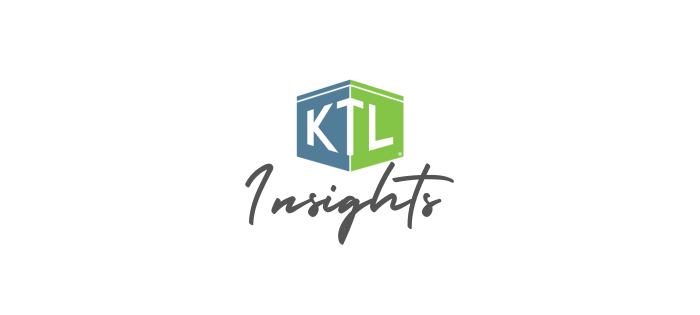
Integrated Emergency Response Plans
The most effective way to respond to an emergency is to properly plan for it before it happens. That’s precisely why so many federal, state, and municipal laws and regulations require many facilities to develop and implement some sort of Emergency Response Plan (ERP).
Effective Emergency Response
An ERP is intended to outline the steps an organization needs to take in an emergency—and after—to protect workers’ health and safety, the environment, the surrounding community, and the business itself. The requirements developed by various agencies are important, as they establish the components that must be included in an ERP to comply with regulations and respond effectively.
Most ERPs contain the same basic information. However, it can get complicated when a facility is subject to more than one regulation requiring an ERP, because even though the various regulations share many similarities, they also contain important differences (e.g., command structures, training requirements, equipment needs, operating protocols). Often, facilities end up creating a different ERP to respond to the different regulatory requirements. In an actual emergency, this can create inconsistencies or, worse yet, an implementation nightmare trying to figure out which ERP to follow.
Importance of Integration
The solution lies in integration. For example, consider an integrated management system that allows organizations to align standards, find common management system components (e.g., terminology, policies, objectives, processes, resources), and add measurable and recognizable business value. The same can be done with the various ERPs required within a facility.
It shouldn’t come as a surprise that in 1996, the U.S. National Response Team (NRT) published initial guidance for consolidating multiple ERPs into one core document. The Integrated Contingency Plan (ICP or One Plan) is a single, unified ERP intended to help organizations comply with the various emergency response requirements of the Environmental Protection Agency (EPA), U.S. Coast Guard, Occupational Safety and Health Administration (OSHA), Department of Transportation (DOT), and Department of Interior (DOI). The ICP Guidance does not change any of the existing requirements of the regulations it covers; rather, it provides a format for consolidating, organizing, and presenting the required emergency response information.
While the ICP does not currently incorporate all federal regulations addressing emergency response, it does establish a basic framework for organizations to pull in ERPs for any applicable regulations. And the benefits of doing so are many:
- Streamlined planning process. A single document simplifies the planning, development, and maintenance process. When plans are integrated, it minimizes duplication of effort, eliminates discrepancies and inconsistencies, and helps the organization identify and fill in gaps.
- Improved emergency response. It is much easier—and faster—for emergency responders and employees to navigate one plan rather than multiple separate ones. One plan allows for a single command structure with defined roles rather than potentially conflicting responsibilities. This all allows responders to act quickly and decisively to minimize potential disruption to the organization and public.
- Greater compliance. An integrated ERP provides improved visibility to all parts of the organization’s emergency response and helps reveal gaps that could prove costly and/or dangerous. This is especially important for organizations that must comply with several regulations.
- Potential cost savings. Streamlined and simplified planning reduces the resources required to build the plan. An integrated ERP may also help eliminate regulatory fines and minimize the need for and associated costs of emergency response/cleanup efforts.
Find Your Format
The goal of an integrated ERP is not to create new requirements but to consolidate existing concepts into a single functional plan structure. Regardless of what the plan looks like, it should start with:
- An assessment of the facility’s vulnerabilities to various emergency situations.
- An understanding of the various applicable emergency planning laws and regulations to determine which specific requirements must be incorporated. For example, food emergency response has different implications that must be integrated, particularly when it comes to recovery. A food production facility that is ordered or otherwise required to cease operations during an emergency may not reopen until authorization has been granted by the regulatory authority. Food facilities also have strict guidelines to follow for salvaging, reconditioning, and/or discarding product.
With this understanding, the ERP should then comprise step-by-step guidelines for addressing the most significant emergency situations. The core plan should be straightforward and concise and outline fundamental response procedures. More detailed information can be included in the annex. Most ERPs should include the following basic elements:
- Facility information. Consolidate common elements required in various plans, including site description, statement of purpose, scope, drawings, maps, roster of emergency response personnel, emergency response equipment, key contacts for plan development and maintenance, etc.
- Steps to initiate, conduct, and terminate a response. Outline essential response actions and notification procedures, with references to the annex for more detailed information. Provide concise and specific information that is time-critical in the earliest stages of the response and a framework to guide responders through key steps to deliver an effective response.
- Designated emergency responders. Develop a single command structure for all types of emergencies. Assign qualified, high-level individuals who are familiar with emergency procedures to fill emergency roles. In addition, list the appropriate authorities for specific emergencies, as well as their contact information.
- Evacuation plan/routes and rally points. Clearly mark evacuation routes and identify rally points where employees should meet upon exiting. Do not allow employees to leave designated rally points until it has been documented they have safely left the building.
- Data and information backup technology. Develop provisions for data backup to secondary/off-site systems, as well as alternate options for communications and power.
- Designated plan for communication. Outline who is communicating what, when they are communicating it, and how it is being communicated. This includes internal communication, as well as communication to customers/clients/suppliers/vendors that may be impacted, the media, and the appropriate regulatory authorities.
- Supporting materials. The annex should provide detailed support information based on the procedures outlined in the core plan and required regulatory compliance documentation. Importantly, facilities should create a table that cross-references individual regulatory requirements with the plan to ensure there are no gaps and to demonstrate compliance.
Ensuring Success
The goal of emergency response planning is to minimize impacts to the environment and workers’ health and safety, as well as disruptions to operations. An integrated ERP has the potential to significantly reduce the number of decisions required to respond in an emergency, eliminate confusion and disagreement regarding roles and responsibilities, and enable a timelier, more coordinated response.
That all being said, an integrated ERP will only be effective if it is thoroughly and consistently communicated to all employees. These best practices will help ensure that the integrated ERP functions not only on paper, but also in practice:
- Periodic training is vital to ensure employees understand the ERP and are fully aware of emergency response procedures. It is especially important in an integrated ERP that first responders are trained to handle all potential emergencies rather than more narrowly trained on response for a single regulation.
- Routine drills significantly improve understanding of the ERP, clarify employee roles, test procedures to ensure they work, and diminish confusion during an emergency.
- Posting an abbreviated version of the ERP throughout the plant provides easy access to all employees if an emergency occurs. This summary version of the ERP should highlight the most vital information for quick response: recognized hazards, high-level emergency procedures, evacuation routes, and key contacts.
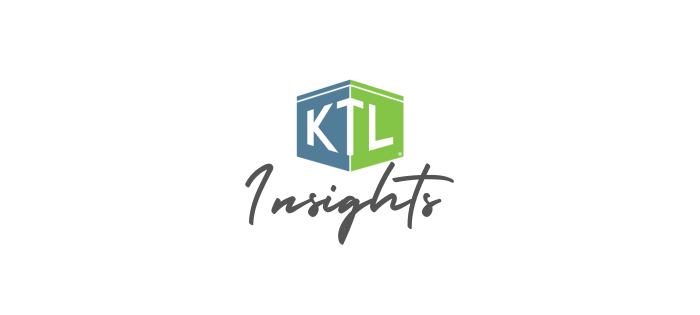
EHS Trends to Watch in 2023
Every year, we see a number of environmental, health, and safety (EHS) trends rise to the surface that have the potential to impact many industries. Some challenges and opportunities in EHS remain ongoing; some are just gaining traction with impacts yet to be known. Regardless, the start of a new year provides the opportunity to plan for EHS issues and trends on the horizon and prioritize efforts to ensure ongoing compliance.
Here are some of the top EHS trends KTL is keeping watch on in 2023—and some guidance to help you as you set your EHS strategy for the new year.
Resource Constraints and Technology Solutions
EHS personnel are being asked to manage a lot—and often in growing areas that may be outside their education, expertise, and/or experience. Resource constraints—particularly related to staffing—remain a significant concern across industry, and EHS is certainly not immune. Impacts from the “Great Resignation” of November 2021 and beyond continue to leave many companies without the resources needed to effectively manage EHS requirements.
Achieving and maintaining EHS compliance requires great management and expertise to ensure all aspects of a company’s technical compliance have been identified and are being actively handled. KTL has been working with more and more EHS departments to fill these gaps—either with outsourced personnel or compliance efficiency tools—as companies look to recruit EHS staff and meet compliance obligations.
Guidance:
- Develop a relationship with someone you trust to do things in your best interest, understanding that EHS should be a process of continuous improvement. Use them to help you understand what regulations apply. Let them help you prioritize your compliance plan. Use them to do your annual training. Rely on them as a part of your team.
- Employ information technology (IT) solutions to create compliance efficiencies. A well-designed and executed compliance information management system brings IT and management systems together to coordinate, organize, control, analyze, and visualize information in such a way that helps organizations remain in compliance and operate efficiently. A system like this will help provide operational flexibility, generate business improvement, and prepare organizations to address these and other EHS compliance challenges that will continue to surface.
EPA Inspections and Enforcement
EPA intends to continue its enforcement path, holding environmental violators and responsible parties accountable. Significant investments are being made to enforce and ensure compliance with the nation’s environmental laws, including $213 million for civil enforcement efforts, $148 million for compliance monitoring efforts, and $69 million for criminal enforcement efforts. The Agency also has plans to improve inspections by sending 75% of EPA inspection reports to facilities within 70 days of inspection and conducting 55% of annual EPA inspections at facilities that affect communities with potential environmental justice (EJ) concerns (see more on EJ below).
Guidance:
- Design and maintain a safe facility to prevent accidental releases and minimize the consequences of accidental releases that do occur. Conduct a gap assessment to ensure the required processes and systems are functioning as intended.
- Establish a quick response internal inspection team that can evaluate all areas of risk in your facility to ensure you are in compliance, particularly at the time of inspection.
- Understand the hazards posed by chemicals at the facility and assess the impacts of a potential release. Complete a waste characterization for all hazardous and solid waste streams to make sure you are appropriately managing your universal waste and hazardous waste.
- Check your Emergency Response Plan to ensure it has identified emergency contacts for your facility and that the contacts are current. Coordinate with local emergency responders.
Environmental Justice (EJ)
EPA’s Strategic Plan includes a goal that EJ and civil rights will be embedded into EPA’s programs, policies, and activities to reduce disparities in environmental and public health conditions. This focus on EJ has continued to gain momentum with a slew of additional significant actions taken in 2022 to further elevate EJ priorities and deliver on the Administration’s promises to advance justice and equity when it comes to ensuring clean air and water for all communities; safeguarding and revitalizing communities (i.e., Superfund and RCRA); and ensuring safety of chemicals through civil rights and compliance reviews, audits, and community outreach.
Guidance:
- Take the time to understand the communities where you operate—be informed, be prepared, and be proactive. Establish companywide priorities and goals and commit the appropriate resources to address EJ concerns.
- There are a number of EJ grants, funding, and other technical assistance available. EPA’s new Office of Environmental Justice and External Civil Rights is positioned to deliver new grants and technical assistance to meet EJ goals.
Sustainability and Climate Change
The Biden Administration previously committed to a net zero economy by 2050. EPA is focused on reducing greenhouse gas (GHG) emissions by promulgating rules to reduce pollution from the power sector, setting vehicle emission standards, and partnering with the public and private sectors communities (especially those underserved and disproportionally at risk) to increase energy efficiency in the residential, commercial, and industrial sectors. In addition, there is $100 million in grants to support efforts to reduce GHG emissions and increase resiliency in the nation’s infrastructure and $35 million to implement the American Innovation in Manufacturing Act to continue phasing out GHGs.
Guidance:
- Conduct a lifecycle analysis (LCA) to identify and quantify the inputs and outputs in a process and use data to assess the potential environmental impacts across the lifecycle.
- Have an energy audit completed of your facilities.
- Get input from employees on what initiatives are important to them by enacting a sustainability committee or adding sustainability to your EHS agenda.
Safer Communities by Chemical Accident Prevention (SCCAP)
EPA proposed on August 31, 2022 to strengthen the Risk Management Program (RMP) regulations with the SCCAP proposed rule. The proposed SCCAP amendments include a number of requirements that were originally promulgated by the Obama Administration EPA in 2017 and subsequently rescinded during the Trump Administration in 2019, plus several new requirements considering impacts of climate change, EJ concerns, employee participation, and enhanced community notification. Proposed changes would require RMP-regulated facilities to better consider surrounding communities and the consequences of potential chemical accidents that could have significant impacts on industry requirements going forward.
Guidance:
- Identify/understand/prioritize your compliance risks and develop strategies to minimize them to the extent possible.
- Outline steps to improve performance and safe operations, including defining organizational roles and responsibilities. Plan and conduct required tabletop exercises and coordinate with Local Emergency Planning Committees (LEPCs) to ensure your plans work in practice.
- Streamline compliance methods and improve operational efficiencies by implementing IT solutions and compliance management systems that coordinate, organize, control, analyze, and visualize information.
PFAS Contamination
More and more facilities are going to be directly impacted by mitigation efforts and future regulatory action related to per- and polyfluoroalkyl substances (PFAS). PFAS contamination is an extremely complicated issue—and concern is mounting over its impacts and how to regulate these chemicals going forward. EPA has set aside $126 million to increase its understanding of human health and ecological effects of PFAS contamination, restrict its uses, and remediate PFAS that have been released. Over the course of 2022, EPA took several actions to further protect individuals and communities from the health risks posed by these forever chemicals and more is on the way.
Guidance:
- Evaluate your current environmental risk level and develop strategies to minimize risks to the extent possible. Proper usage strategies, a comprehensive environmental management system (EMS), and a forward-thinking Emergency Response Plan will remain vital tools for companies potentially dealing with PFAS to effectively manage the associated risks.
- Work with LEPCs to coordinate emergency response efforts and exercises to keep communities informed and safe.
Set Your Goals for 2023
With these trends toward more regulation, more enforcement, and more focus on EJ and sustainability—but with fewer resources to manage it all—companies need to accurately assess compliance requirements and create a plan for how to meet them. KTL suggests completing the following early in 2023:
- Get senior leadership commitment. It is often clear how an organization prioritizes EHS with little digging. Even with the best EHS personnel, the organization and its EHS system will only be as good as the top leadership and what is important to them.
- Conduct a comprehensive gap assessment to ensure you are meeting the requirements of all applicable EHS regulations. This should be the starting place for understanding your regulatory obligations and current compliance status.
- Perform a comprehensive onsite risk assessment with associated risk minimization planning and plan/conduct annual spill drills to practice emergency response for hazardous chemical incidents.
- Organize your records. Know what records you need. Document your inspections and your training. Develop standard operating procedures (SOPs) so people know what to do.
- Create an integrated management system (e.g., ISO 9001/14001/45001) by finding commonalities between the standards and leveraging pieces of each to develop a reliable system that works for your organization. Implement IT solutions to streamline compliance and create business efficiencies.
- Seek third-party oversight. Having external experts periodically look inside your company provides an objective view of what is really going on, helps you to prepare for audits, and allows you to implement corrective/preventive actions that ensure compliance.
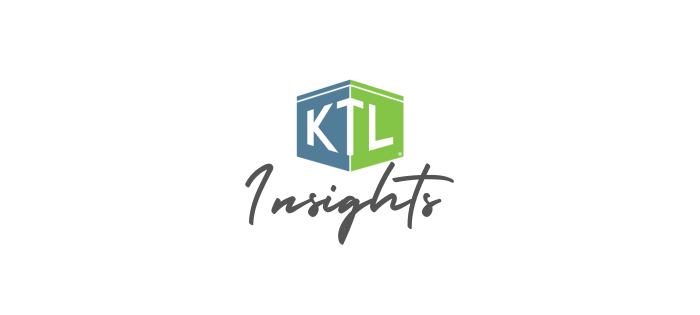
Comments: No Comments
Pending Changes to PSM
In August 2013, President Obama signed Executive Order (EO) 13650, Improving Chemical Facility Safety and Security, with the objective to “improve the safety and security of chemical facilities and reduce the risks of hazardous chemicals to workers and communities.” A key element of EO 13650 involves modernizing federal policies, regulations, and standards.
The Order specifically calls on the Occupational Safety and Health Administration (OSHA) and Environmental Protection Agency (EPA) to, among other things, review the Process Safety Management (PSM) and Risk Management Program (RMP) rules to determine if their covered hazardous chemical lists should be expanded.
Over nine years have passed since EO 13650 was issued, and the PSM/RMP modernization efforts are still underway. EPA’s most recent action on August 31, 2022 proposed to strengthen the RMP regulations with the Safer Communities by Chemical Accident Prevention (SCCAP) proposed rule. OSHA has yet to propose updates to the PSM rule, which has not been updated since its publication in 1992; however, the PSM rulemaking project is back on the Unified Agenda, and OSHA is working to make progress.
Progress on PSM
OSHA published the PSM standard (29 CFR 1910.119) in 1992 in response to several catastrophic chemical-release incidents. PSM requires employers to implement safety programs that identify, evaluate, and control highly hazardous chemicals. Unlike other standards, PSM is “performance-based” rather than prescriptive. It outlines 14 management system elements for controlling highly hazardous chemicals. Employers have the flexibility to tailor their PSM programs to the unique conditions at their facilities.
In response to EO 13650, OSHA published a Request for Information (RFI) in December 2013 and then completed a Small Business Advocacy Review Panel (SBAR) in June 2016. Following the SBAR, PSM was moved to the Long-Term Actions list on the Unified Agenda but was placed back on the Unified Agenda in Spring 2021.
Most recently, OSHA held an informal stakeholder meeting on October 12, 2022, to reengage stakeholders and solicit comments on the modernization topics mentioned in the RFI and SBAR panel report.
Potential PSM Changes
The PSM and RMP rules were written to complement each other. OSHA and EPA continue to coordinate as both agencies consider revisions to their respective rules. The Federal Register notice for OSHA’s stakeholder meeting lists the following potential changes to the scope of the current PSM standard that OSHA is considering:
- Clarifying the exemption for atmospheric storage tanks.
- Expanding the scope to include oil- and gas-well drilling and servicing.
- Resuming enforcement for oil and gas production facilities.
- Expanding PSM coverage and requirements for reactive chemical hazards.
- Updating and expanding the list of highly hazardous chemicals in Appendix A.
- Extending PSM requirements to cover dismantling and disposal of explosives and pyrotechnics.
- Clarifying the scope of the retail facilities exemption
- Defining the limits of a PSM-covered process.
- Including a definition of recognized and generally accepted as good engineering practices (RAGAGEP).
- Including a definition of critical equipment.
- Strengthening employee participation and including stop work authority.
- Requiring evaluation of updates to applicable RAGAGEP.
- Requiring continuous updating of collected information.
- Requiring formal resolution of Process Hazard Analysis team recommendations that are not utilized.
- Requiring safer technology and alternatives analysis.
- Requiring considering of natural disasters and extreme temperatures in their PSSM programs.
- Covering the mechanical integrity of any critical equipment.
- Better explaining equipment deficiencies.
- Clarifying organizational changes.
- Requiring root cause analysis.
- Requiring coordination of emergency planning with local emergency response authorities.
- Requiring third-party compliance audits.
- Developing a system for periodic review of and necessary revisions to their PSM management systems.
- Requiring the development of written procedures for all elements specified in the standard, and to identify records required by the standard along with a records retention policy.
What’s Next
While there is still much uncertainty regarding what potential changes may be made to the PSM standard—and when those changes could take effect—it is never too early for PSM-impacted facilities to consider the following:
- How might the potential changes listed above impact your business?
- What issues does your facility foresee with compliance?
- What systems, processes, procedures, plans, etc. does your facility need to ensure ongoing compliance?
KTL will continue to monitor developments with the PSM standard. As things progress, we can help you to:
- Identify/understand/prioritize your facility risks.
- Define organizational roles and responsibilities.
- Better manage documents and information to demonstrate compliance.
- Identify resources to help your facility comply with potential changes to the PSM standard.
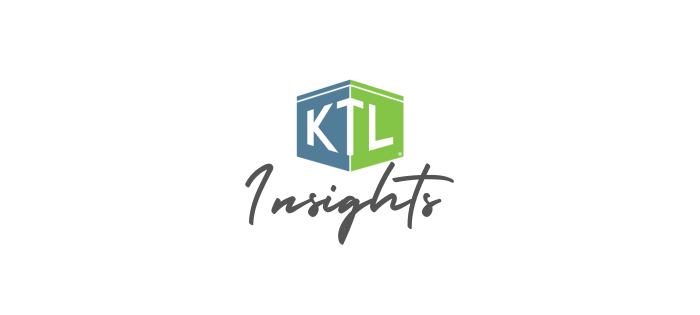
Comments: No Comments
OSHA Strengthens Severe Violator Enforcement Program
The Occupational Safety and Health Administration (OSHA) is stepping up enforcement. On September 16, 2022, the U.S. Department of Labor (DOL) announced expanded criteria for placement in the OSHA Severe Violator Enforcement Program (SVEP) to strengthen enforcement, improve compliance with workplace safety standards (i.e., OSH Act), and reduce worker injuries and illnesses.
SVEP: Then and Now
The expanded criteria build off the original SVEP, which was first introduced on June 18, 2010, to focus OSHA’s resources on inspecting employers who continually expose workers to very serious dangers, even after being cited for them. This includes employers who have demonstrated indifference to OSH Act obligations by either “willfully or repeatedly violating federal health and safety laws or demonstrating refusal to correct previous violations” (i.e., failure to abate).
The changes enacted by OSHA in September 2022 are intended to broaden the SVEP’s scope and maximize the tools available to ensure employers comply with their legal obligation to provide safe and healthful workplaces. The new instructions “reflect the Biden-Harris administration’s commitment to ensuring OSHA has the tools it needs to ensure employers protect their workers or hold them accountable when they fail to provide safe and healthy workplaces,” explains Doug Parker, Assistant Secretary of Labor for Occupational Safety and Health. He reinforces, “These changes to SVEP will hold a microscope to those employers who continue to expose workers to very serious dangers.”
This goes hand-in-hand with the Biden Administration’s recent efforts to make significant improvements in workplace safety protection for American workers through proposed increases in funding and significant increases to OSHA’s maximum penalties, as proposed in the original Build Back Better Act.
What’s Changing
The table below outlines how the SVEP criteria are changing from 2010 to 2022.
THEN: SVEP 2010 | NOW: SVEP 2022 |
Limited to cases involving fatalities, three or more hospitalizations, high-emphasis hazards, the potential release of a highly hazardous chemical (PSM), and enforcement actions classified as egregious. | Expands program criteria to include all hazards and OSHA standards, broadening the program’s scope and potential for additional industries to fall within its parameters. |
Focused on cases where there was a willful or repeated serious violation or a hazard the employer failed to abate that was directly related to either an employee death or an incident that caused three or more hospitalizations. | Focuses on program placement for employers with citations for at least two willful or repeated violations or who receive failure-to-abate notices based on the significance of serious violations. |
Required no designated timeframe in which OSHA would conduct a follow-up inspection after the final order. | Requires follow-up or referral inspections to be conducted one year (but no longer than two years) after the final order. |
Permitted removal from the SVEP three years after the final order date. | Allows for potential removal from the SVEP three years after the date of receiving verification that the employer has: · Abated all SVEP-related hazards. · Paid all final penalties. · Where applicable, followed and completed all applicable settlement provisions. · Received no additional serious citations related to the hazards identified in the original SVEP inspection or any related establishments. · Received one follow-up or referral OSHA inspection. |
Only allowed employers to become eligible for removal from SVEP after three years. | Enables employers to reduce time spent in the SVEP to two years if they consent to an enhanced settlement agreement that includes use of a safety and health management system (SHMS). |
The final two updates included in the table above are intended to incentivize employers to fix problems quickly with solutions that ultimately work to transform the health and safety culture. The new SVEP instructions also add sample documents and guidance for specific situations to assist companies in complying.
Implementing a SHMS
Developing and implementing an SHMS is one of the best ways to help ensure a company does not end up in the SVEP. As stated in the table above, it is also a requirement for early removal from the SVEP. That is because a properly structured SHMS will get the processes, programs, and systems in place—and documented—to ensure the company is protecting employee safety and health and meeting OSH Act requirements.
OSHA requires the SHMS include the following Core Elements of the Safety and Health Program Recommended Practices:
- Management Leadership: Top management demonstrates a commitment to continuous improvement in safety and health, communicates that commitment to workers, provides adequate resources and support, and sets program expectations and responsibilities.
- Worker Participation: Workers understand their responsibilities and are involved in all aspects of the safety and health program, including setting goals, identifying reporting hazards, investigating incidents, communicating with management, and tracking progress.
- Hazard Identification and Assessment: Procedures are in place to continually identify workplace hazards and evaluate risks. Initial assessment of existing hazards, exposures, and control measures is followed by periodic inspections to identify new hazards; any incidents are also investigated to identify root causes.
- Hazard Prevention and Control: Employer and employees cooperate to identify and select methods for eliminating, preventing, or controlling workplace hazards according to the hierarchy of controls: engineering solutions, safe work practices, administrative controls, and personal protective equipment (PPE).
- Education and Training: Workers are trained to understand how the safety and health program works, how to recognize workplace hazards, and how to carry out their responsibilities under the program.
- Program Evaluation and Improvement: Processes are established to evaluate control measures for effectiveness, monitor program performance, verify program implementation, and identify opportunities to improve overall health and safety performance.
- Communication and Coordination for Host Employers, Contractors, and Staffing Agencies: Hosts commit to providing the same level of health and safety protection to all employees, communicating hazards present at the worksite, and resolving any conflicts that could impact safety or health.
Based on the plan-do-check-act cycle of continuous improvement, the SHMS should also include provisions for continually evaluating and improving program effectiveness and for OSHA’s review and evaluation. Finally, implementation must be verified by an independent third party (CSP, CIH, national union safety and health representative) subject to OSHA’s approval.
As usual, the best way to get ready for the increased enforcement is to understand the regulations and be prepared.
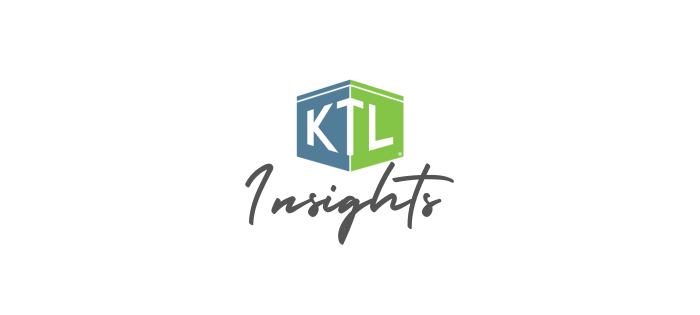
Comments: No Comments
Benefits of a Third-Party Safety Audit
Safe + Sound Week
You have not had any injuries. You have an onsite safety professional. You don’t have any high hazard operations onsite. You have few employees. You mostly use contractors and temporary workers. Whatever your situation, you may think that having a third-party audit of your safety programs and operations is an added expense that provides no real value.
In reality, a third-party safety audit can provide a valuable means of supporting ongoing safety performance and compliance, even beyond what an internal audit might provide. A third-party safety audit has the following advantages:
- Objectivity: Enlisting a qualified outside firm to audit your safety program provides a fresh set of unbiased eyes to assess aspects of your program internal staff may not consider. Third-party auditors offer broad perspective and knowledge of best management practices from conducting audits across industries. They maintain ongoing, up-to-date awareness of current and pending regulatory requirements that the organization should consider.
- Customizable: The audits themselves can be customized to fit the needs and goals of the organization. A third-party auditor can provide more direct coverage to evaluate specific program effectiveness and allow for a more focused understanding of existing strengths and improvement areas. Whether there is a desire to prepare for unannounced regulatory agency visits, review plans and programs, or even verify applicability, third-party audits can be built to suit the organization’s identified concerns and risks.
- Efficiency: Audits performed internally can take resources away from normal business operations. Third-party auditors work with the resources (or lack thereof) allocated to them to conduct an audit in a timely manner that does not negatively impact business functions.
- Validation: Third-party auditors validate existing programs and identify areas where best practices can be implemented to further protect the company. They assist in identifying issues before they become violations and identify root causes of continuing issues—focusing on corrective actions to be implemented. They can also provide data and reports that can be shared internally with employees to improve safety performance or externally with communities or customers to bolster the company’s image.
Every safety program needs to be continually reviewed and assessed to ensure it is meeting organizational goals and compliance requirements. Building a relationship with a third-party auditor is one way for organizations that are committed to a strong safety culture to:
- Take their safety program to the next level.
- Keep employees safe.
- Further protect the organization from a risk and compliance standpoint.
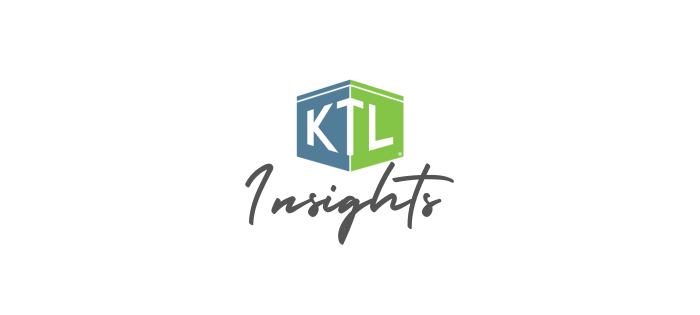
Comments: No Comments
Where Is Your Company on its Safety Journey?
Safe + Sound Week
Ralph Waldo Emerson famously said, “Life is a journey, not a destination.” The same could be said for safety. Workplace safety does not have a designated endpoint; rather, it is an ongoing journey—one in which new information is constantly being input, new technologies and innovations are constantly evolving, and employees are holding employers more accountable for ensuring a safe work environment.
Levels of Safety
How do you know where your organization falls on your safety journey? A recent webinar conducted by the Board of Certified Safety Professionals (BCSP) suggests organizations fall into one of four safety level that indicate the maturity of their safety program:
- Safety is not a major concern. Organizations on this level do not take an active role in the safety of their employees; instead, they are reactive to events that may occur. Their focus is generally on maximizing profits and minimizing costs. They are not future-looking, nor do they invest money in safety. This is typically the level where you see organizations with the most expensive fines and the most potential to cause serious damage to workers and/or their equipment.
- We do what is necessary to meet minimum safety requirements. This organization is still more concerned about costs over safety, so it is not significantly safer than an organization at the first level. That being said, the organization is at least meeting the bare minimum requirements, though blindly follows regulations just to avoid penalties. At this level, the organization will have only the required documentation and will not have a strong safety management system.
- We take a proactive approach to safety. The organization focuses on safety aspects that apply to their operations, is actively looking at other organizations in their industry for best practices, and utilizes leading indicators to drive safety improvements. These organizations understand that safety is an investment and, even more so, that the safety of their sites has direct impacts on their bottom line. These organizations go above the minimum requirements and show concern for the safety of their employees.
- Behavior-Based Safety (BBS) is in our blood. At the ultimate level, the organization understands how to help employees take an active role in their safety and actively encourages employees to exercise their rights to a safe work environment. In these organizations, employees are given positive reinforcement for actions taken to make the organization safer and are encouraged by management to watch out for each other rather than leaving the burden solely on the safety professional. There is an increase in morale, as safety is an integral part of the organization’s culture.
Moving Along Your Journey
Understanding where your organization is on its safety journey is the first step in creating a culture that embraces safety. This starts with assessing your safety programs, procedures, and policies; reviewing your safety metrics; and even surveying your staff to understand their attitudes about workplace safety.
As organizations move along in this journey, it is important to remember that a solid safety culture does not happen overnight. It takes ongoing work to build a robust and mature safety program where all employees contribute to a strong safety culture. And it takes ongoing work to maintain this culture, but the benefits are worth it:
- Fewer accidents, losses, and disruptions by preventing workplace injuries and illnesses
- Engaged employees and improved morale
- Increased productivity and enhanced overall business operations
- Lower workers’ compensation and insurance claims
- Improved compliance with OSHA regulations
- Improved reputation to attract new customers and employees and retain existing ones
- Better brand and shareholder value that tie to social responsibility
Where does your organization fall when it comes to safety? Where do you want it to be? And how can you get there?
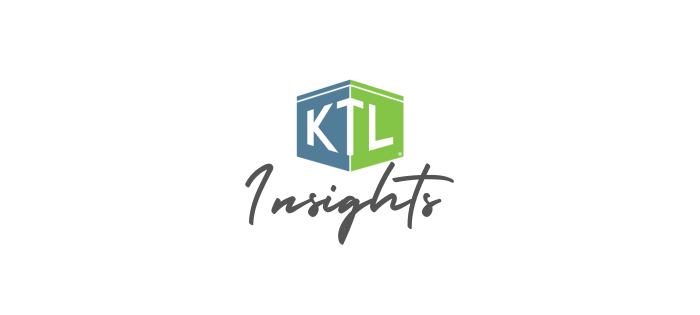
Comments: No Comments
Workers’ Compensation Audits
Safe + Sound Week
Workers’ compensation is tied directly to an organization’s safety program in that it provides medical and wage benefits to people who are injured or become ill at work. A strong safety program can reduce the likelihood of injuries and illnesses. When fewer work-related accidents and illnesses occur, workers’ compensation costs also become less expensive.
Getting Audit-Ready
The world of workers’ compensation is complex. Each state has different regulations that establish what is required of an organization and what premiums apply. One commonality across the board, however, is the workers’ compensation audit, which insurance companies conduct to make sure coverage and premiums match.
The following tips can help your organization prepare for a workers’ compensation audit and, in turn, improve your safety performance and save money over time.
- Inform yourself. Workers’ compensation audits are generally conducted within 35 days of when a premium is due or within 60 days of policy expiration. These audits are not done at random—they are mandatory. An auditor will contact the organization to send notice of the audit, which may be conducted via mail/email, phone, or field (i.e., in-person). When setting up the audit, it is important to ask, “What exactly should I have prepared to ensure a smooth and timely audit?” Carriers will gladly provide this information so the audit as painless and efficient as possible for all parties. Maintaining documentation is key, as organizations must provide the auditor with the information they request (i.e., employee, payroll, job descriptions) and ensure it is accurate. Not doing so is considered fraudulent activity.
- Project your payroll. While it is hard to see into the future, it is important to make sure your projected payroll is as accurate as possible to ensure you do not pay for additional exposure at a higher rate.
- Understand and expand your safety program. It can’t be emphasized enough—a strong safety program can reduce the likelihood of injuries or illnesses. Safety personnel should take an active role in understanding the workers’ compensation process, as there are important aspects of the safety system that can save the organization money if implemented correctly. Some of the important items that will be considered during the workers’ compensation audit may include:
- Personal protective equipment (PPE) program and availability
- Ergonomic evaluations
- Safety audits (i.e., frequency and type)
- Safety training
- Return-to-work programs
- Hiring practices (e.g., pre-employment evaluations, drug testing)
- Injury response protocols
- Medical evaluation programs
- Maintain contractor control. Having proper contractor control protects an organization from potential safety risks on many levels. For workers’ compensation, this involves ensuring all subcontractors and contractors have certificates of insurance, proper safety programs in place for the work that they will be doing, training for their employees, and supporting documentation for all these items.
Workers’ compensation audits can be a useful tool in an organization’s arsenal to identify gaps in your safety program that could create additional risk. Having your safety program and associated documentation in place will not only prepare the organization for a workers’ compensation audit, it should also improve overall safety performance and save money over time.
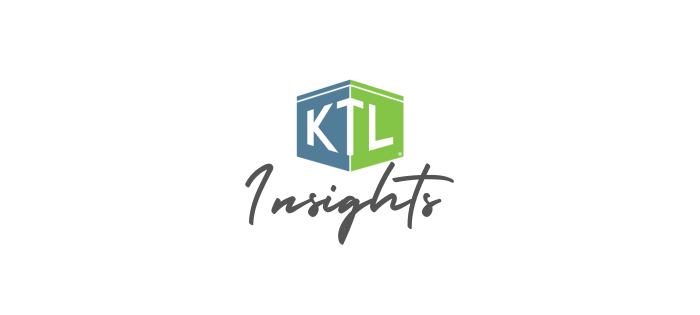
Comments: No Comments
Behavior-Based Safety 101
Safe + Sound Week
When an organization expresses the objective to have a strong safety culture, definitions can vary widely among top management as to what that actually means. According to the UK Health & Safety Commission, a safety culture is “the product of individual and group values, attitudes, perceptions, competencies, and patterns of behavior that determine the commitment to, and the style and proficiency of, an organization’s health and safety management.”
A strong safety culture has a number of characteristics in common. An organization’s safety culture is ultimately reflected in the way that safety is managed in the workplace, including the actionable steps that should be taken to reach the ultimate goal.
The Science of Behavior
Implementing a Behavior-Based Safety (BBS) approach is one way to create a robust safety culture. BBS involves applying the “science of behavior” to change real-world safety problems. Essentially, BBS aims to increase safe behavior while reducing hazards and risks by examining the motivation behind the underlying behaviors of workers. BBS relies on complete trust and cooperation between every employee—from top management to operation-level employees—to be successful.
Cooperation means working together to develop a strong safety program (e.g., management involving line workers in creating safety policies and procedures). It means that management seeks feedback from workers about safety issues—and uses that feedback to make improvements. And it means that there is no blame when incidents occur. Incident investigations focus on fact finding, not fault finding. Trust in the safety program, in senior management, and in each other is built when each of these characteristics is present and treated as a company-wide priority.
Creating a BBS Program
The hallmark of BBS programs is their aim to provide effective feedback, reinforcement, and recognition to the employees to improve safety conditions in the workplace and increase situational awareness based on behavioral observations. The Health and Safety Authority (HSA) recommends following these eight steps to create a BBS program:
- Create a team that will initiate the BBS program.
- List targeted behaviors that are deemed unsafe. These can be taken from safety audits, near miss reports, toolbox talks, etc.
- Create a BBS checklist that any employee can fill out completely when they observe an unsafe behavior. Behaviors should be:
- Observable (i.e., seen or heard)
- Reliable (i.e., witnessed the same way by more than one person)
- Something the employee can control
- Described in a positive way (i.e., what should be done vs. what shouldn’t be done)
- Objective (i.e., not based on opinions or interpretations)
- Determine the measurement system that can count the frequency of safe and unsafe behaviors.
- Conduct behavioral observations.
- Provide appropriate feedback depending on the behavior of the employees. Positive verbal feedback is a powerful way to reinforce safe behavior and a cornerstone of effective BBS.
- Use the data gathered from observing employees and make necessary changes.
- Work with employees determine which behavior(s) or process(es) needs improvement.
BBS is an effective tool for involving all employees in creating a strong safety culture—one that employees will not only buy into but embrace as the way the organization does business. Done effectively, BBS creates the positive reinforcement, non-judgmental feedback, leadership influence, and an environment of trust that are all key characteristics of a strong safety culture.
Does your organization rely on BBS to support its safety culture?
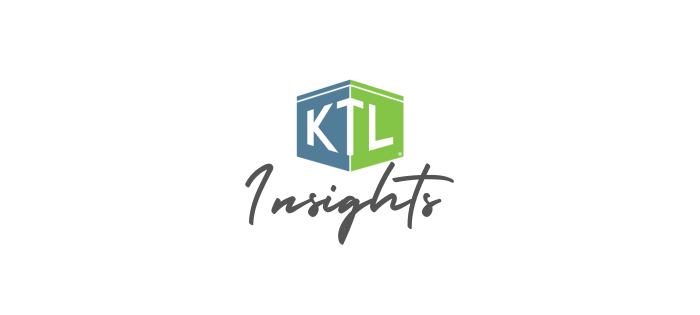
Comments: No Comments
Hearing Employee Safety Concerns
Safe + Sound Week
Safety programs work when employees actively participate in them. According to the U.S. Department of Labor, they tend to work even better when employees are involved in establishing, operating, evaluating, and improving them. That is because employees know and understand the potential hazards of doing their jobs.
Top of the List
Many different organizations have conducted surveys on the top safety concerns for workers. The identified concerns often vary by industry due to the types of job activities performed. And, not surprisingly, some concerns align with the Occupational Safety and Health Administration’s (OSHA’s) Top 10 Safety Violations (e.g., trips, slips, and falls).
Regardless industry, there are similarities in some of the health and safety concerns employees have, particularly in those organizations with barriers to effective safety communication. Some of the top health and safety issues that are often overlooked by employers—and ones that don’t necessarily hit OSHA’s Top 10— include the following:
- Stress and distractions. The National Institute for Occupational Safety and Health (NIOSH) defines job stress as “the harmful physical and emotional responses that occur when the requirements of the job do not match the capabilities, resources, or needs of the worker. Job stress can, in turn, lead to poor health and even injury.” Long days, increased workload, and increased competition for workers’ attention can lead to lower productivity, more physical and mental illnesses, and the inability to anticipate potential hazards.
- Poor ergonomics. According to the Bureau of Labor Statistics, one-third of worker injury and illness cases are musculoskeletal disorders resulting from poor ergonomics. Workers across all industries are at risk of musculoskeletal injuries from things like repetitive tasks, lifting heavy objects, or working at a desk for prolonged periods of time without proper breaks.
- Spread of illnesses. One positive outcome of the COVID-19 pandemic is the increased awareness of the risks associated with spreading illnesses in the workplace. Workers are more cognizant of those with illnesses around them and, subsequently, are becoming less hesitant to call off work if they are feeling under the weather.
- Working alone. While working alone is common in many industries, that does not make the practice inherently safe. Working alone and/or without proper surveillance means workers are at an increased risk of serious injury with no one to call for help or to provide medical attention in the event an incident occurs.
- Temporary workers. With staffing shortages impacting nearly every industry, temporary workers are becoming more common. Unfortunately, temporary workers are the most likely to perform dangerous tasks due to inadequate training on job-specific hazards. This lack of adequate training is not only a risk to the temporary worker, but also to any permanent workers who work along side them. Workers are aware of the lack of safety-specific training for temporary workers and feel the responsibility falls unduly on to them.
Addressing Concerns
Not every employee feels safe to bring up safety concerns with their company. It is important that organizations have many avenues available for employees to bring forward issues they see in a way that is comfortable for them and without retribution. These avenues can be weekly safety meetings as a team, a monitored company email address, or even something as simple as an anonymous suggestion box. Giving adequate time to listening to employee safety concerns increases trust between workers and the company, shows leadership consistency, and aids in employee retention.
Can your company bear the cost of your employees’ concerns falling on deaf ears?
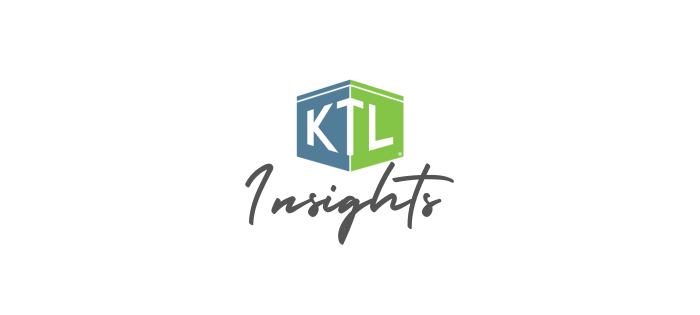
Comments: No Comments
OSHA Safe + Sound Week: August 15-21, 2022
According to the Occupational Safety and Health Administration (OSHA), “Safe workplaces are sound workplaces.” An organization’s safety culture is ultimately reflected in the way that safety is managed in the workplace, and having a strong safety and health program can help create:
- Fewer accidents, losses, and disruptions by preventing workplace injuries and illnesses
- Engaged employees and improved morale
- Increased productivity and enhanced overall business operations
- Lower workers’ compensation and insurance claims
- Improved compliance with OSHA regulations
- Improved reputation to attract new customers and employees and retain existing ones
- Better brand and shareholder value that tie to social responsibility
These benefits are precisely why the OSHA created Safe + Sound as a year-round campaign: to encourage every workplace to develop, implement, and maintain a safety and health program.
Safe + Sound Week
One week out of the year—August 15-21, 2022—OSHA promotes a nationwide “Safe + Sound Week” to recognize the successes of workplace health and safety programs, offer information and ideas on how to keep America’s workers safe, and encourage America’s workplaces to commit to workplace safety and health.
OSHA recommends that every workplace have a safety and health program that includes the following three major areas:
- Management leadership. Management must provide the leadership, vision, and resources needed to implement an effective safety and health program. This means that business owners, managers, and supervisors commit to:
- Making worker safety and health a core organizational value.
- Eliminating hazards, protecting workers, and continuously improving workplace safety and health.
- Providing sufficient resources to implement and maintain a strong safety culture.
- Visibly demonstrating and communicating their ongoing commitment to safety and health.
- Worker participation. Engaging workers at all levels in establishing, implementing, evaluating, and improving safety and health in the workplace creates buy-in. Workers are a valuable partner in making the workplace safer, and maximizing participation (without risk of retaliation) allows everyone to feel invested in the program.
- Systematic approach to finding and fixing hazards. Finding and fixing hazards in the workplace is an ongoing process to better identify and control sources of potential injuries or illnesses. This can involve establishing procedures to collect and review information about known or potential hazards, investigating the root cause of those hazards, and prioritizing hazard controls. This continual process ensures that workers go home to their families safe and sound every night.
KTL’s Series on Investing in Safety
Throughout OSHA’s Safe + Sound Week (August 15-19), KTL will be featuring a series of articles and posts on our blog and social media (i.e., Facebook, LinkedIn, Twitter) reinforcing these concepts from OSHA and discussing why businesses should invest in safety. Topics will include the following:
- Where is your company on its safety journey?
- Top employee safety concerns and why they need to be heard
- Worker compensation audits, what to expect, and how you can save money
- Behavior-based safety – what is it?
- Benefits of a third-party safety audit
Watch for these articles! And for more information on Safe + Sound and what your organization can do to participate and promote a strong safety culture, visit https://www.osha.gov/safeandsound.