Including a definition of recognized and generally accepted as good engineering practices (RAGAGEP).
- Including a definition of critical equipment.
- Strengthening employee participation and including stop work authority.
- Requiring evaluation of updates to applicable RAGAGEP.
- Requiring continuous updating of collected information.
- Requiring formal resolution of Process Hazard Analysis team recommendations that are not utilized.
- Requiring safer technology and alternatives analysis.
- Requiring considering of natural disasters and extreme temperatures in their PSSM programs.
- Covering the mechanical integrity of any critical equipment.
- Better explaining equipment deficiencies.
- Clarifying organizational changes.
- Requiring root cause analysis.
- Requiring coordination of emergency planning with local emergency response authorities.
- Requiring third-party compliance audits.
- Developing a system for periodic review of and necessary revisions to their PSM management systems.
- Requiring the development of written procedures for all elements specified in the standard, and to identify records required by the standard along with a records retention policy.
What’s Next
While there is still much uncertainty regarding what potential changes may be made to the PSM standard—and when those changes could take effect—it is never too early for PSM-impacted facilities to consider the following:
- How might the potential changes listed above impact your business?
- What issues does your facility foresee with compliance?
- What systems, processes, procedures, plans, etc. does your facility need to ensure ongoing compliance?
KTL will continue to monitor developments with the PSM standard. As things progress, we can help you to:
- Identify/understand/prioritize your facility risks.
- Define organizational roles and responsibilities.
- Better manage documents and information to demonstrate compliance.
- Identify resources to help your facility comply with potential changes to the PSM standard.